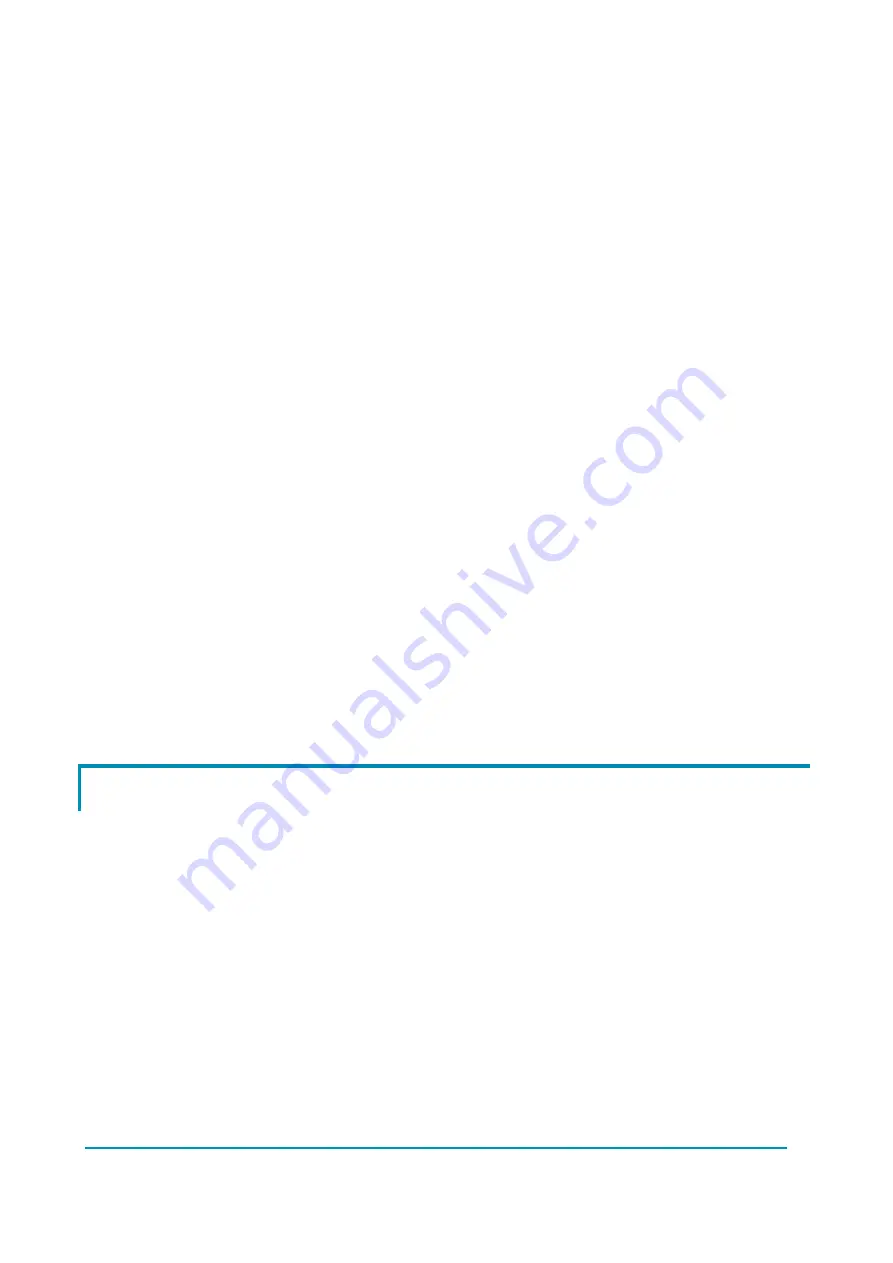
AEMZP0BA - EPS-AC0 - User Manual
Page - 95/95
16 PERIODIC MAINTENANCE TO BE
REPEATED AT TIMES INDICATED
Check the wear and condition of the Contactors’ moving and fixed contacts.
Electrical Contacts should be checked every
3 months.
Check the Battery cables, cables to the controller, and cables to the motor. Ensure
the insulation is sound and the connections are tight.
Cables should be checked every
3 months.
Check the mechanical operation of the Contactor(s). Moving contacts should be free
to move without restriction.
Check every
3 months.
Checks should be carried out by qualified personnel and any replacement parts
used should be original. Beware of NON ORIGINAL PARTS.
The installation of this electronic controller should be made according to the
diagrams included in this Manual. Any variations or special requirements should be
made after consulting a Zapi Agent. The supplier is not responsible for any problem
that arises from wiring methods that differ from information included in this Manual.
During periodic checks, if a technician finds any situation that could cause damage
or compromise safety, the matter should be bought to the attention of a Zapi Agent
immediately. The Agent will then take the decision regarding operational safety of
the machine.
Remember that Battery Powered Machines feel no pain.
NEVER USE A VEHICLE WITH A FAULTY ELECTRONIC CONTROLLER.
16.1 Testing the faulty detection circuitry
The material handling directive EN1175 requires periodic testing of the controller’s
fault detection circuitry to be checked in one of the following modes (choose the one
you prefer):
1) Switch on the key and try to disconnect the stepper motor or the twin pot. An
alarm, stopping the traction should immediately occur.
2) Try to disconnect the steering motor. After switching on the key an alarm
stopping the traction should immediately occur as soon as the steering (or
handle) wheel rotates.
Summary of Contents for EPS-AC0
Page 23: ...AEMZP0BA EPS AC0 User Manual Page 23 95 6 2 EPS AC0 Stepper Motor diagram Figure 6 2...
Page 24: ...Page 24 95 AEMZP0BA EPS AC0 User Manual 6 3 EPS AC0 Twin pot diagram Figure 6 3...
Page 55: ...AEMZP0BA EPS AC0 User Manual Page 55 95 12 3 2 RTC with Encoder and Feedback pot Figure 12 3...