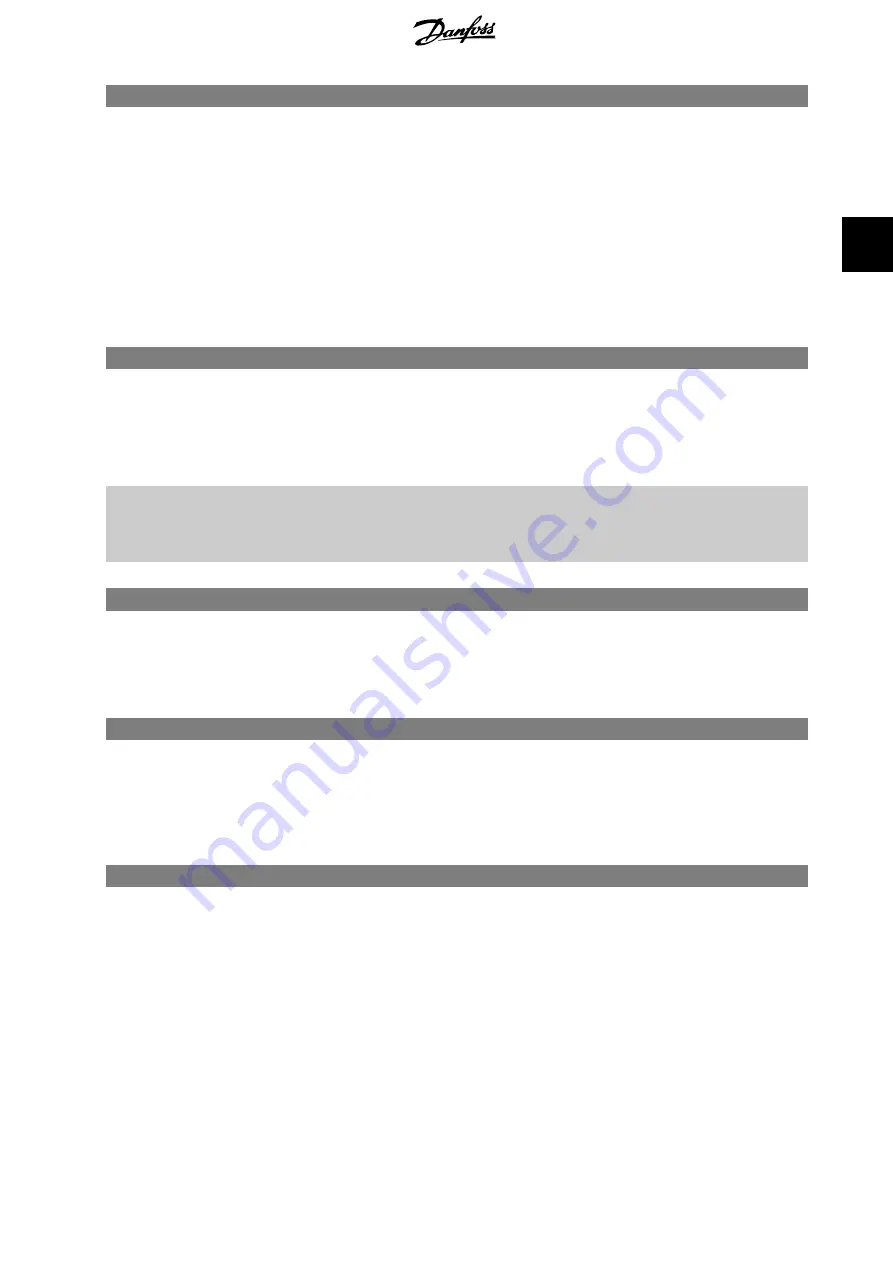
20-84 On Reference Bandwidth
Range:
Function:
5%
*
[0 - 200%]
When the difference between the feedback and the setpoint reference is less than the value of this parameter,
the frequency converter’s display will show “Run on Reference”. This status can be communicated externally by
programming the function of a digital output for
Run on Reference/No Warning
[8]. In addition, for serial com-
munications, the On Reference status bit of the frequency converter’s Status Word will be high (1).
The
On Reference Bandwidth
is calculated as a percentage of the setpoint reference.
3.18.7. 20-9* PID Controller
This group provides the ability to manually adjust this PID Controller. By adjusting the PID Controller parameters the control performance may be
improved. See section
PID
in the
VLT HVAC Drive Design Guide, MG.11.Bx.yy
for guidelines on adjusting the PID Controller parameters.
20-91 PID Anti Windup
Option:
Function:
[0]
Off
Off
[0] causes the PID Controller to continue to integrate (add) the error between the feedback and setpoint
reference even though the frequency converter cannot adjust its output frequency to correct this error. In this
case, the integral term of the PID Controller may become quite large. When the PID Controller can again control
the frequency converter’s output frequency, it may attempt to initially make a large change in the frequency
converter’s output frequency. This should generally be avoided.
[1]
*
On
On
[1] stops the PID Controller from integrating (adding) the error between the feedback and the setpoint
reference if it is not possible to adjust the output frequency of the frequency converter to correct the error. This
can occur when the frequency converter has reached its minimum or maximum output frequency or when the
frequency converter is stopped.
20-93 PID Proportional Gain
Range:
Function:
0.50
*
[0.00 = Off - 10.00]
This parameter adjusts the output of the frequency converter’s PID Controller based on the error between the
feedback and the setpoint reference. Quick PID Controller response is obtained when this value is large. However,
if too large a value is used, the frequency converter’s output frequency may become unstable.
20-94 PID Integral Time
Range:
Function:
20.00 s
*
[0.01 - 10000.00 = Off s] The integrator adds over time (integrates) the error between the feedback and the setpoint reference. This is
required to ensure that the error approaches zero. Quick frequency converter speed adjustment is obtained when
this value is small. However, if too small of a value is used, the frequency converter’s output frequency may
become unstable.
20-95 PID Differentiation Time
Range:
Function:
0.0 s
*
[0.00 = Off - 10.00 s]
The differentiator monitors the rate of change of the feedback. If the feedback is changing quickly, it will adjust
the output of the PID Controller to reduce the rate of change of the feedback. Quick PID Controller response is
obtained when this value is large. However, if too large of a value is used, the frequency converter’s output
frequency may become unstable.
Differentiation time is useful is situations where extremely fast frequency converter response and precise speed
control are required. It can be difficult to adjust this for proper system control. Differentiation time is not com-
monly used in VLT HVAC Drive applications. Therefore, it is generally best to leave this parameter at 0 or OFF.
VLT
®
HVAC Drive Programming Guide
3. Parameter Description
MG.11.C5.02 - VLT
®
is a registered Danfoss trademark
163
3