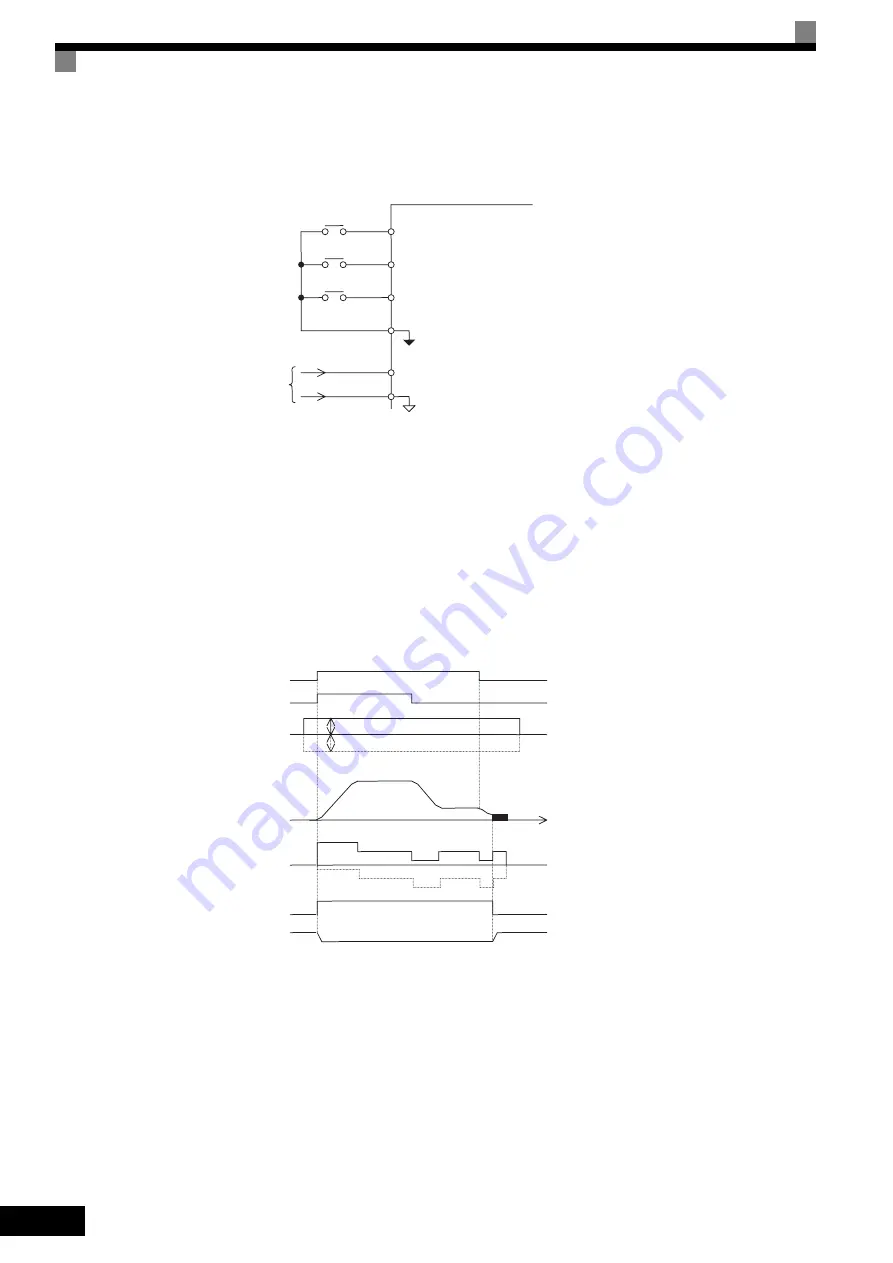
6
-176
Sequence Circuit Configuration
The following diagram shows the sequence circuit configuration for torque compensation.
Fig 6.84 Torque Compensation Sequence Circuit Configuration
Time Chart
•
Lifting
The analog signals corresponding to the load size are input as torque compensation signals from before the
Inverter starts until operation stops. (Factory setting: 10 V/100% torque)
Positive polarity is input for motor loads and negative polarity is input for regenerative loads.
The following diagram shows the time chart for lifting.
Fig 6.85 Torque Compensation Time Chart (Lifting)
•
Lowering
In the same way as for lifting, when the torque decreases, the analog signals corresponding to the load size are
input as torque compensation signals from before the Inverter starts until operation stops. (Factory setting: 10
V/100% torque)
Negative polarity is input for motor loads and positive polarity is input for regenerative loads.
The following diagram shows the time chart for lowering.
S1
UP
S2 (Reverse
run)
DOWN
HIGH/LOW
S6 (Multi-step speed reference 2)
SC
(Using elevator control circuit)
Torque compensation signal
−
10 to +10 V
A3
AC
(Forward run)
H3-04 (multi-function analog input terminal A3 signal level)
= 1 (
−
10 to +10 V)
H3-05 (multi-function analog input terminal A3 function
selection) = 14 (torque compensation)
Use H3-06 and H3-07 for fine tuning.
OFF
OFF
ON
UP (Forward)
ON
Analog signals corresponding to load size
Same as above
Torque compensation
signal: 0
HIGH/LOW
Output frequency
0
Motor torque
0
OFF
ON
During run 2
OPEN
Holding brake operation
CLOSE
(Motor load: Inputs positive polarity.)
(Regenerative load: Inputs negative polarity.)
t
(Motor load)
(Regenerative load)
Zero-speed control