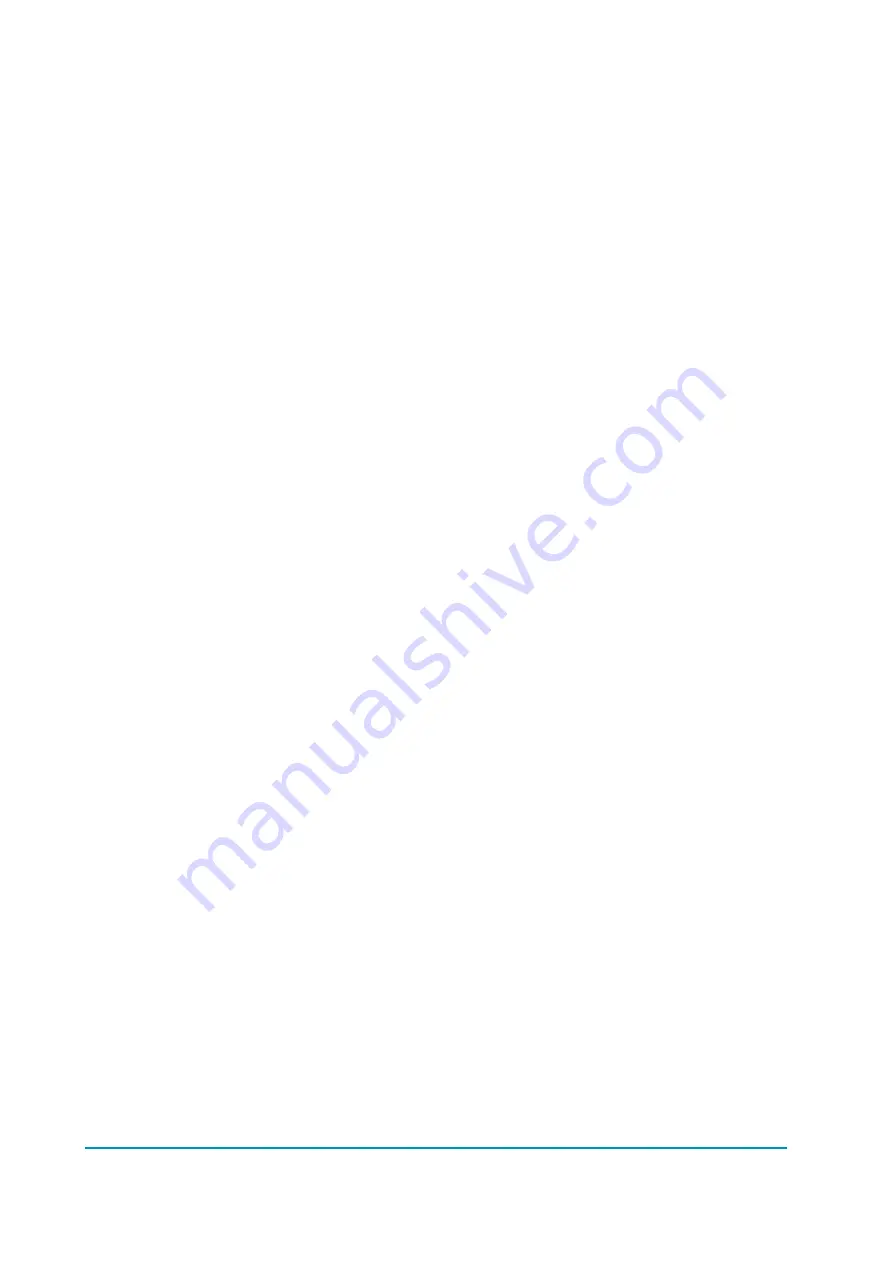
Page - 6/95
AEMZP0BA - EPS-AC0 - User Manual
1 INTRODUCTION
This equipment (Eps-ac0: AC0 Electrical Power Steering) may perform two steer by
wire functions on a truck:
1) manually controlled power steering
2) automatic centering (AUTC).
Manually controlled steering may use either a stepper motor (used as a
tachogenerator) or a twin pot fixed to the steering wheel.
Feedback sensors are mandatory to close the loop when an automatic function is
required (Automatic Centering).
Feedback sensors are mandatory to close the loop in manual mode if a twin pot is
mounted on the steering wheel.
Feedback sensors are strongly suggested (to improve safety) in manual mode if a
stepper motor is mounted on the steering wheel (open loop).
The feedback sensor may be an incremental encoder on the steering motor shaft in
combination with one straight-ahead switch. A second switch may be adopted,
together with the first one, in the 90 degrees position to improve safety. Besides a
feedback potentiometer may be chosen in alternative to the straight-ahead switch.
The eps-ac0 runs an inexpensive, robust and maintenance free three phases
AC induction motor.
Also, our patented system makes possible
to use a very low-
resolution encoder (4 pulses/rev are more than enough)
mounted on the
steering motor shaft.
The on board CAN interface
makes the communication exchange between our
eps-ac0 and other units in the truck rapid and simple. Via CAN it is possible to
enhance the steering performances with additional functions like: steer sensitivity
changes with the traction speed, traction speed modulation vs. the steered angle,
via CAN automatic centering request and so on.
Configuration options, steering adjustment, measurement functions, and
troubleshooting operations are integrally supported by the ZAPI hand held
controller
equipped with Eprom release number CKULTRA ZP3.01 or subsequent.
Having two microprocessors provides improved safety and operation. The first
microprocessor performs operations and a second one executes supervisor
functions.
Both the aboard microprocessors are CAN BUS connected, as
consequence the eps-ac0 may receive a remote steering command directly via
CAN fulfilling the norm (the redundant check of the steering command
complies with the Category #3 requirement).
The microprocessors combined with the ZAPI hand held controller make servicing
easy and direct, reducing adjustment and troubleshooting time. Increased steering
motor performance and reduced noise levels are achieved by using MOSFET
technology.
The reference SW release for this manual is ZP0.70.
Summary of Contents for EPS-AC0
Page 23: ...AEMZP0BA EPS AC0 User Manual Page 23 95 6 2 EPS AC0 Stepper Motor diagram Figure 6 2...
Page 24: ...Page 24 95 AEMZP0BA EPS AC0 User Manual 6 3 EPS AC0 Twin pot diagram Figure 6 3...
Page 55: ...AEMZP0BA EPS AC0 User Manual Page 55 95 12 3 2 RTC with Encoder and Feedback pot Figure 12 3...