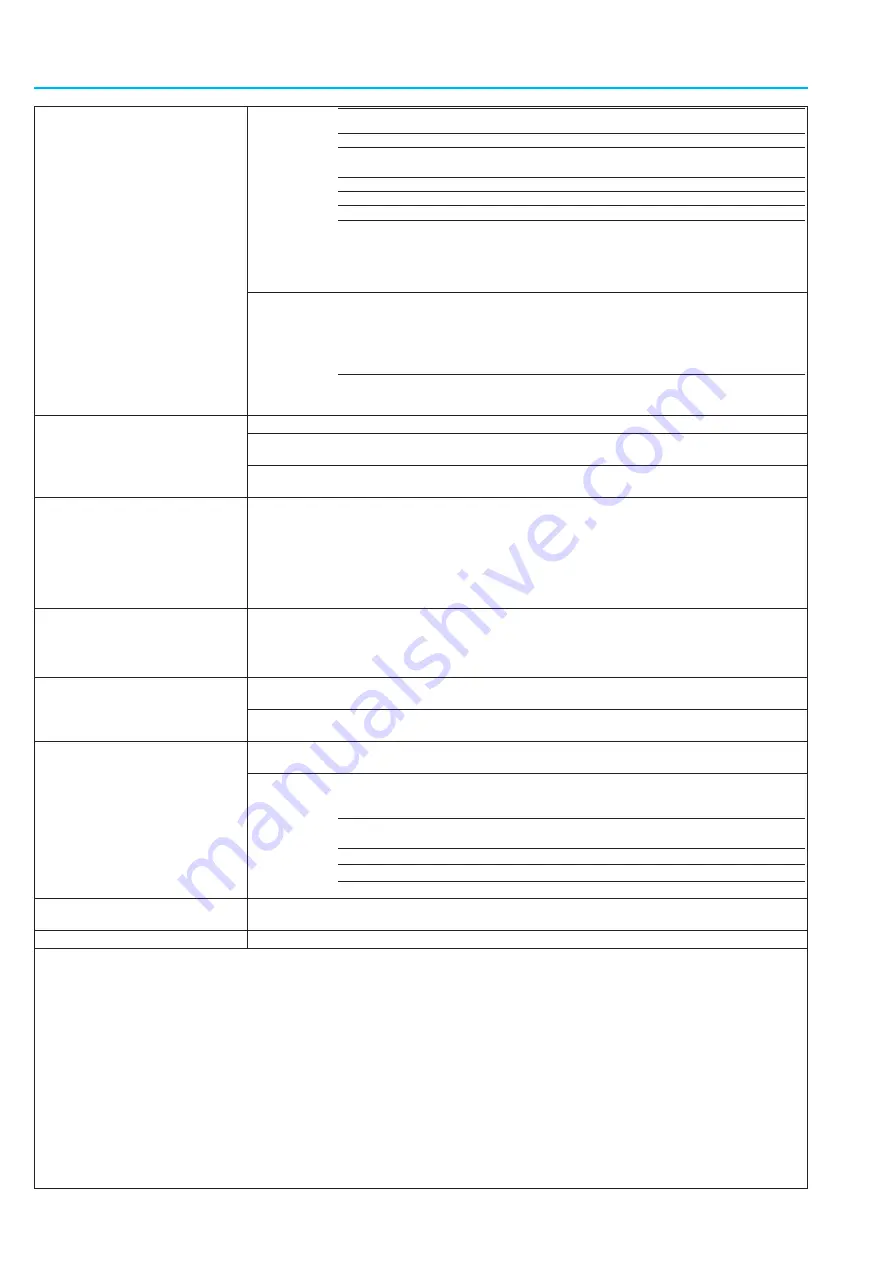
Functions
Standard:
Switch-off mode adjustable
limit or torque seating for end position OPEN and end position CLOSED
Torque monitoring over the whole travel
Torque by-pass, adjustable up to 5 seconds
(no torque monitoring during running time)
Phase loss monitoring
5)
with automatic phase correction
Programmable behaviour in case of bus failure
Running indication via indication lights
Positioner:
Actual position value via Profibus DP interface
Programmable behaviour on loss of signal
Automatic adaptation of the dead band (adaptive behaviour selectable)
Change-over between OPEN - CLOSE duty and modulating duty
via Profibus DP
Options:
Process controller, PID
Process setpoint via Profibus DP interface
Actual process value via 0/4 – 20 mA additional input
Programmable behaviour on loss of signal
Limitation of control range
Change-over between OPEN - CLOSE duty and modulating duty
via Profibus DP
Multiport valve function:
Direct approaching of up to 8 intermediate positions via Profibus DP
and the local controls
Monitoring functions
Programmable monitoring of the max. number of starts, generates warning signal
Reaction monitoring for operation command (programmable from 1 to 15 seconds),
generates fault signal and results in switching off
Operating time monitoring (programmable from 4 to 1,800 seconds), generates warning
signal
Electronic name plate
Order data:
AUMATIC commission number, actuator commission number,
KKS number (definition system for power plants), valve number,
plant number
Product data: Product name, actuator works number, AUMATIC works number,
logic software version, logic hardware version, date of final test,
wiring diagram, terminal plan
Project data: Project name, 2 freely definable customer fields with a max. of 19 digits each
Service data: Service telephone, Internet address, service text 1, service text 2
Logging of operating data
A resettable counter and a lifetime counter for:
Motor running time, number of starts, torque switch trippings in end position CLOSED, limit
switch trippings in end position CLOSED, torque switch trippings in end position OPEN, limit
switch trippings in end position OPEN, torque faults CLOSE, torque faults OPEN, motor
protection trippings
Motor protection evaluation
Standard:
Monitoring of the motor temperature with PTC tripping device
in combination with PTC thermistors in the actuator motor
Option:
Thermal overload relay in combination with thermoswitches in
the actuator motor
Electrical connection
Standard:
Plug/socket connector with screw type connection (KP, KPH)
Protection type: increased safety EEx de
Options:
Plug/socket connector with spring cage terminals (KES)
Protection type: increased safety EEx de
Threads for cable entries
Plug/socket connector with spring cage terminals (KES)
Protection type: flameproof enclosure EEx d
Special threads, other than standard mentioned above, possible
Parking frame for wall mounting of the disconnected plug
Protection cover for plug compartment (when plus is removed)
Overvoltage protection (option)
Protection of the actuator and control electronics against overvoltages on the fieldbus
cables of up to 4 kV
6)
Wiring diagram (basic version)
ACP E3FC-2M0—S000 KMS TP202/001
5) During an adjustable period (factory setting 10 seconds), faults in the supply voltage (e.g. voltage drops) will not lead to an fault signal.
6) Only in combination with standard electrical connection via plug/socket connector with screw-type terminals (KP, KPH).
78
Multi-turn actuator SAExC 07.1 – SAExC 16.1/SARExC 07.1 – SARExC 16.1 Non-Intrusive
with actuator controls AUMATIC ACExC 01.1 Profibus DP
Operation instructions