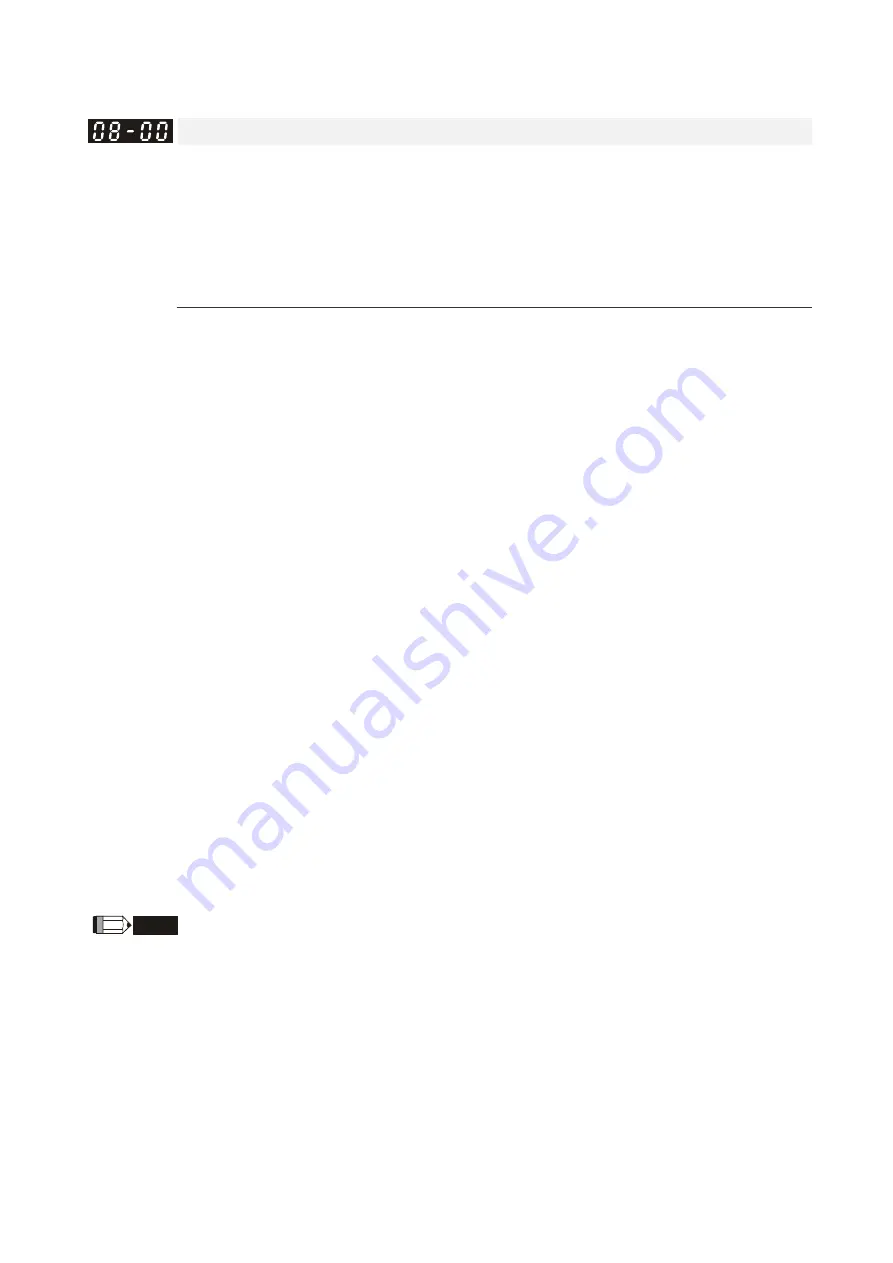
Ch12 Descriptions of Parameter Settings
| VFD-ED
12-70
08 PM Parameters
: You can set this parameter during operation.
Motor Auto-tuning
Control Mode
FOCPM
Default:
0
Settings
0: No function
1: Only for an unloaded motor; auto-measures the angle between magnetic pole
and PG origin (Pr.08-09)
2: Auto-tuning PM parameters (suggested to lock the brake)
3: Auto-measures the angle between magnetic pole and PG origin (Pr.08-09)
Position the elevator near the middle floors before auto-tuning.
Auto-tuning process: 2, and then 1 or 3.
Motor auto-tuning:
Set Pr.08-00 to 1 to 3, and then press the RUN key on the digital keypad KPC-CC01 (Pr.00-15=2) to start
auto-tuning. Or when the drive is in manual mode (inspection), run the upward operation or downward
operation (Pr.00-15=1) to start auto-tuning immediately. In the process of auto-tuning, an “Auto tuning”
warning continuously displays on the digital keypad until it is finished.
Pr.08-00=2: Motor auto-tuning is static test:
1. Make sure that all the drive parameters are set to defaults and the motor wiring is correct.
2. Enter the correct values for Pr.01-01, Pr.01-02, Pr.08-01, Pr.08-02, Pr.08-03 and Pr.08-04. Refer to
motor capacity to set the acceleration/deceleration time.
