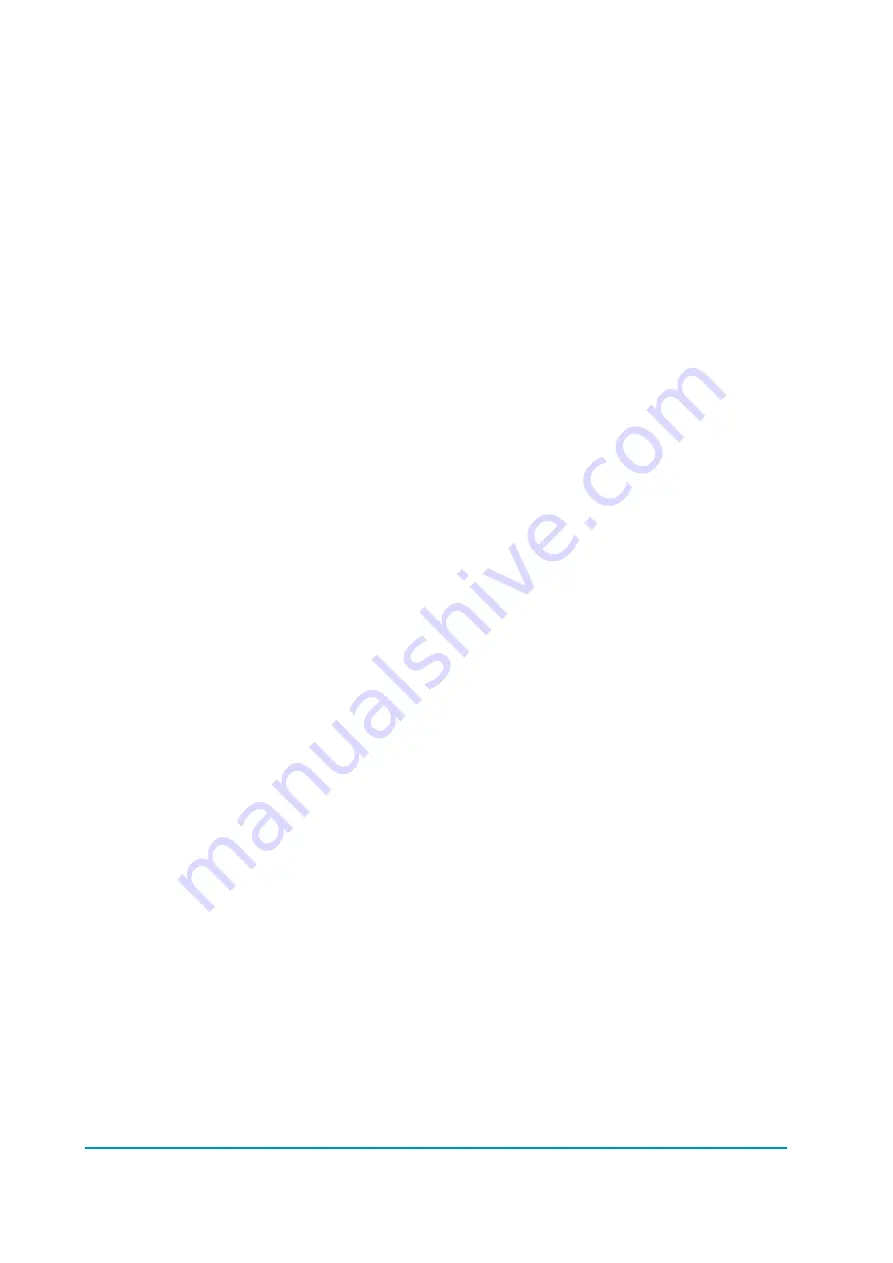
AEMZP0BA - EPS-AC0 - User Manual
Page - 91/95
3) CURRENT GAIN
CAN Bus Code = 225
- Cause:
This alarm occurs when the parameters to compensate for the
gain of the current amplifiers (ADJUSTMENT #03 and
ADJUSTMENT #04) have the default values (i.e. the maximum
current was not regulated).
- Remedy:
It is necessary to send the controller to Zapi to perform the
maximum current regulation.
14.1.5 Five Blinks Alarms
1) HIGH
TEMPERATURE
CAN Bus Code = 61
- Cause:
This alarm occurs if the temperature of the controller base plate
overtakes 75 degrees.
- Remedy:
Improve the cooling of the controller; otherwise it is necessary to
replace the controller.
2) MOTOR TEMPERAT.
CAN Bus Code = 65
- Cause:
This alarm occurs only when DIAG MOTOR TEMP is on and the
thermal sensor inside the motor measures a temperature higher
than 150 degrees. It occurs also when trying to acquire the motor
resistance with a temperature in the motor higher than 150 degree
(still with DIAG MOTOR TEMP to ON).
- Remedy:
Check the thermal sensor in the motor is right working. If it is,
improve the cooling of the motor.
14.1.6 Six Blinks Alarms
1) STBY I HIGH
CAN Bus Code = 53
- Cause:
This alarm occurs two ways:
1) In the initial rest state after key on, if the outputs of the current
amplifiers are not comprised in the window 2.2 to 2.8 Vdc.
2) After the initial diagnosis this alarm occurs when the outputs of
the current amplifiers at rest have a drift larger than ±0.15 V.
- Remedy:
It is necessary to replace the controller.
2) VMN NOT OK
CAN Bus Code = 32
- Cause:
This alarm occurs in the initial rest state after key on if the outputs
of the motor voltage amplifiers are not in the window from 2.2 to
2.8 Vdc.
- Remedy:
It is necessary to replace the controller.
3) LOGIC FAILURE #3
CAN Bus Code = 17
- Cause:
This alarm occurs in the rest state if the output of the voltage
amplifier of the phase Vu-Vw have a drift larger than ±0.25 V.
- Remedy:
It is necessary to replace the controller.
4) LOGIC FAILURE #4
CAN Bus Code = 16
Summary of Contents for EPS-AC0
Page 23: ...AEMZP0BA EPS AC0 User Manual Page 23 95 6 2 EPS AC0 Stepper Motor diagram Figure 6 2...
Page 24: ...Page 24 95 AEMZP0BA EPS AC0 User Manual 6 3 EPS AC0 Twin pot diagram Figure 6 3...
Page 55: ...AEMZP0BA EPS AC0 User Manual Page 55 95 12 3 2 RTC with Encoder and Feedback pot Figure 12 3...