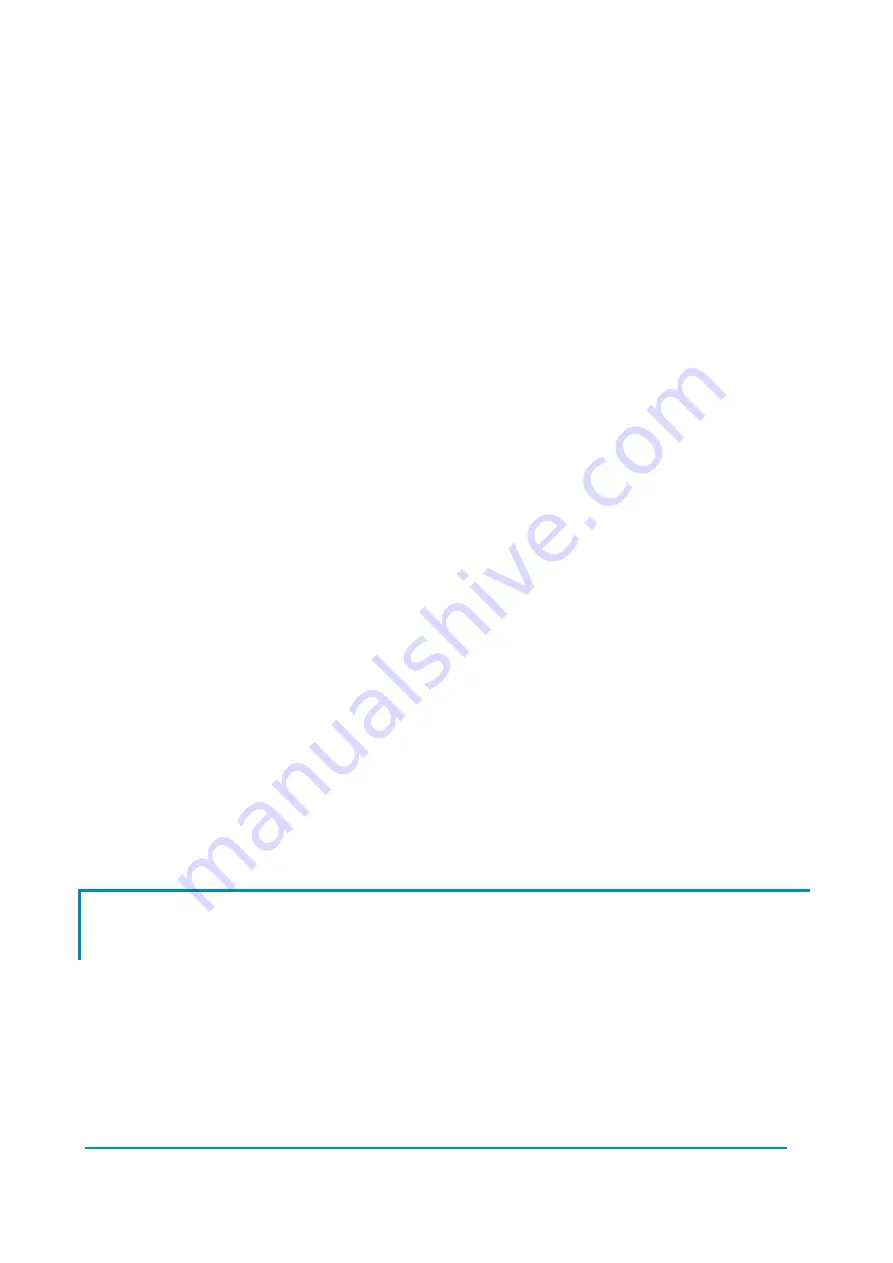
Page - 46/95
AEMZP0BA - EPS-AC0 - User Manual
Step5
Connect the feedback pot in such a way the FEEDBACK POT reading in the
tester menu assumes higher voltage when the FREQUENCY in the tester
menu is positive. When a FB POT LOCKED alarm occurs immediately after
switching on the key, it means the motor is turning away from the wished
position (i.e. FEEDBACK POT decreases when the FREQUENCY is
positive). Then it is necessary to swap the PPOT with NPOT (CNB#2 with
CNB#1).
Step6
Connect the encoder. The encoder supply is between CNB#4 (5 Vdc) and
CNA#11 (GND): the two channels are CNB#8 (CHA) and CNB#7 (CHB).
Step7
Verify the reading ENC SPEED in the tester menu is consistent with the
reading FREQUENCY in the tester menu. Consistent means that ENC
SPEED and FREQUENCY must have the same sign and a close value. If
ENC SPEED has a wrong sign, swap CHA (CNB#8) with CHB (CNB#7). If
ENC SPEED is not close to FREQUENCY, the encoder resolution is wrong
and a different SW is needed (see 12.4.7.12 and 12.4.7.8).
Step8
If the motor runs well without glitches, it is possible to stays with ENCODER
CONTROL to OFF; otherwise, turn ENCODER CONTROL to ON.
Step9
Verify the steered wheel rotates in the correct direction according to the
hand wheel. If it isn’t, swap DL (CNA#9) with QL (CNA#8).
Step10
Set the LIMIT DEVICE option to OFF to avoid the maximum angle
limitations.
Step11
Turn the steering wheel until the maximum (plus 90 degrees) steered wheel
angle is achieved. This position (plus 90 degrees) corresponds to the
maximum value of the FEEDBACK POT reading in the TESTER menu.
Step12
With the steered wheel in the maximum angle (plus 90 degrees), enter and
save the adjustment SET MAX FB POT on the hand set to memorize the
steer angle feedback pot voltage for the maximum (plus 90 degrees) limit
position. If present, the maximum of the FB ENC is recorded too (although it
is not shown in the hand set).
Step13
Turn the steering wheel until the minimum (minus 90 degrees) steered
wheel angle is achieved. This position (minus 90 degrees) corresponds to
the minimum value of the FEEDBACK POT reading in the TESTER menu.
Step14
With the steered wheel in the minimum angle (minus 90 degrees), enter and
save the adjustment SET MIN FB POT on the hand set to memorize the
steer angle feedback pot voltage for the minimum (minus 90 degrees) limit
position. If present, the minimum of the FB ENC is recorded too (although it
is not shown in the hand set).
Step15
Set FEEDBACK DEVICE to OPTION#2 (feedback pot plus feedback
encoder) and recycle the key to enable the steering by encoder.
Step16
Carry out the complete set-up procedure (see 11.1).
10.4 Stepper Motor with Encoder and Toggle Switch(es): one shot
installation procedure
This procedure is relative to the connecting drawings Figure 6-2. It describes the
step by step installation procedure to get the prototype working in manual mode: to
raise the AUTC function it is necessary to make the complete set-up procedure (see
topic 11).
For every truck released on the field, the default set-up and wiring shall reply the
prototype settings and so no installation procedure is required except for the
acquisition of the limiting position (see the quick set-up 11.2).
Carry out the procedure in the following order.
Summary of Contents for EPS-AC0
Page 23: ...AEMZP0BA EPS AC0 User Manual Page 23 95 6 2 EPS AC0 Stepper Motor diagram Figure 6 2...
Page 24: ...Page 24 95 AEMZP0BA EPS AC0 User Manual 6 3 EPS AC0 Twin pot diagram Figure 6 3...
Page 55: ...AEMZP0BA EPS AC0 User Manual Page 55 95 12 3 2 RTC with Encoder and Feedback pot Figure 12 3...