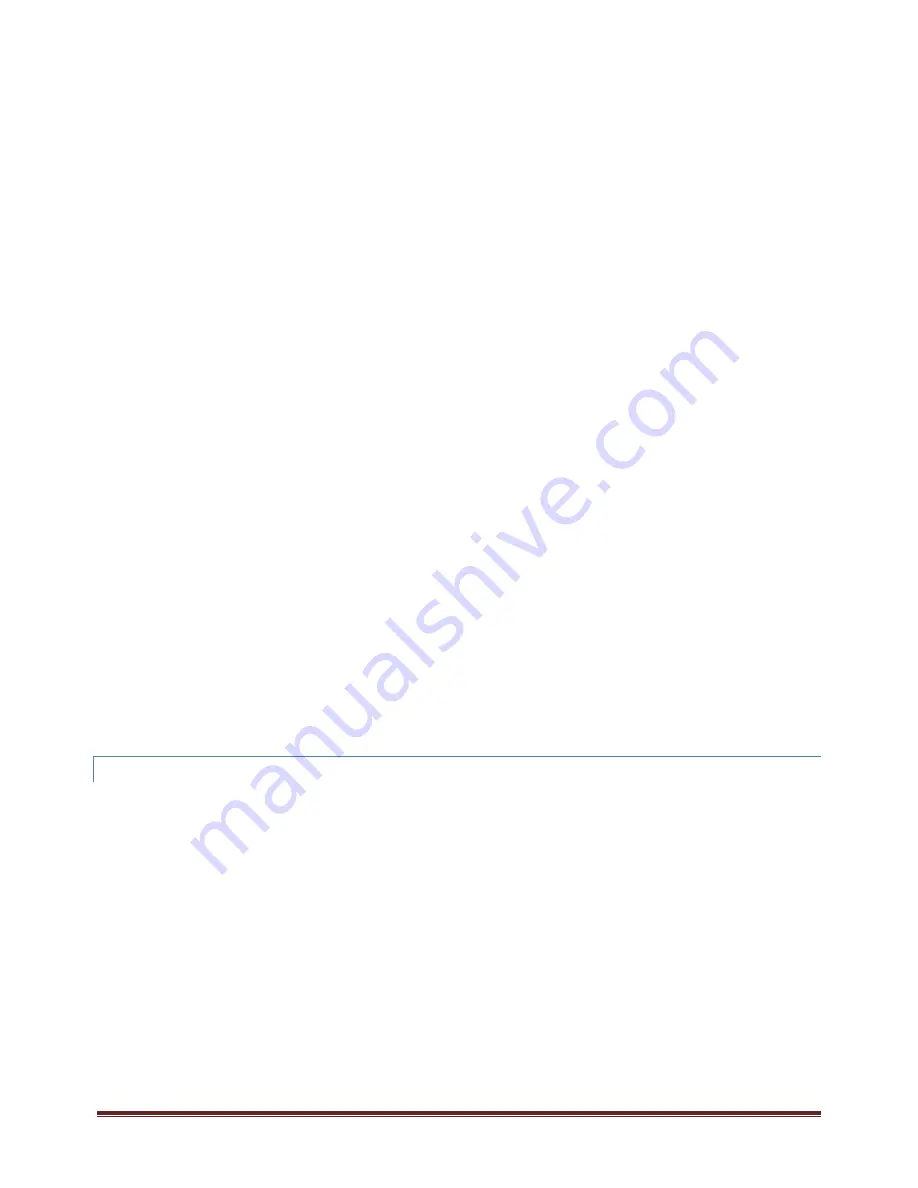
XT2640 Operating Manual
13 July 2016
Page 80 of 187
16.3.2.4
HARMONICS
SETTING
If harmonics measurements are not required then this should be set to either 0 or 1 (if set to 1 then the vectors and cycle view
screens are available, otherwise they are not).
Otherwise, this setting depends on the BANDWIDTH setting method selected. Generally, because of the presence of the PWM carrier
signal, measurement of more than a few harmonics is inappropriate in these applications.
1.