3. Note that the motor will run! The shaft needs to be locked by an external force.
4. After auto-tuning is finished, check if Pr.08-05, Pr.08-07, and Pr.08-08 all have values.
Pr.08-00=1: Auto-measures the angle between the magnetic pole and the PG origin. Pay attention to the
following notes when measuring: (dynamic test)
1. Unload before auto-tuning.
2. If the drive controls the brake, the drive can auto-tune according to the normal sequence after you
complete the wiring and set the brake control parameters.
3. If the host controller controls the brake, make sure that the brake is in release status before
auto-tuning.
Pr.08-00=3: Auto-measures the angle between the magnetic pole and the PG origin. Pay attention to the
following notes when measuring: (static test)
1. The motor can be loaded or unloaded before auto-tuning.
2. See the reference table for auto-tuning for Pr.10-00 (PG Signal Type).
3. If the drive controls the brake, the drive can auto-tune according to the normal sequence after you
complete the wiring and set the brake control parameters.
4. If the host controller controls the brake, make sure that the brake is in release status before
auto-tuning.
5. Make sure the setting for Pr.10-02 is correct. Incorrectly setting Pr.10-02 causes incorrect positioning
of the magnetic pole and results in the wrong angle between the magnetic pole and PG origin.
NOTE
The entered rated speed cannot be larger than or equal to 120 f/p.
Note that if the contactor and brake are not controlled by the AC motor drive, release it manually.
Set Pr.08-00 to 1 (unloaded motor) for accurate calculation. If you need to execute this function with
a loaded motor, balance the carriage before execution.
If you do not balance the carriage in a measured environment, you can execute this function with a
loaded motor by setting Pr.08-00= 3. It will have a difference of 15–30
o
for different encoder types.
“Auto Tuning Err” displays on the digital keypad when stopping due to an AC motor drive fault or
human error, which means the detection fails. Check the wiring connections of the AC motor drive If
“PG Fbk Error” displays on the digital keypad, change the setting of Pr.10-02 (if set to 1, change it to
2). If “PG Fbk Loss” displays on the digital keypad, check the feedback of Z-phase pulse.
Содержание VFD-ED Series
Страница 3: ......
Страница 10: ...Ch01 Introduction VFD ED 1 3 1 2 Model Name 1 3 Serial Number...
Страница 21: ...Ch01 Introduction VFD ED 1 14 Built In Keyboard Panel KPED LE01 Unit mm inch...
Страница 26: ...Ch02 Installation VFD ED 2 5 Ambient Temperature Derating Curve Altitude Derating Curve...
Страница 27: ...Ch02 Installation VFD ED 2 6 The page intentionally left blank...
Страница 28: ...Ch03 Wiring VFD ED 3 1 Chapter 3 Wiring 3 1 Wiring 3 2 System Wiring Diagram...
Страница 30: ...Ch03 Wiring VFD ED 3 3 3 1 Wiring...
Страница 32: ...Ch03 Wiring VFD ED 3 5...
Страница 38: ...Ch04 Main Circuit Terminals VFD ED 4 3 4 1 Main Circuit Diagram Frame B Frames C D Frame E...
Страница 46: ...Ch05 Control Terminals VFD ED 5 3 Frame E Step 1 Step 2 Step 3...
Страница 47: ...Ch05 Control Terminals VFD ED 5 4 5 2 Control Terminal Specifications...
Страница 51: ...Ch05 Control Terminals VFD ED 5 8 The page intentionally left blank...
Страница 93: ...06 Optional Accessories VFD ED 6 42 EMC Filter Model B84143D0075R127 B84143D0090R127 Unit mm inch...
Страница 94: ...06 Optional Accessories VFD ED 6 43 EMC Filter Model B84143D0150R127 Unit mm inch...
Страница 95: ...06 Optional Accessories VFD ED 6 44 EMC Filter Model B84143D0200R127 Unit mm inch...
Страница 96: ...06 Optional Accessories VFD ED 6 45 EMC Filter Model B84142A0042R122 Unit mm inch...
Страница 242: ...Ch12 Descriptions of Parameter Settings VFD ED 12 31 Elevator Timing Diagram...
Страница 313: ...Ch12 Descriptions of Parameter Settings VFD ED 12 102 The page intentionally left blank...
Страница 317: ...Ch13 Warning Codes VFD ED 13 4 The page intentionally left blank...
Страница 329: ...Ch14 Fault Codes VFD ED 14 12 The page intentionally left blank...
Страница 351: ...Ch16 Safe Torque Off Function VFD ED 16 10 16 5 6 STL1 Figure 6 16 5 7 STL2 Figure 7...
Страница 353: ...Ch16 Safe Torque Off Function VFD ED 16 12 The page intentionally left blank...
Страница 373: ...Appendix A EMC Standard Installation Guide VFD ED A 20 The page intentionally left blank...
Страница 389: ...Appendix B Revision History VFD ED B 16 The page intentionally left blank...