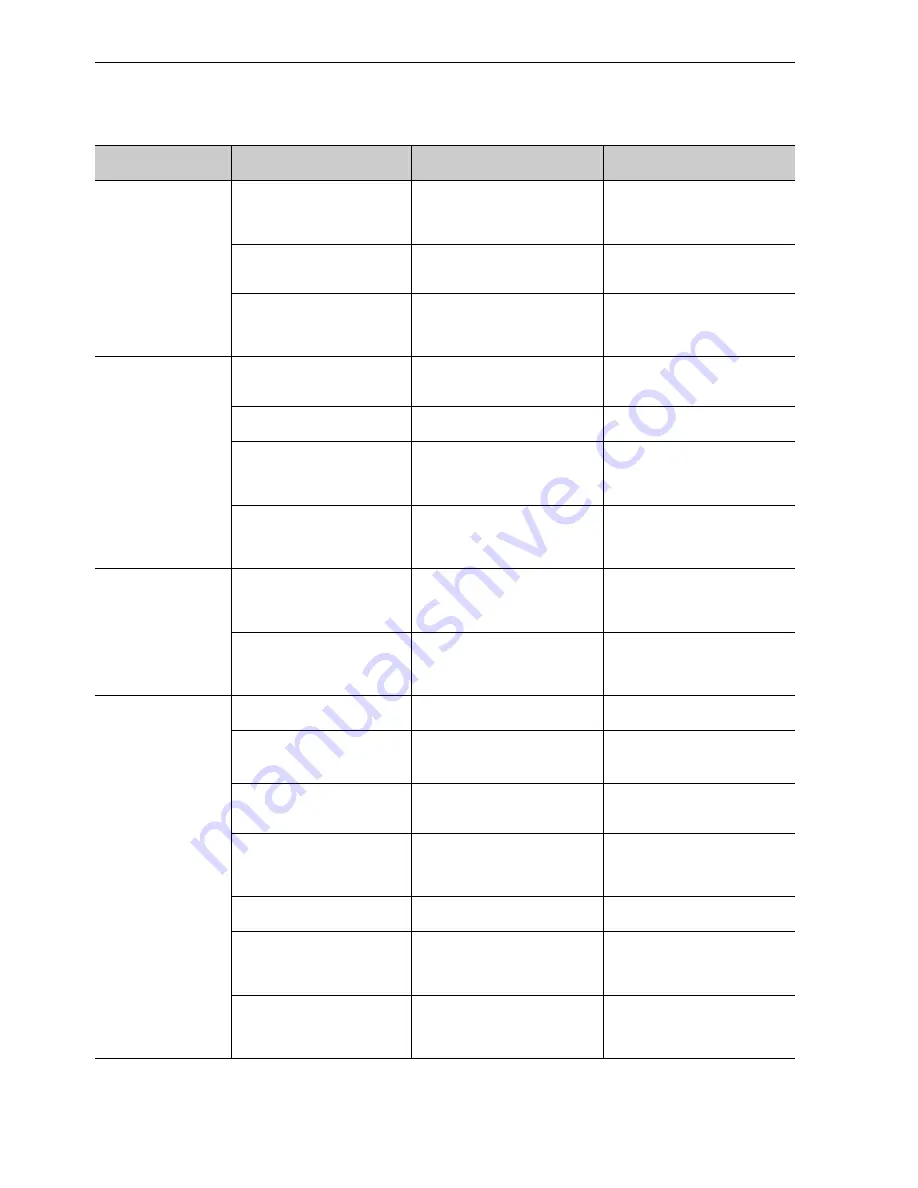
11 Inspection, Maintenance, and Troubleshooting
11.2.3 Troubleshooting of the Servo Drive Alarms
11-28
A.C91:
Encoder
Communications
Position Data Error
The noise interference occurred
on the input/output signal line
because the encoder cable is bent
and the sheath is damaged.
Check the encoder cable and con-
nector.
Confirm that there is no problem
with the encoder cable layout.
The encoder cable is bundled
with a high-current line or near a
high-current line.
Check the encoder cable layout.
Confirm that there is no surge volt-
age on the encoder cable.
The FG potential varies because
of influence from machines on
the servomotor side, such as the
welder.
Check the encoder cable layout.
Properly ground the device to sepa-
rate from the encoder FG.
A.C92:
Encoder
Communications
Timer Error
Noise interference occurred on
the input/output signal line from
the encoder.
−
Take countermeasures against
noise.
Excessive vibration and shocks
were applied to the encoder.
Check the operating environment.
Reduce the machine vibration, or
correctly install the servomotor.
Encoder failure
−
Turn the power supply OFF and
then ON again. If the alarm still
occurs, the servomotor may be
faulty. Replace the servomotor.
SERVOPACK failure
−
Turn the power supply OFF and
then ON again. If the alarm still
occurs, the SERVOPACK may be
faulty. Replace the SERVOPACK.
A.CA0:
Encoder Parameter
Error
Encoder failure
−
Turn the power supply OFF and
then ON again. If the alarm still
occurs, the servomotor may be
faulty. Replace the servomotor.
SERVOPACK failure
−
Turn the power supply OFF and
then ON again. If the alarm still
occurs, the SERVOPACK may be
faulty. Replace the SERVOPACK.
A.CB0:
Encoder Echoback
Error
The encoder wiring and contact
are incorrect.
Check the encoder wiring.
Correct the encoder wiring.
Noise interference occurred due
to incorrect encoder cable specifi-
cations.
−
Use tinned annealed copper twisted-
pair or shielded twisted-pair cable
with a core of at least 0.12 mm
2
.
Noise interference occurred
because the wiring distance for
the encoder cable is too long.
−
The wiring distance must be 20 m
max.
The FG potential varies because
of influence from machines on
the servomotor side, such as the
welder.
Check the encoder cable and con-
nector.
Make the grounding for the
machine separately from encoder
side FG.
Excessive vibration and shocks
were applied to the encoder.
Check the operating environment.
Reduce the machine vibration or
correctly install the servomotor.
Encoder failure
−
Turn the power supply OFF and
then ON again. If the alarm still
occurs, the servomotor may be
faulty. Replace the servomotor.
SERVOPACK failure
−
Turn the power supply OFF and
then ON again. If the alarm still
occurs, the SERVOPACK may be
faulty. Replace the SERVOPACK.
(cont’d)
Alarm:
Alarm Name
Cause
Investigative Actions
Corrective Actions