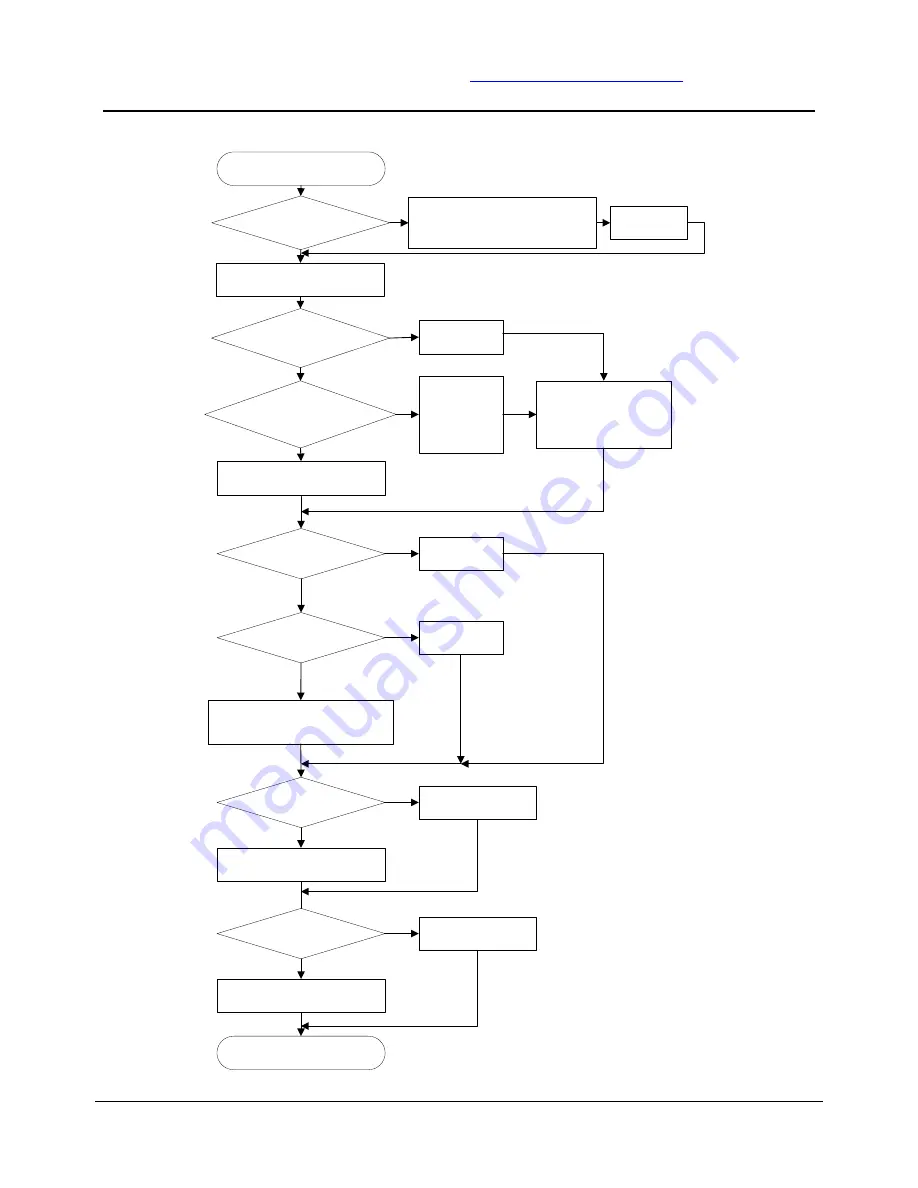
V&T Technologies Co., Ltd.
http://www.ecodrivecn.com
Appendix B Control Mode Setting Process
129
Closed loop setting process (continued)
Deceleration stop?
First DC braking after
begin to run from the startup
frequency?
Begin to run from the
startup frequency
Setting P3.00=0
Setting startup frequency
P3.03 and startup frequency
retention time P3.04
Free stop?
Anti-reverse?
Setting P3.09=1
DC braking stop, setting P3.05=2, setting
P3.06, P3.07 and P3.08 properly (For the
meaning, refer to Chapter 6 Parameter
Description)
Dynamic braking?
Setting PA.09=0
Setting P3.00=1
DC braking
current P3.01 and
retention time of
braking keep
P3.02
Rotation speed tracing startup, setting
P3.00=2
Setting P3.05=0
Setting P3.05=1
Setting P3.09=0
Setting PA.09=1
END
N
Y
N
Y
N
Y
N
Y
N
Y
N
Y
Select multi acceleration/
deceleration time?
Select function of X terminal acceleration/
deceleration time?
(For details, refer to the function description
of P5.00 to P5.006 in Chapter 6)
Setting correct
P4.09
~
P4.14
Setting P0.08 and P0.09
N
Y
JOIN THE PAGE