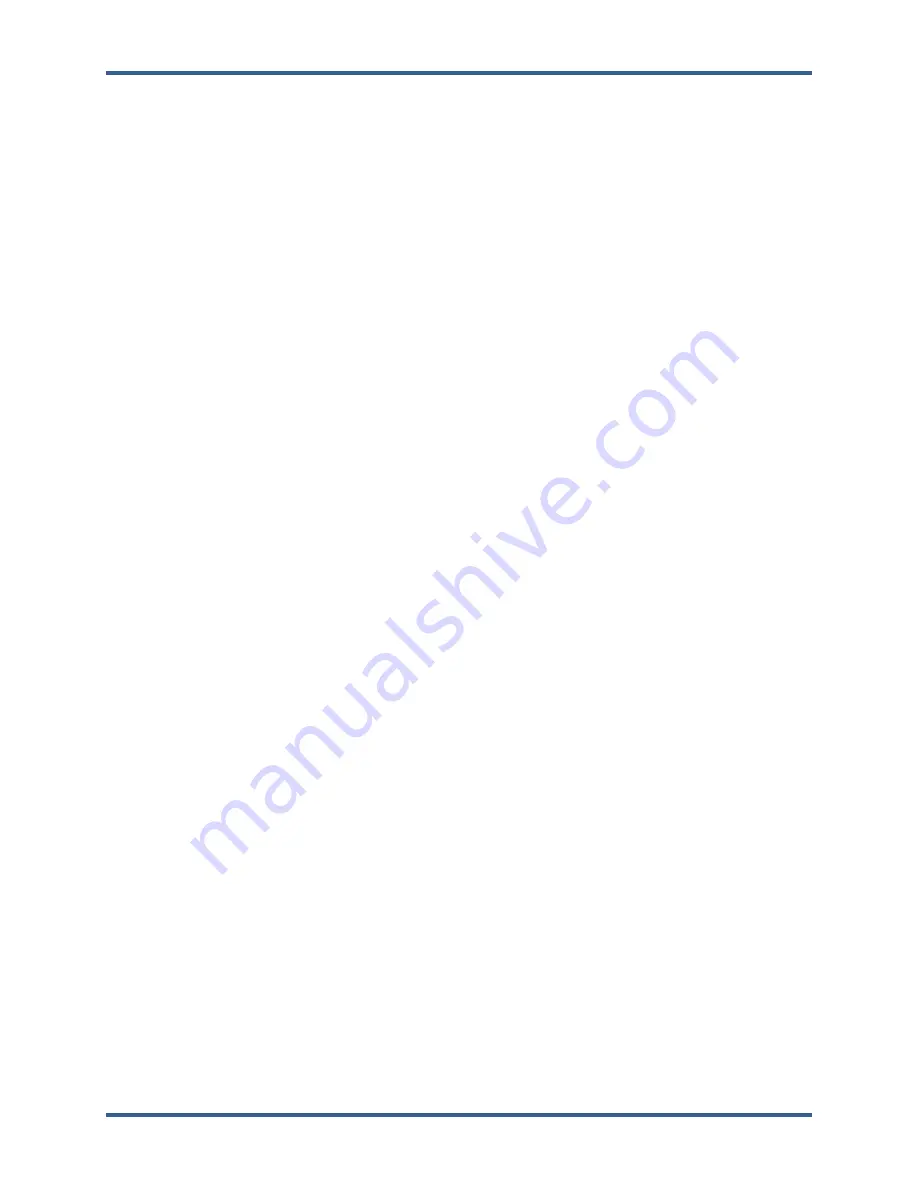
Manual 35018V1
505XT Digital Control System for Steam Turbines
Woodward
63
If this option is programmed it will be use in one of the following ways:
1. It will provide a second unique setpoint relative to this temperature input for each idle speed level
configured. For the unit to advance from one idle speed to the next, both temperature conditions must
be met.
2. Using the second temperature analog input makes available an option to use the temperature
difference between these two signals. Select the “Use Temperature Difference” checkbox in the
Turbine Start configuration menu under “Autostart Sequence Settings”. For the unit to advance from
one idle speed to the next, the difference between Start Temperature 1 and 2 must be less than the
configured amount, in addition to the individual temperature set points.
When a temperature input fails then the conditions to continue from any idle speed will not be met, which
means that the start sequence will not continue past that idle level. In order to proceed with the start
sequence, the temperature input can be overridden via the Service menu.
If configured, the following conditions must be met to continue from each idle speed:
“Auto Halt at Idle Setpoints” not selected or operator ‘Continue’ command.
Idle delay time expired.
Start Temperature 1 is greater than “Temperature 1 Setpoint”.
Start Temperature 2 is greater than “Temperature 2 Setpoint”.
Difference between Start Temperature 1 and 2 is less than “Max Temperature Difference”.
Speed Control Overview
The speed control receives a turbine speed signal from one or two magnetic pickups or proximity probes.
The ‘MPU Gear Ratio’ and the ‘Teeth Seen By MPU’ settings are configured to allow the 505 to calculate
actual turbine speed. The control will always use the highest speed signal received as the validated
turbine speed process variable. The Speed PID (proportional, integral, derivative control amplifier) then
compares this signal to the set point to generate an output signal to the speed low signal select bus
(LSS). In a single valve application, this signal then goes through a second low signal select bus which
produces the output demand to governor valve actuator. In an Extraction/Admission turbine application
the speed LSS value feeds into the Ratio Limiter equation that will control the output demands to both the
HP and LP actuators.
The speed control’s set point is adjustable with raise or lower commands, through the 505 keypad,
remote contact inputs or the communication line. This set point can also be directly set by entering a new
set point through the 505 keypad or via Modbus. In addition, an analog input can be programmed to
remotely position the speed set point.