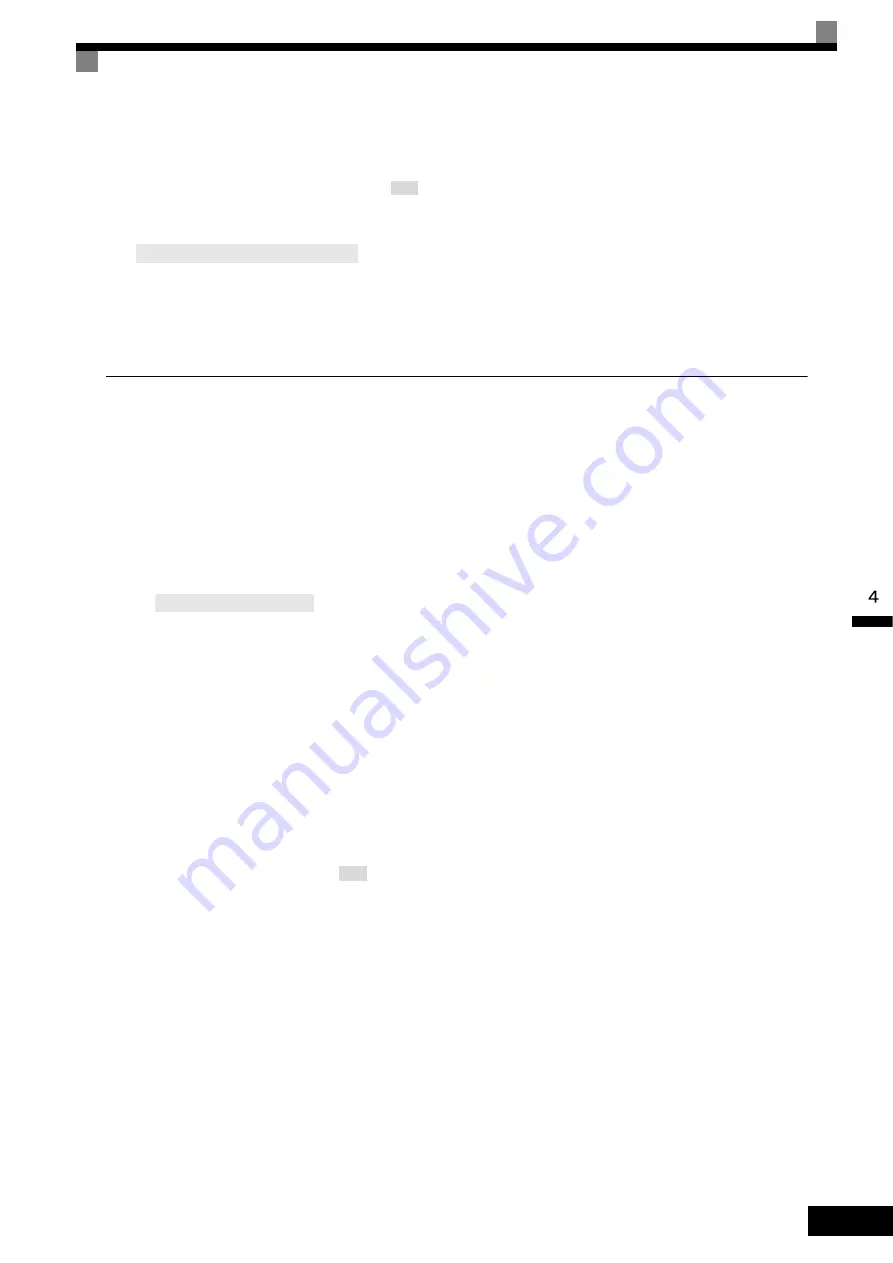
Trial Operation Procedures
4-
9
Open-loop Vector Control (A1-02 = 2)
Perform autotuning. If the motor can be operated, perform rotational autotuning. If the motor cannot be oper-
ated, perform stationary autotuning 1
. Refer to the following section on
Autotuning
for details on
autotuning.
Perform autotuning. If the motor can be operated, perform rotational autotuning. If the motor cannot be oper-
ated, perform stationary autotuning 1 or 2. Refer to the following section on
Autotuning
for details on
autotuning.
Autotuning
Use the following procedure to perform autotuning if using the vector control method or the cable length is
long, etc. Motor constants will be set automatically.
If the control method was changed after autotuning, be sure to perform autotuning again.
One of the following four autotuning modes can be set.
•
Rotational autotuning
•
Stationary autotuning 1
•
Stationary autotuning for line-to-line resistance only
Precautions Before Using Autotuning
Read the following precautions before using autotuning.
•
Autotuning the Inverter is fundamentally different from autotuning the servo system. Inverter autotuning
automatically adjusts parameters according to detected motor constants, whereas servo system autotuning
adjusts parameters according to the detected size of the load.
•
When speed or torque precision is required at high speeds (i.e., 90% of the rated speed or higher), use a
motor with a rated voltage that is 20 V less than the input power supply voltage of the Inverter for 200V-
class Inverters and 40 V less for 400V-class Inverters. If the rated voltage of the motor is the same as the
input power supply voltage, the voltage output from the Inverter will be unstable at high speeds and suffi-
cient performance will not be possible.
•
Use stationary autotuning 1
whenever performing autotuning for a motor that is connected to a load.
•
Use rotational autotuning whenever performing autotuning for a motor that has fixed output characteris-
tics, when high precision is required, or for a motor that is not connected to a load.
•
If rotational autotuning is performed for a motor connected to a load, the motor constants will not be found
accurately and the motor may exhibit abnormal operation. Never perform rotational autotuning for a motor
connected to a load.
•
If the wiring between the Inverter and motor changes by 50 m or more between autotuning and motor
installation, perform stationary autotuning for line-to-line resistance only.
•
If the motor cable is long (50 m or longer), perform stationary autotuning for line-to-line resistance only
even when using V/f control.
•
The status of the multi-function inputs and multi-function outputs will be as shown in the following table
during autotuning. When performing autotuning with the motor connected to a load, be sure that the hold-
ing brake is not applied during autotuning, especially for conveyor systems or similar equipment.
or 2
Flux Vector Control (A1-02 = 3)
•
Stationary autotuning 2
or 2