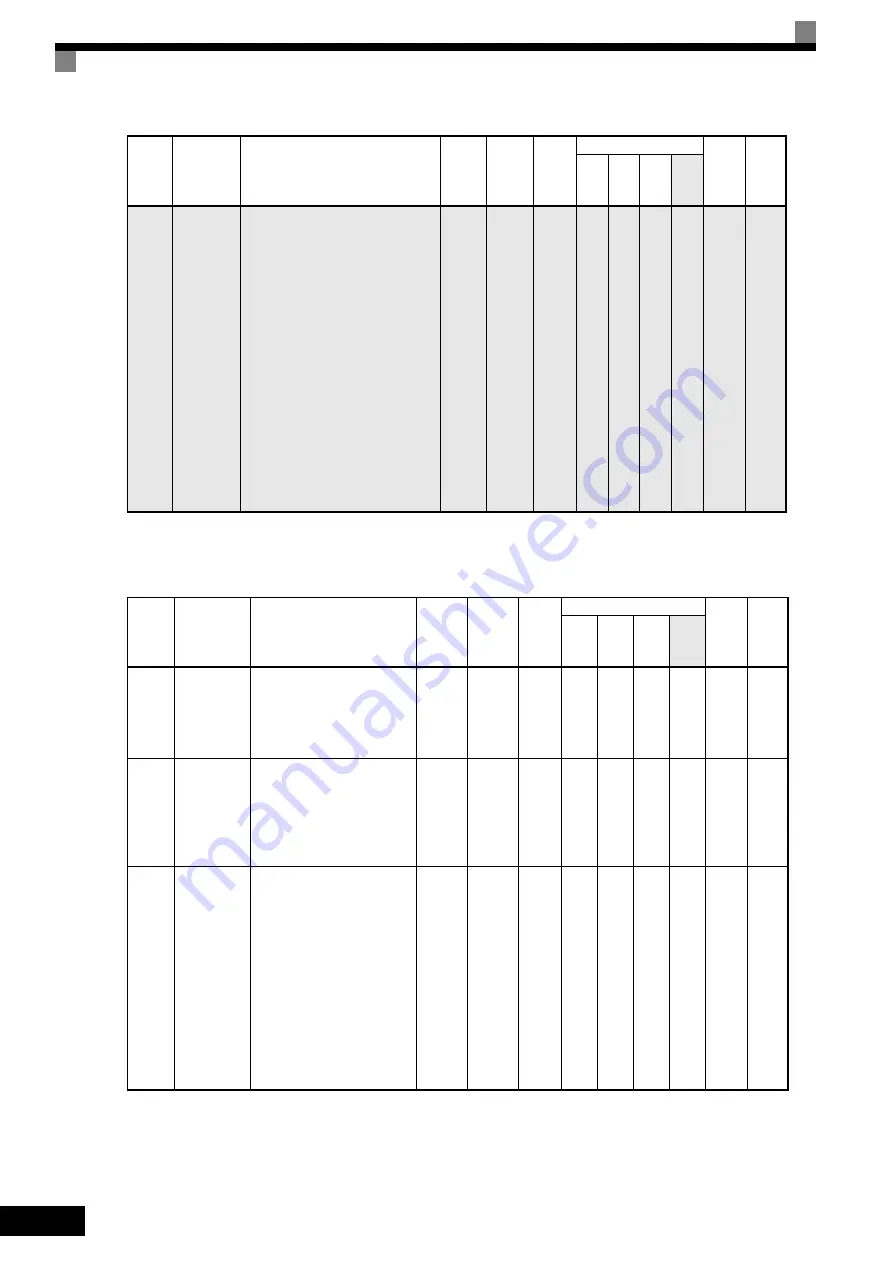
5
-64
Hardware Protection: L8
User constants for hardware protection functions are shown in the following table.
L7-07
Control
method
selection
for torque
limit dur-
ing accel-
eration
and decel-
eration
Select the control method for the
torque limit during acceleration
and deceleration.
0: Proportional control (integral
control during constant speed)
1: Integral control
Usually, this constant does not
need to be set.
For applications in which the
torque limit will be reached during
acceleration and deceleration,
torque control can be given priority
by selecting integral control.
When the torque is limited, the
acceleration and deceleration times
may increase or the motor speed
may not agree with the speed refer-
ence value.
0 or 1
0
No
No
No
A
No 4C9H
4-20
6-49
Con-
stant
Number
Name
Description
Setting
Range
Factory
Setting
Change
during
Opera-
tion
Control Methods
MEMO
BUS
Regis-
ter
Page
V/f
V/f
with
PG
Open
Loop
Vec-
tor
Flux
Vec-
tor
L8-01
Protect
selection for
internal DB
resistor
(Type ERF)
0: Disabled (no overheating
protection)
1: Enabled (overheating
protection)
0 or 1
0
No
A
A
A
A
4ADH 6-76
L8-02
Overheat
pre-alarm
level
Sets the detection tempera-
ture for the Inverter overheat
detection pre-alarm in
°
C.
The pre-alarm detects when
the cooling fin temperature
reaches the set value.
50 to
130
95
°
C
*1
No
A
A
A
A
4AEH 6-77
L8-03
Operation
selection
after over-
heat pre-
alarm
Sets the operation for when
the Inverter overheat pre-
alarm goes ON.
0: Decelerate to stop in
deceleration time C1-02.
1: Coast to stop
2: Fast stop in fast-stop time
C1-09.
3: Continue operation
(Monitor display only.)
A fault will be given in set-
ting 0 to 2 and a minor fault
will be given in setting 3.
0 to 3
3
No
A
A
A
A
4AFH 6-77
Con-
stant
Num-
ber
Name
Description
Setting
Range
Factory
Setting
Change
during
Opera-
tion
Control Methods
MEMO
BUS
Regis-
ter
Page
V/f
V/f
with
PG
Open
Loop
Vec-
tor
Flux
Vec-
tor