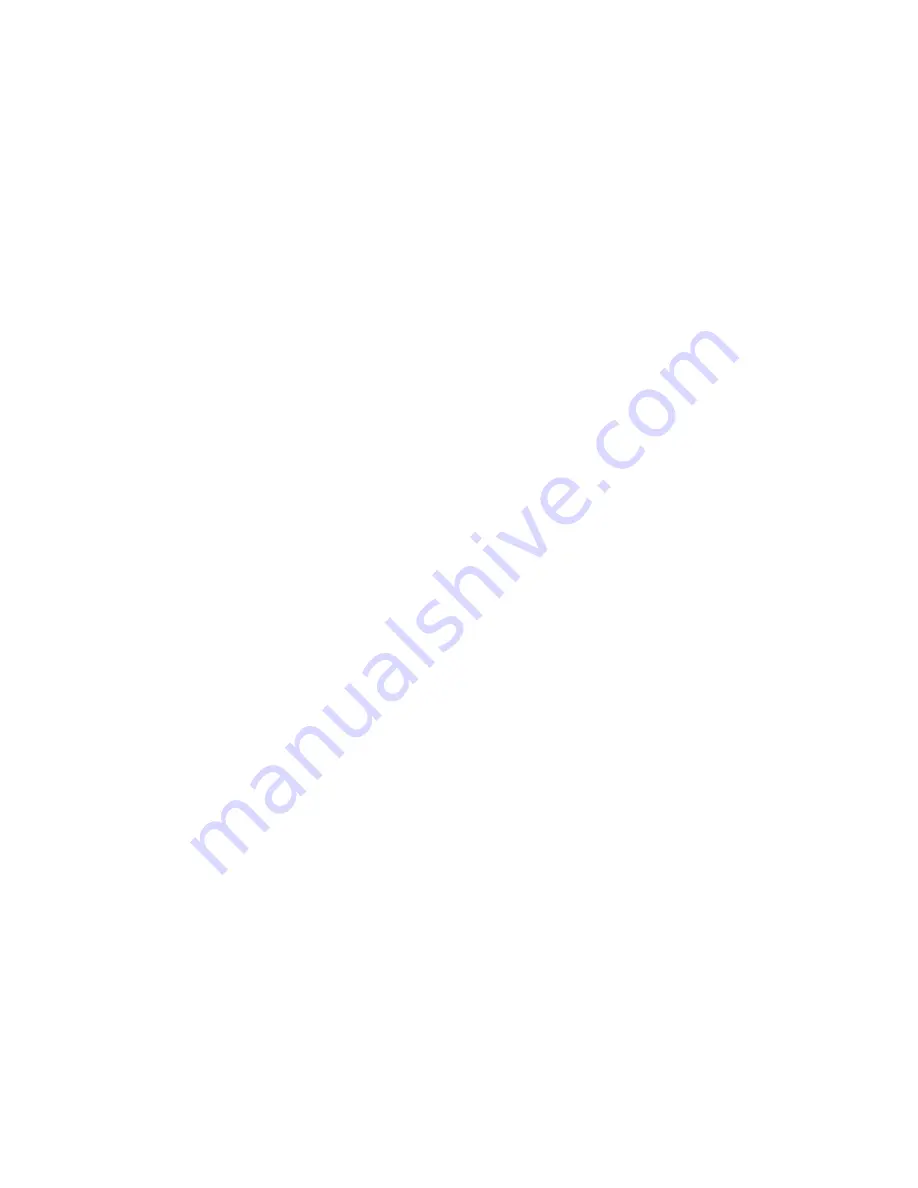
Controller / User Interface | 4-13
Primary Calibration
The actual furnace temperature set point will vary from unit-to-unit
based upon the Primary Calibration which correlates the actual cell
response for the desired 695°C cell set point temperature with the actual
furnace thermocouple feed back temperature. This is accomplished by
applying two known concentrations of oxygen to the analyzer during
the primary calibration. The software algorithm then calculates the
actual cell temperature from the cell mV response and then makes the
appropriate increase or decrease in the furnace temperature control set
point. If you take the displayed cell temperature and divide it by the T/C
Ratio in memory location 88, then this is the actual furnace set point
control temperature. If you take a Type-K table, you should be able to
measure the voltage on terminals C and D on the sensor board, and then
add the appropriate amount of mVs for the board ambient, your corre-
sponding temperature from a Type-K thermocouple should be the actual
furnace set point temperature = 695°C / T/C Ratio (memory location 88).
Use the Type-K table to determine the mV change you have for 273°C
and adding this mV change for the actual board temperature, should be
the compensation voltage measured between D+ and 6- on the sensor
board. So for a 50°C ambient at the board, the voltage should be 11.05
mV (273°C) + 2.02 mV (50°C) = 13.07 mVs.
If you have a T/C ratio of 0.9, the corresponding furnace temperature set
point should be (695°C / 0.9 = 772°C). If you measure the voltage at
terminals C and D on the sensor board with a 50°C ambient, the voltage
should be 32.125 (772°C) - 2.02 mV (50°C) = 30.1 mV. If you add in the
compensation voltage for 50°C, the voltage at terminals 5 and 6 should be
30.1 mV + 12.05 mV = 42.15 mVs which should also be the voltage that
you measures at T/C+ and T/C - terminals on the Series 2000 wiring card
terminals and also the displayed T/C mV value that you can set one of
the display lines to view in the Setup key - Display menu.
Based upon the age of your cell and its characteristics, the control tem-
peratures should be slightly different. However if you incorrectly
perform a primary calibration or if the cell really starts to deteriorate, the
actual cell response to calibration gas will drop off. The primary calibra-
tion is a why to extend the life of the cell since the furnace control
temperature can be increased as the cell ages to reduce the atrophy and
extend the cell life if the output starts to drop off at its original factory
cal furnace set point temperature. You can tell this with the distribution
that you have in your spreadsheet since the calculated cell temperatures
for some of the analyzers are well below 695°C or above by a fair amount.
If the cell response goes out of the following limits, you will receive a
zero or span gas range error. At this point, you should perform a pri-
Содержание Thermox 2000 ATEX Series
Страница 18: ...1 8 Thermox Series 2000 WDG HPII HPIIC ATEX This page intentionally left blank...
Страница 24: ...2 6 Thermox Series 2000 WDG HPII HPIIC ATEX This page intentionally left blank...
Страница 68: ...3 44 Thermox Series 2000 WDG HPII HPIIC ATEX This page intentionally left blank...
Страница 128: ...5 28 Thermox Series 2000 WDG HPII HPIIC ATEX This page intentionally left blank...
Страница 149: ...Service and Parts 7 3 Figure 7 1 Wiring diagram for standard sensor...
Страница 151: ...Service and Parts 7 5 Figure 7 2 Cell replacement...
Страница 153: ...Service and Parts 7 7 Figure 7 3 Furnace thermocouple replacement...
Страница 157: ...Service and Parts 7 11 Figure 7 5 Furnace replacement...
Страница 159: ...Service and Parts 7 13 Figure 7 6 Combustibles detector replacement Hot Wire...
Страница 196: ...B 4 Thermox Series 2000 WDG HPII HPIIC ATEX This page intentionally left blank...
Страница 202: ...D 2 Thermox Series 2000 WDG HPII HPIIC ATEX This page intentionally left blank...