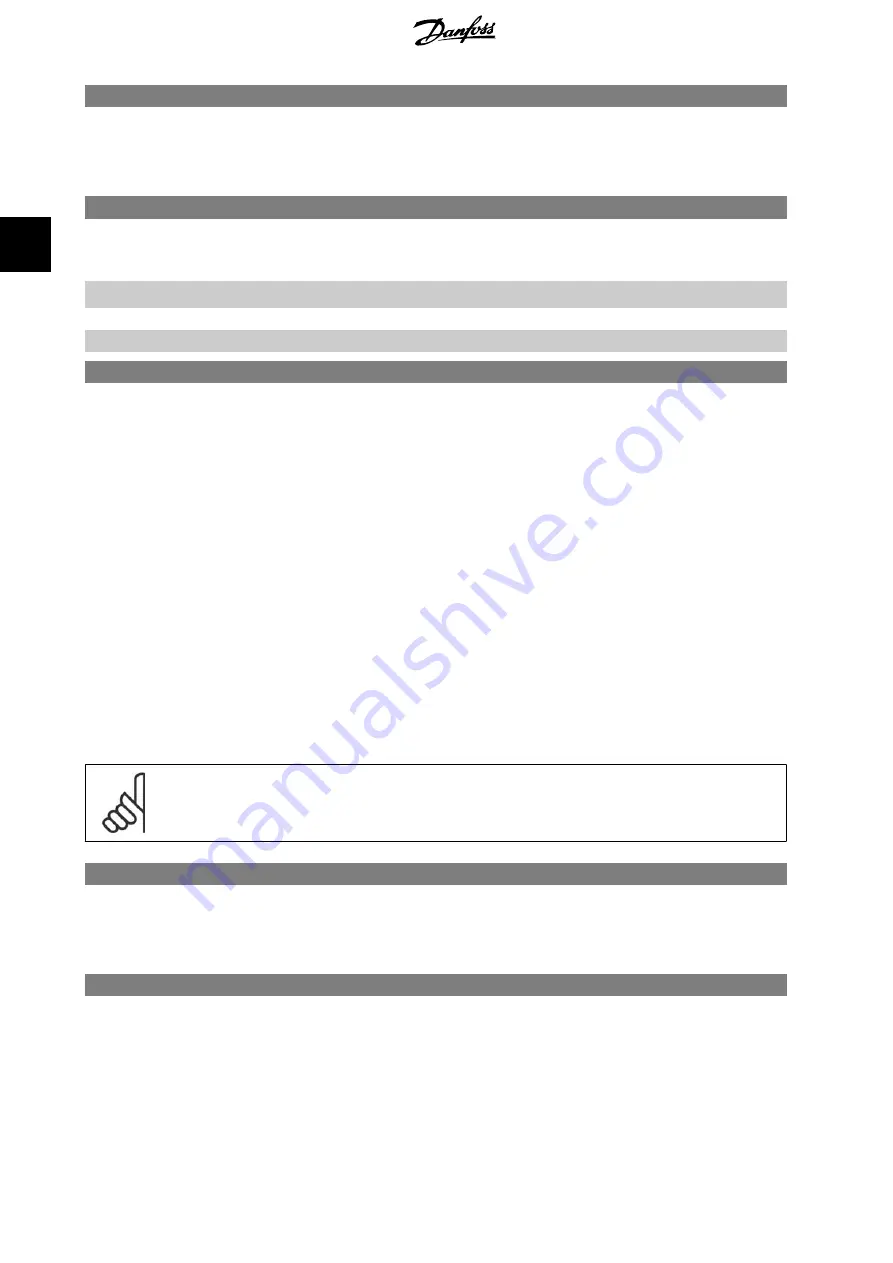
22-24 No-Flow Delay
Range:
Function:
10 sec.
*
[0-600 sec.]
Set the time Low Power/Low Speed must stay detected to activate signal for actions. If detection disappears
before run out of the timer, the timer will be reset.
22-26 Dry Pump Function
Option:
Function:
Low Power Detection
must be Enabled (par. 22-21) and commissioned (using either par. 22-3*,
No Flow Power
Tuning
, or par. 22-20
Auto Set-Up
) in order to use Dry Pump Detection.
[0]
*
Off
[1]
Warning
Messages in the Local Control Panel display (if mounted) and/or signal via a relay or a digital output.
[2]
Alarm
The frequency converter trips and motor stays stopped until reset.
22-27 Dry Pump Delay
Range:
Function:
60 sec.
*
[0-600 sec.]
Defines for how long the Dry Pump condition must be active before activating Warning or Alarm
3.20.2. 22-3* No-Flow Power Tuning
Tuning Sequence, if not choosing
Auto Set Up
in par. 22-20:
1.
Close the main valve to stop flow
2.
Run with motor until the system has reached normal operating temperature
3.
Press Hand On button on the Local Control Panel and adjust speed for approx. 85% of rated speed. Note the exact speed
4.
Read power consumption either by looking for actual power in the data line in the Local Control Panel or call par. 16-10 or 16-11,
Power
, in Main
Menu. Note the power read out
5.
Change speed to approx. 50% of rated speed. Note the exact speed
6.
Read power consumption either by looking for actual power in the data line in the Local Control Panel or call par. 16-10 or 16-11,
Power
, in Main
Menu. Note the power read
7.
Program the speeds used in par. 22-32/22-33 and par. 22-36/37
8.
Program the associated power values in par. 22-34/35 and par. 22-38/22-39
9.
Switch back by means of
Auto On
or
Off
NB!
Set par. 1-03,
Torque Characteristics
, before tuning takes place.
22-30 No-Flow Power
Range:
Function:
[Depends on the power size detec-
tion of No-Flow]
Read out of calculated No Flow power at actual speed. If power drops to the display value the frequency converter
will consider the condition as a No Flow situation.
22-31 Power Correction Factor
Range:
Function:
100% [1-400%]
Make corrections to the calculated power at No Flow Detection (see par. 22-30).
If No Flow is detected, when it should not be detected, the setting should be increased to above 100%. However,
if No Flow is not detected, when it should be detected, the setting should be decreased below 100%".
3. Parameter Description
VLT
®
HVAC Drive Programming Guide
176
MG.11.C5.02 - VLT
®
is a registered Danfoss trademark
3