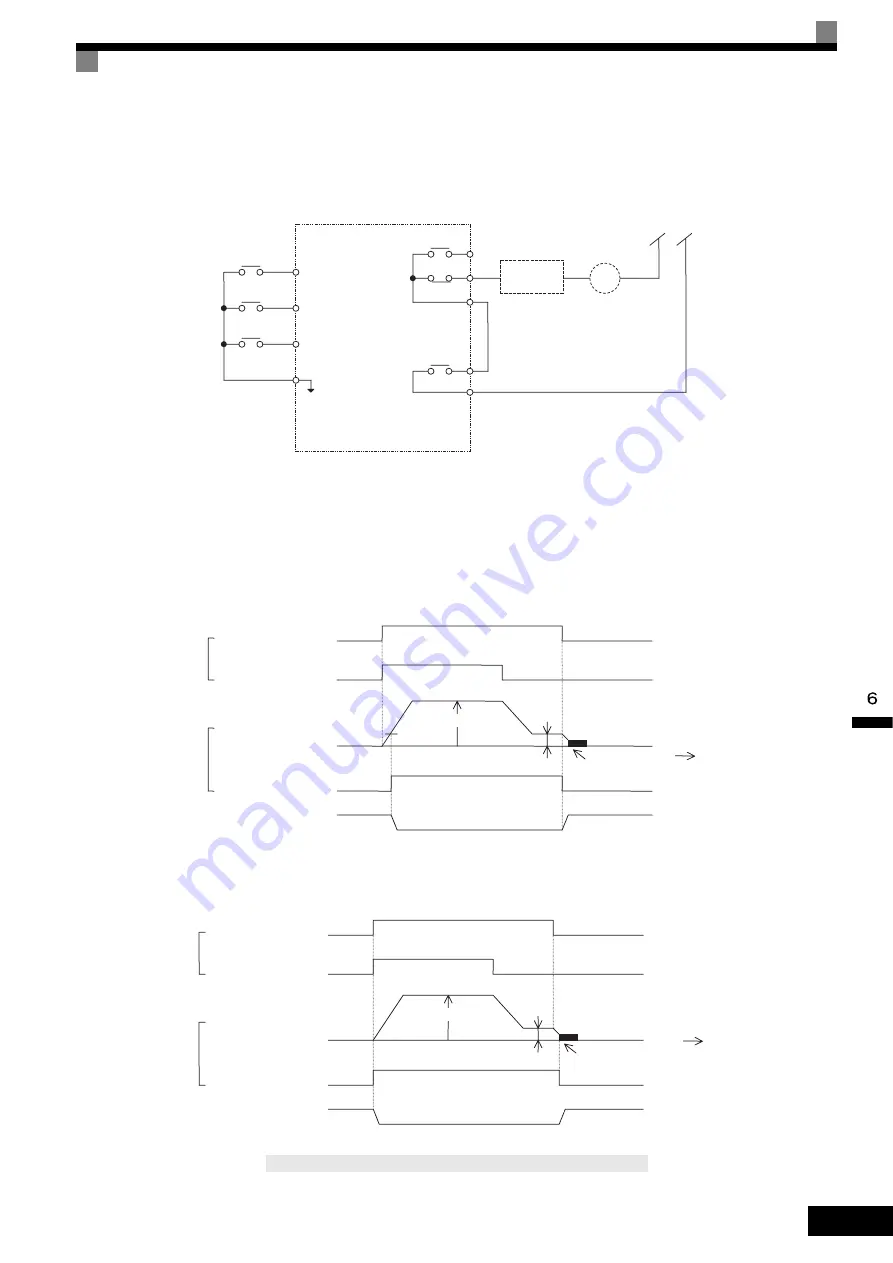
Using Inverters for Elevating Machines
6-
169
Sequence Circuit Configuration
The brake ON/OFF sequence circuit configuration is shown below.
Note Design the sequence so that the holding brake contact is open when the sequence operation conditions are satisfied and the contact between M1 and M2
is closed (ON).
Make sure that the holding brake contact is closed when the emergency stop signal or Inverter fault contact output signal is ON.
Fig 6.81 Brake ON/OFF Sequence Circuit Configuration
Time Chart
The brake ON/OFF sequence time charts are shown in Figs. 6.82 and 6.83.
Note For variable speed operation by an analog signal, set to b1-01 = 1.
Fig 6.82 Brake ON/OFF Sequence Time Chart (V/f, V/f with PG, open-loop vector)
Note For variable speed operation by an analog signal, set to b1-01 = 1.
BR
Inverter (Varispeed F7)
(Forward run)
UP
DOWN
HIGH/LOW
(Reverse run)
S2
(Multi-step speed reference 2)
MA
MB
MC
S6
M1
M2
SC
Fault contacts
S1
Holding brake
auxiliary relay coil
Sequence
circuit
Energizes the brake when ON
(250 VAC 1 A or less, 30 VDC
1 A or less)
Frequency
detection 2 or
During run
UP
S1-SC
S6-SC
OFF
OFF
d1-03
d1-01 (Enabled when b1-01 = 0)
L4-01
b4-01
OFF
DC injection braking
ON
ON
ON
M1-M2
OPEN
CLOSE
CLOSE
Input
Output
Output frequency
0
Frequency detection 2
(H2-01 = 05)
Time
High speed/
Low speed
Holding brake
operation
S1-SC
S6-SC
d1-01 (Enabled when b1-01 = 0)
DC injection braking (Zero-speed control)
M1-M2
Input
Output
Output frequency
0
During run 2
(H2-01 = 37)
Time
UP
OFF
OFF
d1-03
b2-01
OFF
ON
ON
ON
OPEN
CLOSE
CLOSE
High speed/
Low speed
Holding brake
operation
Fig 6.83 Brake ON/OFF Sequence Time Chart (Flux Vector)