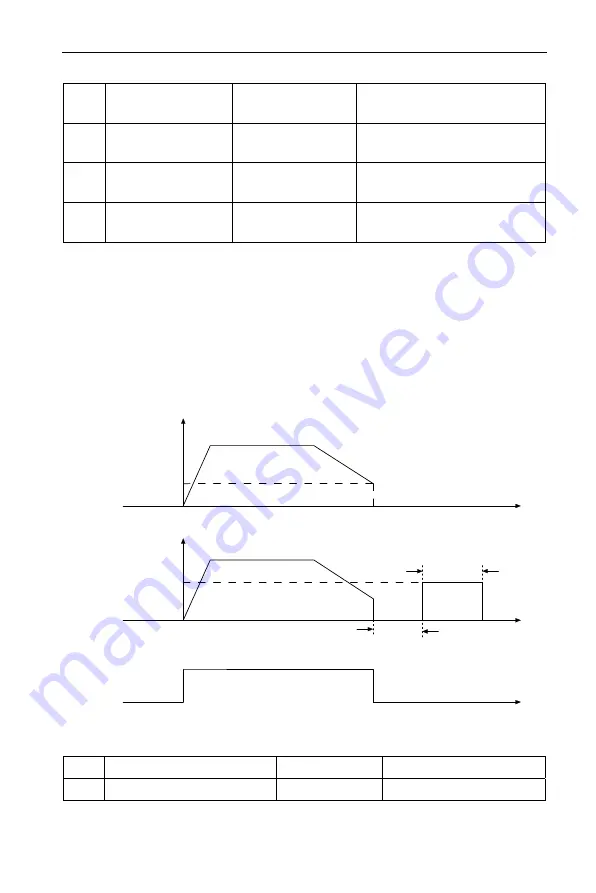
Chapter 6 Key Functional Parameter Explanation In Detail 200 Series General Purpose Vector AC Drive
58
Chapter 6 Key Function Parameter Explanation In Detail
F1-06
Deceleration stop
braking start frequency
Factory default: 0.00Hz Setting Range: 0.00 Hz
~
F0-05
F1-07
Deceleration stop brake
waiting time
Factory default: 0.000s
Setting Range: 0.000s
~
32.000s
F1-08
Deceleration stop DC
braking current
Factory default: 0%
Setting Range: 0
~
150%
F1-09
Deceleration stop DC
braking time
Factory default: 0.000s
Setting Range: 0.0s
~
32.000s(no DC
braking if it is 0.0s)
Stop braking start frequency: In the process of deceleration and stop, when output frequency reaches this
frequency, it begins to enter into stop braking waiting;
Stop braking waiting time: During the period of stop braking waiting, the AC Drive would block the
output, DC braking will be conducted after the delay. It is used to prevent the over current fault caused by
DC braking when the speed is higher.
Stop DC braking current: It refers to the added DC braking value. The bigger the value, the bigger the
braking torque.
Stop DC braking time: The duration time of DC braking.
Stop braking
start frequengcy
Output frequency
Output voltage
Stop DC braking
Running command
Stop braking waiting time
Stop DC braking time
Stop command
t
t
t
Figure 6-1 Schematic diagram of DC braking at deceleration to stop
F2-01 Torque boost
Model depends
Setting range: 0.1%
~
50.0%
F2-02 Cut-off frequency of torque boost Default: 20.00Hz
Setting range: 0.00Hz
~
F0-17
In order to compensate the low-frequency torque characteristics of V/F control, some boost compensation
is made for the output voltage at low frequency. However, if the torque boost is set too large, the motor