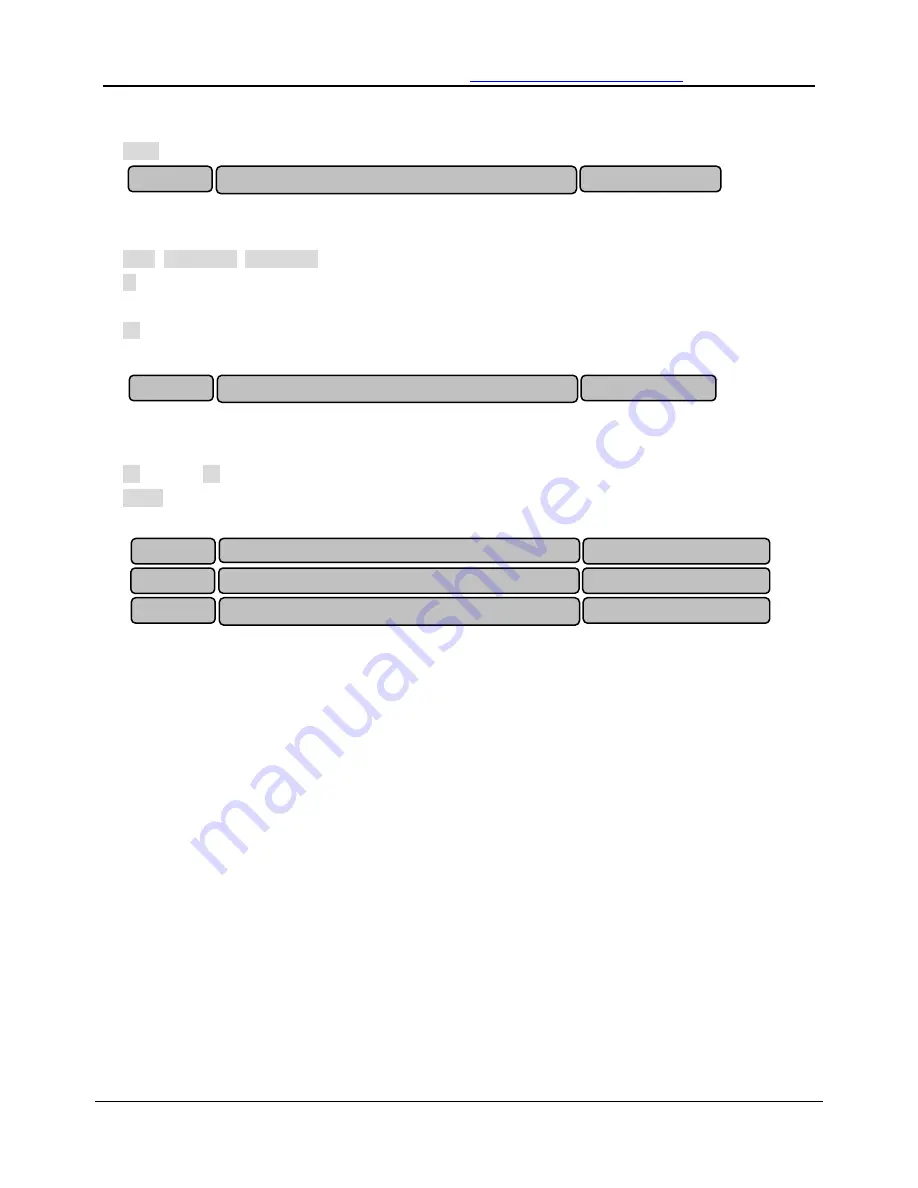
V&T Technologies Co., Ltd.
http://www.ecodrivecn.com
Chapter 6 Parameter Description
55
the analog and the reference frequency is defined by group P6.
Note: When adopting the current input of 0~20mA, refer to the description of P6.01~P6.08. .
Three different operating command reference modes can be selected for the inverter.
0: Operation panel mode: Perform the Run, Stop, Forward/reverse operation of the inverter through the
RUN, STOP/RST, FWD/REV buttons of the operation panel.
1: Terminal mode: Perform the Run, Stop, Forward/reverse operation of the inverter by defining the
multi
−
functional terminals X1~X4. Refer to the description of P5.00~P5.06 and P5.11.
2: Host computer mode: Perform the Run, Stop, Forward/reverse operation of the inverter through
communication. Refer to the appendix A Modbus communication protocol.
This parameter is used to change the rotation direction of the motor under operation panel running
command reference mode (P0.06=0).
0: Forward; 1: Reverse
Note: This function code is invalid under terminal running command reference mode, and the running
direction is controlled by terminal command.
This function can set the speed and stability in the duration from acceleration to constant speed after the
startup of the inverter, or from constant deceleration to stop.
Acceleration time 0: The time that the inverter accelerate from 0 frequency to maximum frequency.
Deceleration time 0: The time that the inverter accelerate from maximum frequency to 0 frequency.
S curve time: The time for adding curve segment to improve the smoothness of the start and ending
section during the acceleration and deceleration, P0.10. S curve time is applicable to the belt conveyer
that carries fragile materials or applications requiring smooth speed adjustment.
P0.06
Running command reference mode
0~2(0)
P0.10
S curve time
0.0~3600.0 s(0.0s)
P0.07
Running direction command
0~1(0)
P0.08
Acceleration time 0
0.1~3600.0 s(6.0s or 20.0s)
P0.09
Deceleration time 0
0.1~3600.0 s(6.0s or 20.0s)