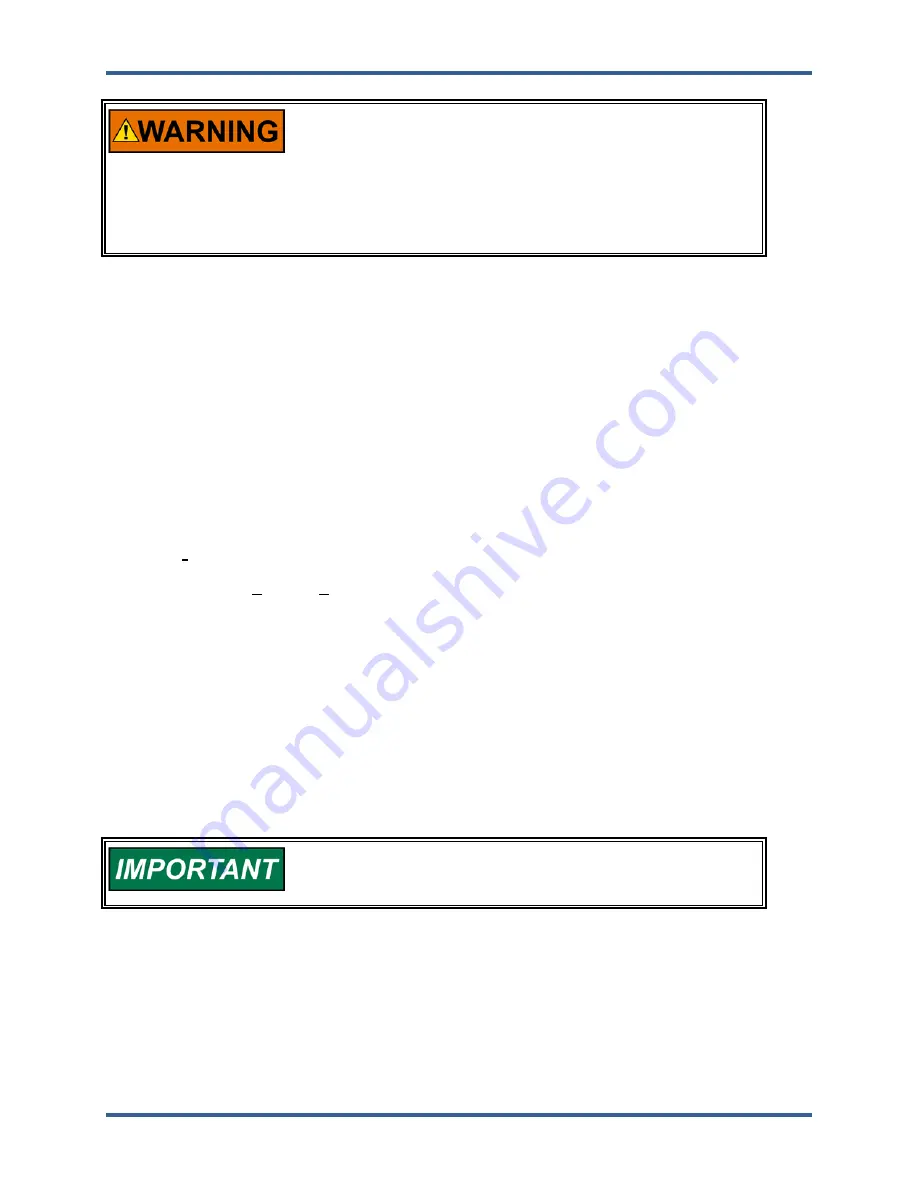
Manual 35018V1
505XT Digital Control System for Steam Turbines
Woodward
112
Manual Valve
Demand
Use caution when adjusting manual demand as the 505 is no
longer in control of any speed, load, or process. It is the
responsibility of the operator to ensure safe operation of all
processes related to valve movement. Use caution even while
using this feature to hold the valve position as the 505 may not
react to any system upsets until the conditions have become
unsafe. Failure to do so may result in loss of control with
possible personal injury, loss of life, or property damage.
Inlet Steam Pressure Compensation
The inlet pressure compensation feature is used to adjust the control response based on variations in the
inlet steam header pressure. Inlet pressure compensation is enabled in Configure Mode (under Operating
Parameters). To use this feature, an analog input must be configured as inlet steam pressure.
Once this is configured, the Pressure compensation curve will be available in the Service Menu screens.
The compensation factor is determined by a user-defined curve. The X values of the curve points are inlet
pressures in engineering units. The Y values of the curve points are a gain multiplier on the HP valve
demand. By default, all Y values are initially set to 1.0. The X values should be set to the expected range
of inlet pressure for normal operation, with at least one Point being the rated pressure and a gain of 1.0.
Increase the gain (Y values) for pressures less than rated and decrease the gains for pressures greater
than rated. This gain factor is applied to the valve demand prior to the valve linearization curve (if that
option is used).
Example:
Curve for a Steam Turbine rated at 500 psi and operating range of +/-150 psi.
X Y
Point
1
350 1.2
Point
2
400 1.1
Point
3
500 1.0
Point
4
600 0.9
Point
5
650 0.8
All X values entered in the curve must be increasing. The curve block has been implemented such that it
will limit the gain to the first and last points entered by the user. If the inlet steam pressure signal fails,
then the curve is bypassed and the gain is forced to 1.0.
The gain output of this curve should be left at 1.0 (all Y values at 1.0) until the control PID gains have
been tuned at the rated inlet pressure. Once this is done, then the inlet pressure compensation curve
points can be set for other inlet pressures.
Pressure compensation will affect the accuracy of the droop
calculation when the 505 is configured for droop with valve
position control.
Isolated PID Control
The Isolated PID Controller can be configured to control any system process. Typically this controller is
configured and used to control seal gas or gland seal pressure, but it can also be used for any type of PID
loop.
The Isolated PID compares a 4–20 mA process signal with an internal setpoint to directly position an
analog output configured as Isolated PID output.