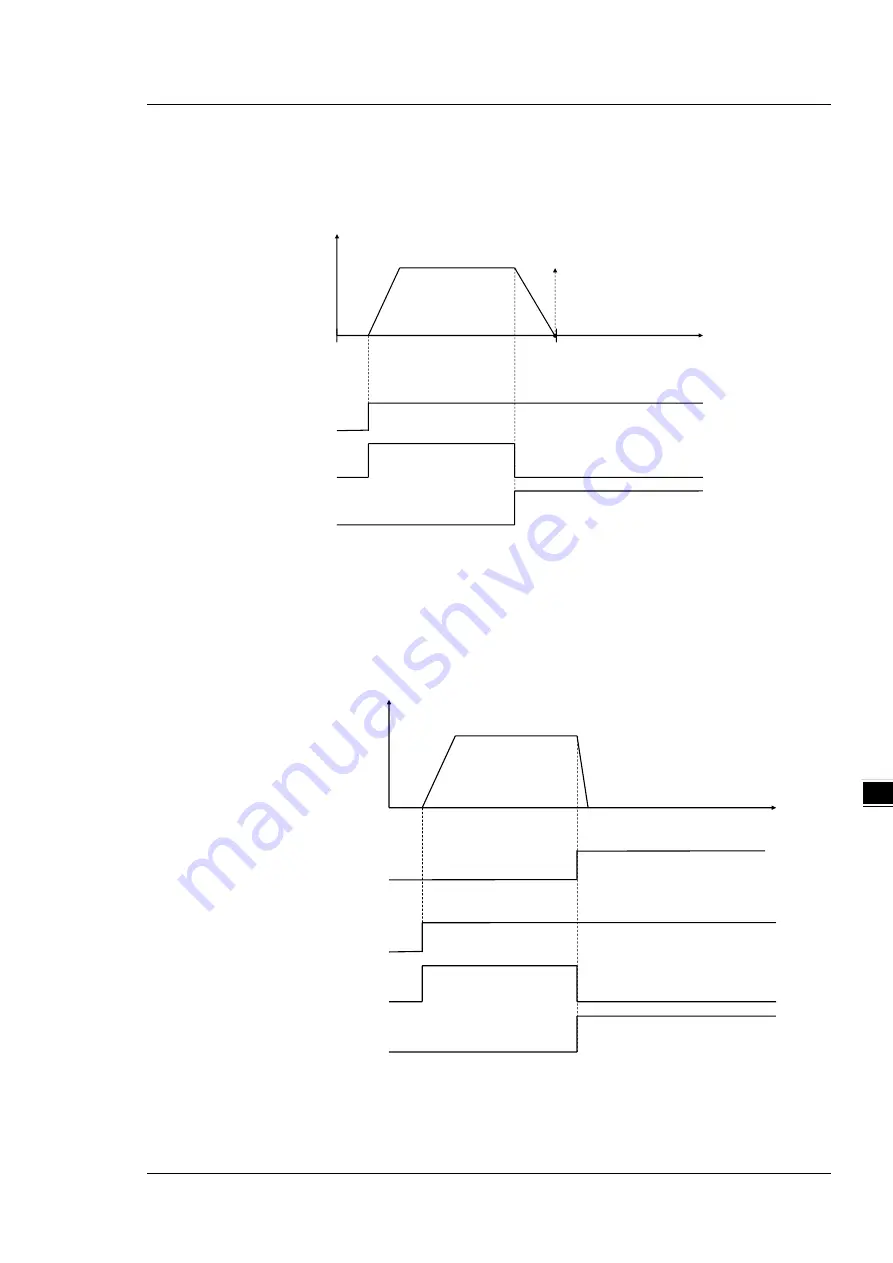
C h a p t e r 7 M o t i o n C o n t r o l B a s i c S e t t i n g s & O p e r a t i o n
7 - 7 1
7_
-
Use function block MC_MoveRelative and activate the function block when the position reaches 11,000.
After the axis moving to about 8,000, Busy of the function block will shift from TRUE to FALSE, while
CommandAborted shifts from FALSE to TRUE. The axis then starts to decelerate and stop at the position
inside software limit
Hardware limit:
Since the EtherCAT servo wires carry the hardware limit signals, the stop method for hardware
limit may be different between companies and brands. The following description takes Delta
ASDA-A2-E servo
drive as example:
-
Use MC_Jog function block to perform axis rotating in positive direction. Once the hardware
limit is reached during the rotation,
ASDA-A2-E servo drive will be stopped and report
error messages via communication.
After using MC_Reset to clear errors for reaching software/ hardware limit, the system synchronizes the
command positon with the values of return position automatically and move away from the direction of limit so as
to operate properly.
Position
Velocity
Execute
MC_MoveRelative
Busy
CommandAborted
10000
0
9992
Position
Velocity
JogForward
MC_Jog
Busy
CommandAborted
Hardware limits
Содержание AX-3 Series
Страница 17: ...AX 3 Series Operation Manual 1 10 _1 MEMO...
Страница 54: ...AX 3 Series Operation Manual 3 22 _3 MEMO...
Страница 98: ...AX 3 Series Operation Manual 4 44 _4 MEMO...
Страница 118: ...AX 3 Series Operation Manual 6 8 _6 MEMO...
Страница 148: ...AX 3 Series Operation Manual 7 30 _7 Scan PLC controller Add the newly scanned PLC controller and click OK...
Страница 241: ...Chapter 7 Motion Control Basic Settings Operation 7 123 7_ Click to enter Axis 0 tab on PoAxis Configuration page...
Страница 292: ...AX 3 Series Operation Manual 7 174 _7 Jerk Done MC_MoveSuperImposed_Done Busy CommandAborted Error ErrorID...
Страница 310: ...AX 3 Series Operation Manual 8 18 8_ MEMO...
Страница 355: ...Appendix A Troubleshooting A 5 _A...