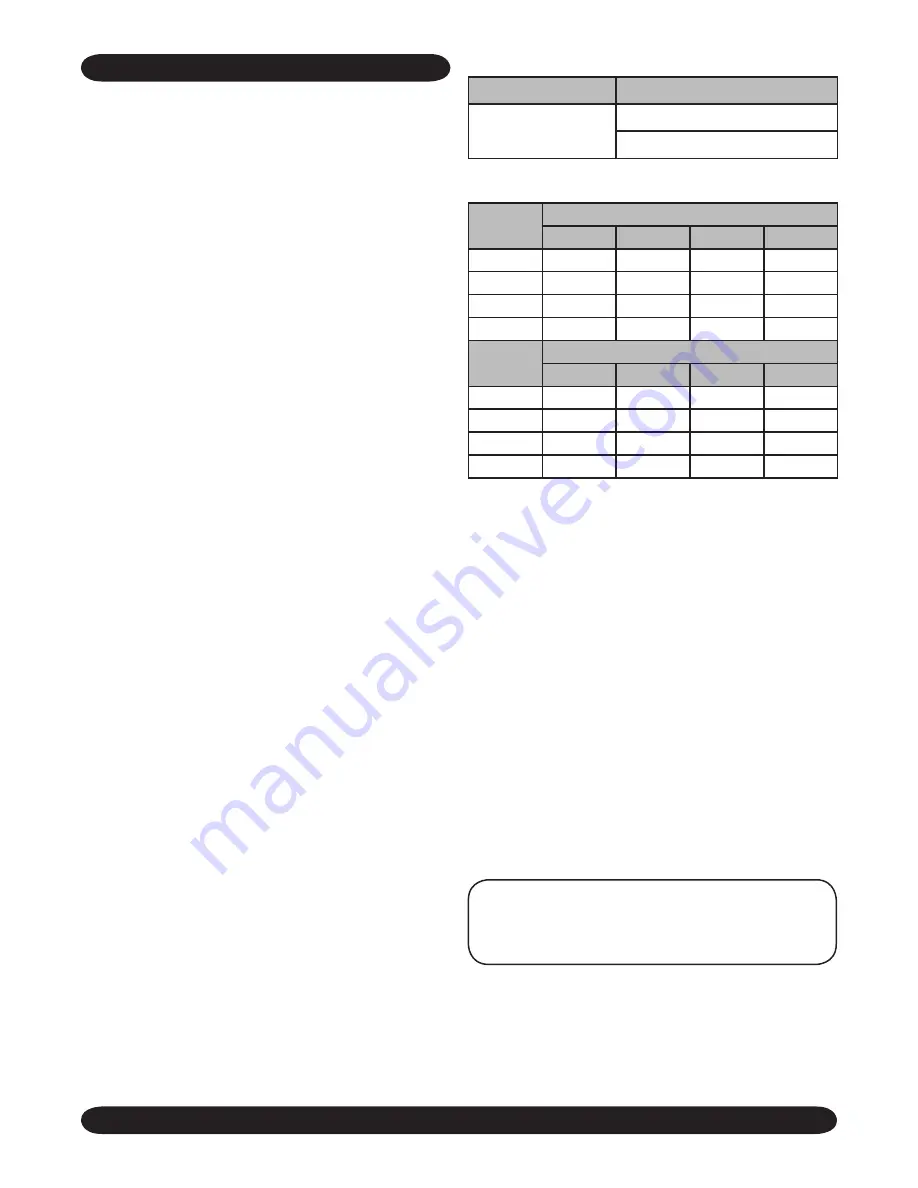
8
Existing ductwork should be assessed for its air
handling capabilities. For residential applications,
the recommended air velocity of a supply air trunk
duct is 700 feet per minute (fpm), and should not
exceed 900 fpm. The recommended air velocity of
a supply air branch run is 600 fpm, and should not
exceed 900 fpm. These values are slightly lower
for flexible ducting. The recommended air velocity
of a return air trunk duct is 600 fpm, and should not
exceed 700 fpm. The recommended and maximum
air velocity of a return air branch 600 fpm.
The
“Equal Friction Chart,”
as published by
ASHRAE and HRAI, is the basis for the various air
duct calculators available through heating supply
companies. Following the air velocity guide lines,
according to the
“Equal Friction Chart,”
or a slide
rule air duct calculator, a typical 6” round duct has
a capacity of approximately 100 cfm.
NOTE:
The return air system is equally as important as
the supply air system. An under-sized return air system will
prevent sufficient quantities of air from reaching the supply
air system and will consequently reduce the service life of
the furnace and its components.
3 - FURNACE SIZING
The maximum hourly heat loss for each heated
space shall be calculated in accordance with the
procedures described in the manuals of the
Heat-
ing, Refrigeration and Air Conditioning Institute of
Canada (HRAI)
, or by any other method which is
suitable for local conditions, provided the results
obtained are in substantial agreement with, and
not less than those obtained using the procedure
described in their manuals.
In the United States,
“Manual J - Load Calculation,”
published by the Air Conditioning Contractors of
America, describes a suitable procedure for calcu-
lating the maximum hourly heat loss.
If the installation is a retrofit application, do not rely
on the capacity of the existing heating equipment
as a method to size the new furnace. Many of the
heat transfer multiples listed in earlier versions of
load calculation manuals were much higher than
those listed in more recent editions. It is possible
that energy saving measures have been completed
since the installation of the existing furnace. This
might include additional insulation in the attic or
walls, the application of sprayed foam insulation,
the addition of storm windows and doors, weather-
stripping, caulking, etc.
Many of the older furnaces were equipped with large
belt drive blower systems, operating at low RPM’s.
If replacing an existing furnace, be sure that the
existing ductwork can handle the amount of airflow
necessary for a reasonable temperature rise. Most
older gas furnaces operated with a system temper-
ature rise of 70 - 100°F. This furnace is designed
to be operated with a system temperature rise
(∆T) of High Fire 35 - 65°F, Low Fire 25 - 55°F.
If the furnace selected has an identical output
capacity as the original furnace, a substan-
tial increase in system air flow will be required.
See Tables 1A and 1B
(below)
and the airflow
characteristics in Section 20 of this manual,
“Airflow.”
TABLE 1B - AIR FLOW FOR TEMPERATURE RISE
Furnace
Model
High Fire (HF) CFM Required for a ▲T of:
35
45
55
65
60
1501
1167
955
808
80
2001
1557
1274
1078
100
2502
1946
1592
1347
120
3002
2335
1910
1616
Furnace
Model
Low Fire (LF) CFM Required for a ▲T of:
25
35
45
55
60
901
700
573
485
80
1201
934
764
647
100
1501
1167
955
808
120
1801
1401
1146
970
TABLE 1A - RANGE OF TEMPERATURE RISE
Furnace Model
Temperature Rise
60, 80, 100, 120
High Fire (HF) 35 - 65°F
Low Fire (LF) 25 - 55°F
Содержание G95V
Страница 27: ...27 FIGURE 21A DIRECT VENT TERMINAL CLEARANCES...
Страница 28: ...28 FIGURE 21B NON DIRECT VENT TERMINAL CLEARANCES...
Страница 53: ...53 22 WIRE DIAGRAM FOR TWO STAGE FURNACE WITH ECM...