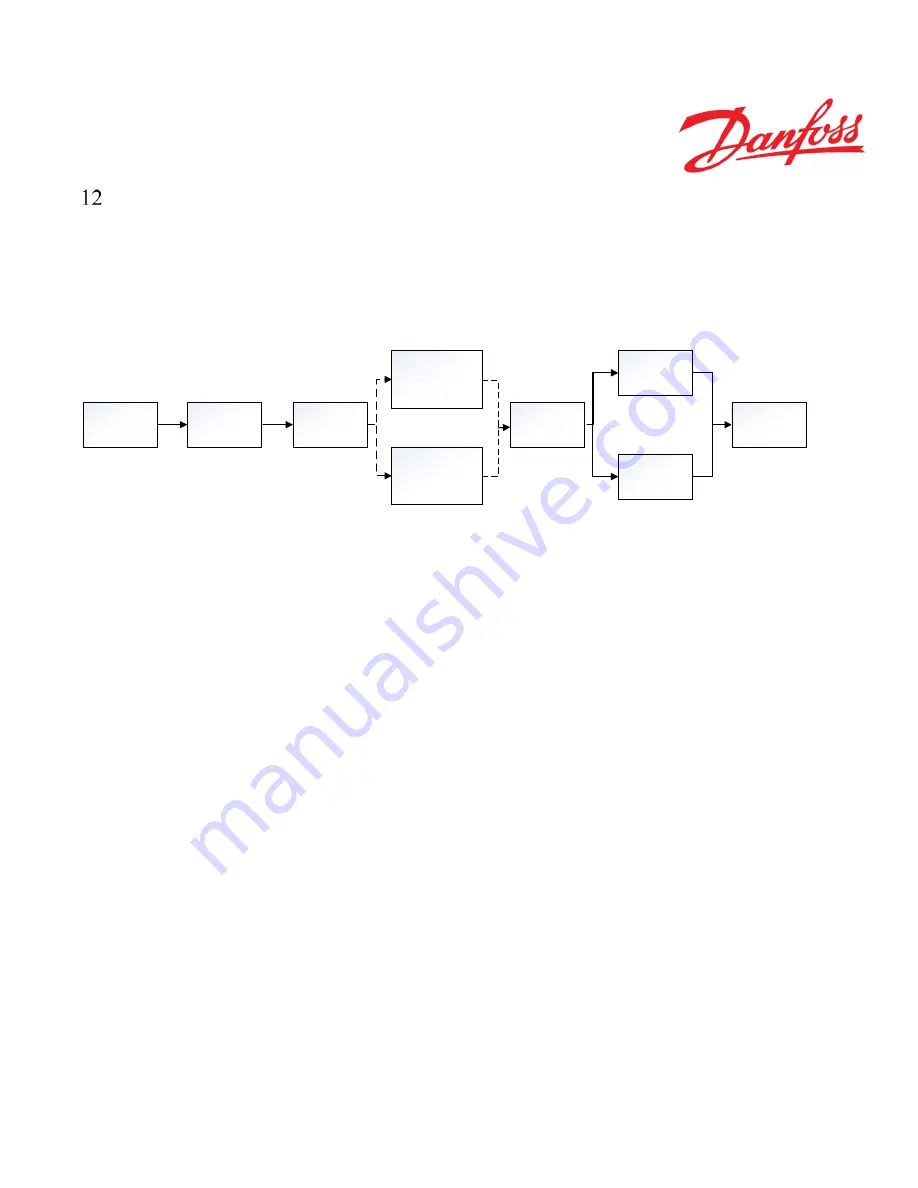
© Danfoss | August 2018
AQ00000211 |
119
ENGINEERING TOMORROW
Auto-guidance steering
When the PVED-CLS is in off-road steering mode (see Figure ) the Auto-guidance steering can be chosen. Furthermore,
the PVED-CLS can be configured in such a way, that two auto-guidance controllers (GPS and GPS2) can be interfaced.
Two safety functions for auto-guidance controllers (GPS and GPS2) can be configured, which can be enabled and run
simultaneously. In addition, these functions are dependent on the vehicle’s speed and can limit the maximum wheel angles
and flow allowed in Auto-guidance steering.
12.1
BLOCK DIAGRAM
GMC to WA
setpoint
Vehicle speed
dependent
wheel angle
limitation
GPS algorithm type v1:
Vehicle speed
dependent
flow command limitation
GPS algorithm type v2:
Vehicle speed
dependent
Wheel angle
speed limitation
Vehicle speed
dependent
closed loop control
Flow command
filter
Control / no control
decision
Flow to spool
position convertion
SVC
Note:
GPS algoritm type v1 or v2 needs to be selected
Figure 63
12.2
SELECTION OF GPS ALGORITHM TYPE
It is possible to select GPS algorithm type:
GPS v1: Vehicle speed dependent flow limitation
GPS v2: Vehicle speed dependent wheel angle speed limitation.
Selection is done from the service tool under GPS config in parameter P3496: GPS Algorithm type.
GPS v1:
If the max WA and cylinder size are unknown.
If a series of machines will not have variation in cylinder size and max WA (same lock stops position across
fleet).
If the lock stops are changed after tuning and the WA is re-calibrated at it should, it will influence the system
gain.
Unless the max angles are updated, the curvature to angle conversion will not be accurate. Further the gain in
the system will change. Small changes will have limited influence in steering accuracy, but if WA is halved or
doubled, the steering inaccuracy will increase
Содержание PVED-CLS
Страница 6: ...6 Danfoss August 2018 AQ00000211 ENGINEERING TOMORROW ...
Страница 71: ... Danfoss August 2018 AQ00000211 71 ENGINEERING TOMORROW Figure 29 ...
Страница 127: ... Danfoss August 2018 AQ00000211 127 ENGINEERING TOMORROW ...
Страница 147: ... Danfoss August 2018 AQ00000211 147 ENGINEERING TOMORROW ...
Страница 182: ...182 Danfoss August 2018 AQ00000211 ENGINEERING TOMORROW ...