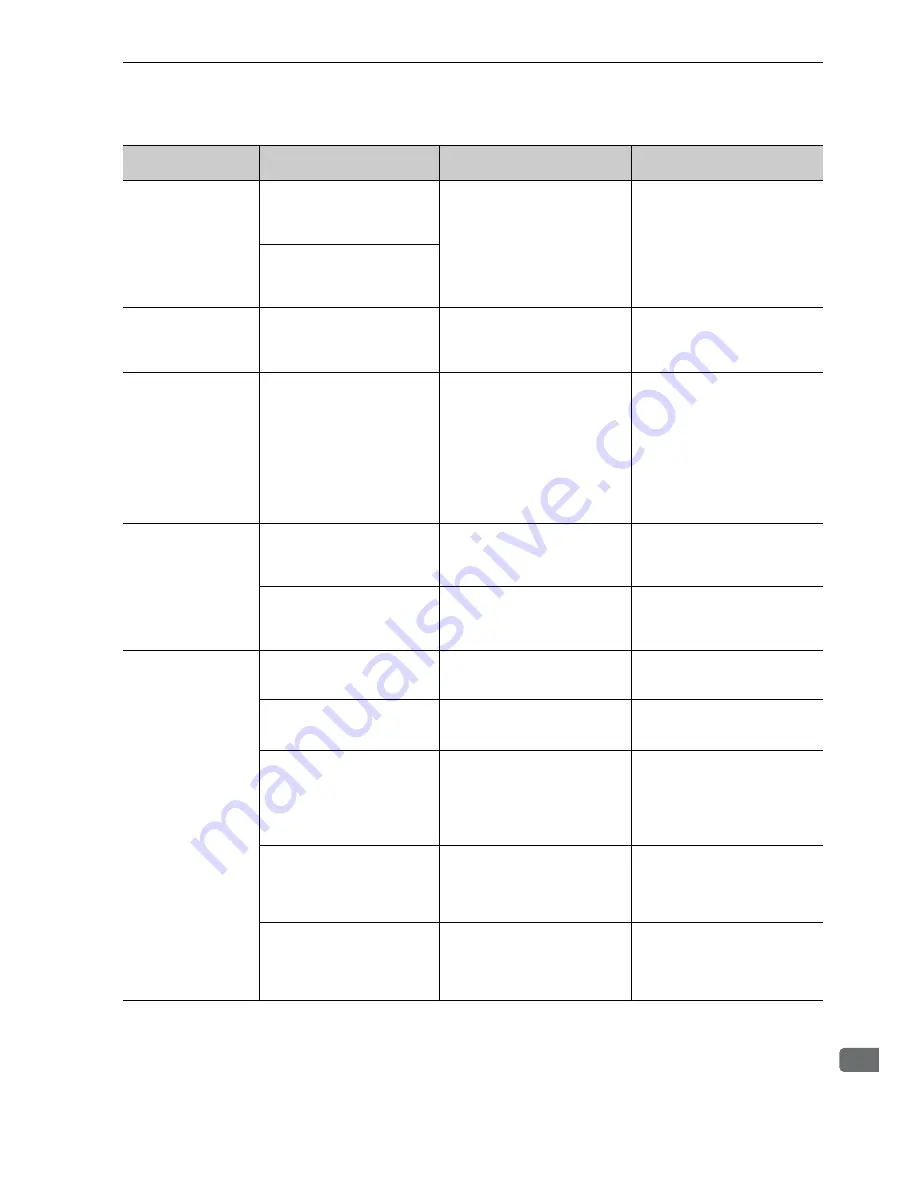
11.2 Alarm Displays
11-27
Inspection, Maintenance, and
Troubleshooting
1
1
A.C52:
Polarity Detection
Uncompleted
An attempt was made to detect
the magnetic pole for the high-
speed winding (for motors with a
winding selection).
−
Perform magnetic pole detection for
the low-speed winding.
An attempt was made to detect
the magnetic pole when changing
the winding (for motors with a
winding selection).
C53:
Out of Range for
Polarity Detection
The travel distance during mag-
netic pole detection exceeded the
magnetic pole detection travel
range in Pn494.
−
Increase the magnetic pole detec-
tion travel range in Pn494.
Increase the magnetic pole detec-
tion speed loop gain in Pn481.
C54:
Polarity Detection
Error 2
The motor’s electrical angle dur-
ing magnetic pole detection con-
firmation exceeded the magnetic
pole detection allowable devia-
tion range in Pn498.
−
Increase the magnetic pole detec-
tion confirmation torque in Pn495.
Increase the magnetic pole detec-
tion allowable deviation range in
Pn498 (however, a motor overheat-
ing alarm or overload alarm may
occur).
Reduce the external force on the
motor’s stator to about 10% or less
of the motor’s rated torque.
A.C80:
Absolute Encoder
Clear Error
(Multiturn Limit Setting
Error)
Encoder failure
−
Turn the power supply OFF and
then ON again. If the alarm still
occurs, the servomotor may be
faulty. Replace the servomotor.
SERVOPACK failure
−
Turn the power supply OFF and
then ON again. If the alarm still
occurs, the SERVOPACK may be
faulty. Replace the SERVOPACK.
A.C90:
Encoder
Communications Error
Contact fault of encoder connec-
tor or incorrect encoder wiring.
Check the encoder connector con-
tact status.
Re-insert the encoder connector and
confirm that the encoder is correctly
wired.
Encoder cable disconnection or
short-circuit.
Or, incorrect cable impedance.
Check the encoder cable.
Use the encoder cable with the
specified rating.
Corrosion caused by improper
temperature, humidity, or gas
Short-circuit caused by intrusion
of water drops or cutting oil
Connector contact fault caused by
vibration.
Check the operating environment.
Improve the operating environmen-
tal conditions, and replace the cable.
If the alarm still occurs, replace the
SERVOPACK.
Malfunction caused by noise
interference.
−
Correct the wiring around the
encoder to avoid noise interference
(Separate the encoder cable from
the servomotor main circuit cable,
improve grounding, etc.)
SERVOPACK failure
−
Connect the servomotor to another
SERVOPACK, and turn ON the
control power. If no alarm occurs,
the SERVOPACK may be faulty.
Replace the SERVOPACK.
(cont’d)
Alarm:
Alarm Name
Cause
Investigative Actions
Corrective Actions