BANDWIDTH set to UNFILTERED. The XT2640 applies sufficient bandwidth restrictions only to harmonics measurements
in this case so it is necessary to ensure that harmonic measurements do not include any significant artifacts of the PWM
carrier frequency. You should compute the highest required harmonic having a frequency of ¼ of the PWM carrier
frequency and enter that number (or less) for the HARMONICS setting. If the drive is subsequently operated at a different
modulation frequency then this setting may need to be altered. For example, if the modulation frequency is 50Hz and the
PWM carrier frequency is 5kHz then the highest recommended HARMONICS setting is (1/4 * 5000 / 50) = 25.
2.
BANDWIDTH set to USER. In this case the value set for HARMONICS selects the highest limit for the number of available
harmonics but the XT2640 will also automatically and dynamically limit it to the harmonic having a frequency of ½ of the
BANDWIDTH frequency setting. So in this case this setting only sets a maximum limit to the number of available
harmonics, typically the actual number is limited by the BANDWIDTH setting.
3.
BANDWIDTH set to AUTO‐TRACK. In this case the XT2640 will automatically limit the bandwidth to 3 times the frequency
of the highest harmonic set by the HARMONICS setting. You should set a HARMONICS setting of less than PWM carrier
frequency / (6*highest modulation frequency). For example, if the highest expected modulation frequency is 50Hz and the
PWM carrier frequency is 5kHz then the highest recommended HARMONICS setting is (5000 / (6*50)) = 16.
Note:
Generally either no harmonics measurements are needed (so set HARMONICS to 0 or 1), or only a few have significance to you
(so set HARMONICS to the lowest number possible).
The HARMONICS setting has no effect on non‐harmonic measurements (e.g. RMS voltage and current, and Watts, VA, VAR, and
PF).
Signals captured using the CYCLE VIEW screen are also affected by this choice, but signals captured by the SCOPE VIEW screen
are not.
16.3.2.5
RESPONSE
SETTING
Because of the various asynchronous signal contents and also because often the measurements being made are within an overall
control loop (e.g. motor speed control), these signals often have considerable variability so the use of result “smoothing” is
recommended. This is selected by your choice for the RESPONSE setting and MEDIUM is the recommended choice in most PWM
applications.
Note:
This setting applies to all measurement results.
Often in PWM applications harmonic results require more smoothing than non‐harmonic results because of the inter‐
harmonic and sub‐harmonic signal content present in these signals caused by the asynchronous nature of the carrier and
modulation frequencies, in those cases it is recommended to change the RESPONSE setting according to which results you
wish to obtain at that time. Changing this setting does not “restart” the smoothing but continues it, so changing the RESPONSE
setting while the signals are present is recommended to avoid unnecessarily long settling times when a long RESPONSE
setting is selected.
It is generally better to smooth results by applying a longer RESPONSE setting than selecting a longer LF/PERIOD setting as
the RESPONSE smoothing is a multi‐order smoothing filter whereas the effect of the measurement period is the equivalent of a
single order filter and also does not apply continuous filtering so has less effect.
16.3.3
PWM
GENERATOR
EFFICIENCY
MEASUREMENTS
In some applications it may be desired to measure both the output of a PWM power generator and also the supply to it, e.g. for power
generator efficiency measurements. This is achieved by configuring the two measurements in two different VPAs in the same
XT2640 as follows–
1.
If there will be significant changes to the levels or signals which require tracking for efficiency results and the supply is DC
which contains ripple at the modulation frequency of the PWM generator (or little ripple at any frequency) and all channels
are W type channels or all are not W type channels.
The MEAS MODE should be set to MULTI VPA.
The PWM generator output VPA should be configured as VPA1.
The DC supply VPA should be configured as VPA2 and DC measurements (FUND=NONE and COUPLING=DC ONLY).
The LF/PERIOD setting of the DC VPA (VPA2) should be set to “VPA1”.
Use the same RESPONSE setting in both VPAs.
In this manner the XT2640 will measure the DC supply exactly synchronously with the measurements of the PWM
generator output, and so will reject the ripple content and also will accurately track changes in efficiency caused by changes
in the signals.
2.
Same as option 1 above but the PWM measurement channels and the DC measurement channels are not of the same type.
The MEAS MODE should be set to SYNC VPA.
Both sets of measurements should be configured in separate VPAs. Any VPA can be used for either measurement and
both are independently configured.