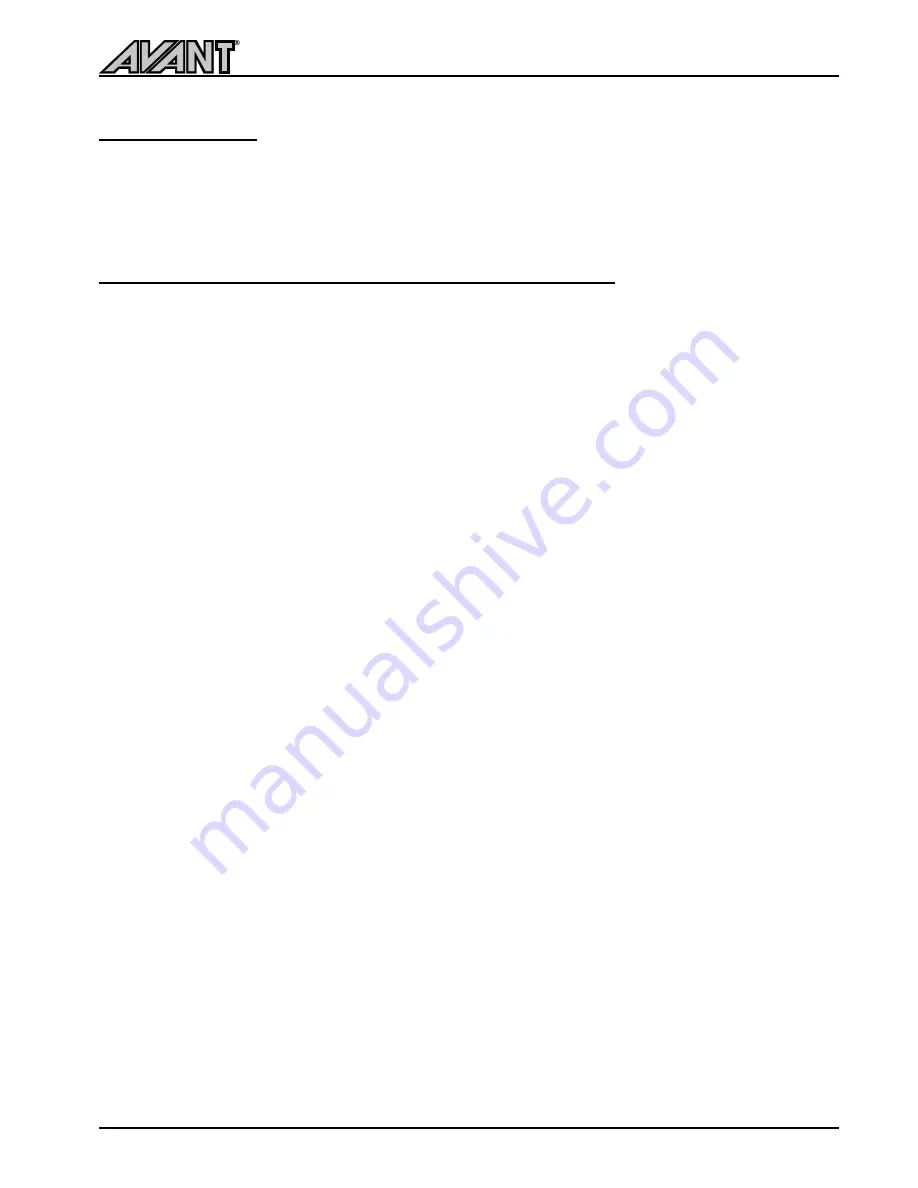
9
Robot 185
Safety Instructions
After operation
After you have finished working, always lower the work tool to the floor or ground.
Turn off the power on the machine.
Always keep the remote control in a safe place, to prevent others from using the machine.
To be noted in service and maintenance operations
Most accidents happen when the machine is being maintained and serviced because personnel are close to
the machine. By taking this into account, a large number of injuries can be avoided.
Protective glasses must be worn during service and maintenance operations.
Never perform maintenance operations without proper training. The machine must be serviced where it
cannot be of danger to the user or others.
Let other people clearly know when the machine is being serviced.
If faults or damages occur in the machine, service the machine immediately and do not use it when it is
damaged.
If the service operation does not require starting up the machine, unplug the connection cable and make
sure it cannot be plugged in again by mistake.
The condition of the machine must be checked regularly and the machine must be monitored every day.
This way, the machine will remain in a condition that is safe for both the user and others.
The electrical cabinet must not be opened, if power is connected to the machine.
Always remove the hydraulic connectors carefully. They may be still pressurised even though the engine is
turned off.
Before removing a hose or a connector, always check that the hydraulic hose is not pressurised.
Never attempt to stop hydraulic leakage with your hands.
Always secure mechanical parts before removing hydraulic hoses.
Always turn off the power from the machine before removing or opening a component that is conductive.
Only competent personnel are allowed to work in the heavy current power.
Содержание Robot 185
Страница 11: ...11 Robot 185 Structure 795 1820 2030 1590 107 2290 2090 0 1 2 3 4 5 1 2 2 3 1 0 1 2 3 4 5 6 ...
Страница 19: ...19 Robot 185 Structure Control system 1 Control box 2 Switch panel 3 Control lever ...
Страница 66: ...66 Robot 185 Electric diagrams 400 V system and soft start ...
Страница 67: ...67 Robot 185 Electric diagrams Frame module and CAN bus ...
Страница 68: ...68 Robot 185 Electric diagrams Frame valves and sensors ...
Страница 69: ...69 Robot 185 Electric diagrams Tower module and rotating connector ...
Страница 70: ...70 Robot 185 Electric diagrams Tower module and valves ...
Страница 71: ...71 Robot 185 Electric diagrams Emergency stop circuit and remote control ...