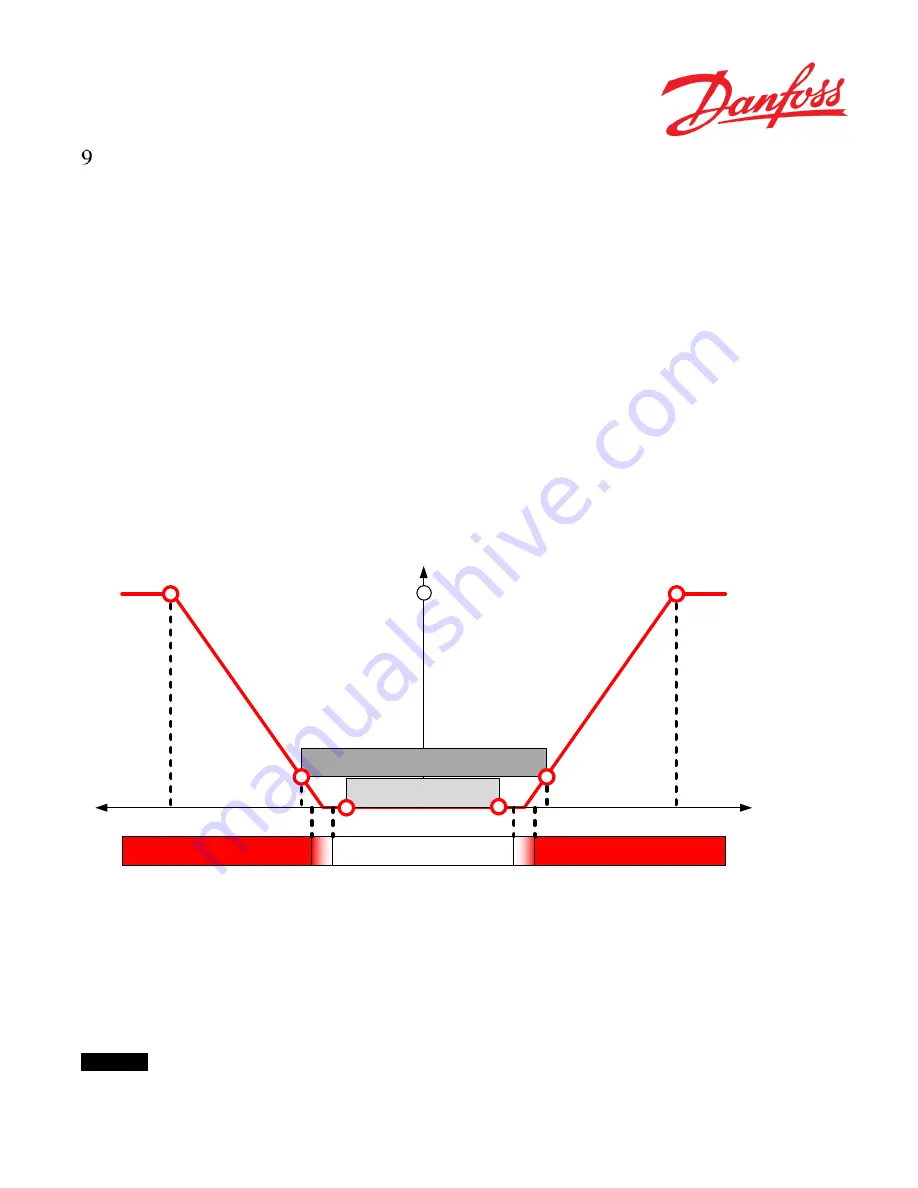
54 | © Danfoss | August 2018
AQ00000211
ENGINEERING TOMORROW
Calibration
A PVED-CLS shall always be calibrated to the valve it is controlling (OSPE, EHPS, EHi-E or EHi-H). This allows
cancellation of mechanical, electrical and environmental dependent tolerances. Spool calibration also compensates for the
mechanical dead-bands designed into the EH spool. Spool calibration is only required at first installation or after PVED-
CLS replacement. PVED-CLS utilizes two types of dead bands: close loop dead band used in Auto-guidance mode and
open loop dead band used in EH steering features.
When using PVED-CLS for fast steering, correctly calibrated dead-bands values (P1 and P2) are important.
If P1 and P2 are too-close-to-neutral (conservative values), no EH flow will be added at low steering wheel RPM,
causing understeer. If P1 and P2 are further away from neutral than they should be (aggressive values), EH-flow
contribution will be higher than expected at low RPM.
For AUX mini-wheel steering, having P1 and P2 too-close-to-neutral (conservative values) causes no steering at low
mini-wheel steering RPM. If P1 and P2 are too far away from neutral (aggressive values) jerky mini-wheel steering,
when steering motion starts.
For open loop joystick, having P1 and P2 too-close-to-neutral (conservative values) causes extra perceived dead-band in
the joystick. If P1 and P2 are too far away from neutral (aggressive values) makes it impossible to steer small amounts
of flow, potentially leading to jerk.
For closed loop joystick having P1 and P2 too-close-to-neutral (conservative values), will cause slight increase in
possible steady state error. If P1 and P2 are too far away from neutral (aggressive values) could cause the wheels never
to settle at a position (oscillation around the set-point).
Flow range
Hydraulic deadband
Flow range
Open Loop mode
Close Loop mode
L
R
(P3162)
(P3164)
(P3088)
(P3166)
(P3168)
P1
P2
P1: (P3166 + P3170)
P2: (P3168 - P3170)
Spool displacement
Maximum flow
Flow, Q
(L/min)
Figure 2
Close loop mode for auto-guidance are placed further away from neutral. They should be placed where definite, yet
small oil output of the EH spool is achieved.
This is to eliminate steady state error between wheel angle and its set-point. The PVED-CLS will potentially oscillate a
bit around steady state, but in auto-guidance there is never a steady state set-point.
If dead-bands are too far away from neutral, jerky steering at small flow can be observed, and if placed further in
towards neutral it will lead to undesired periods of no EH flow output.
Important
Danfoss recommend to perform calibration under the following circumstances:
•
Oil temperature during calibration routine should be at normal operating condition.
Содержание PVED-CLS
Страница 6: ...6 Danfoss August 2018 AQ00000211 ENGINEERING TOMORROW ...
Страница 71: ... Danfoss August 2018 AQ00000211 71 ENGINEERING TOMORROW Figure 29 ...
Страница 127: ... Danfoss August 2018 AQ00000211 127 ENGINEERING TOMORROW ...
Страница 147: ... Danfoss August 2018 AQ00000211 147 ENGINEERING TOMORROW ...
Страница 182: ...182 Danfoss August 2018 AQ00000211 ENGINEERING TOMORROW ...