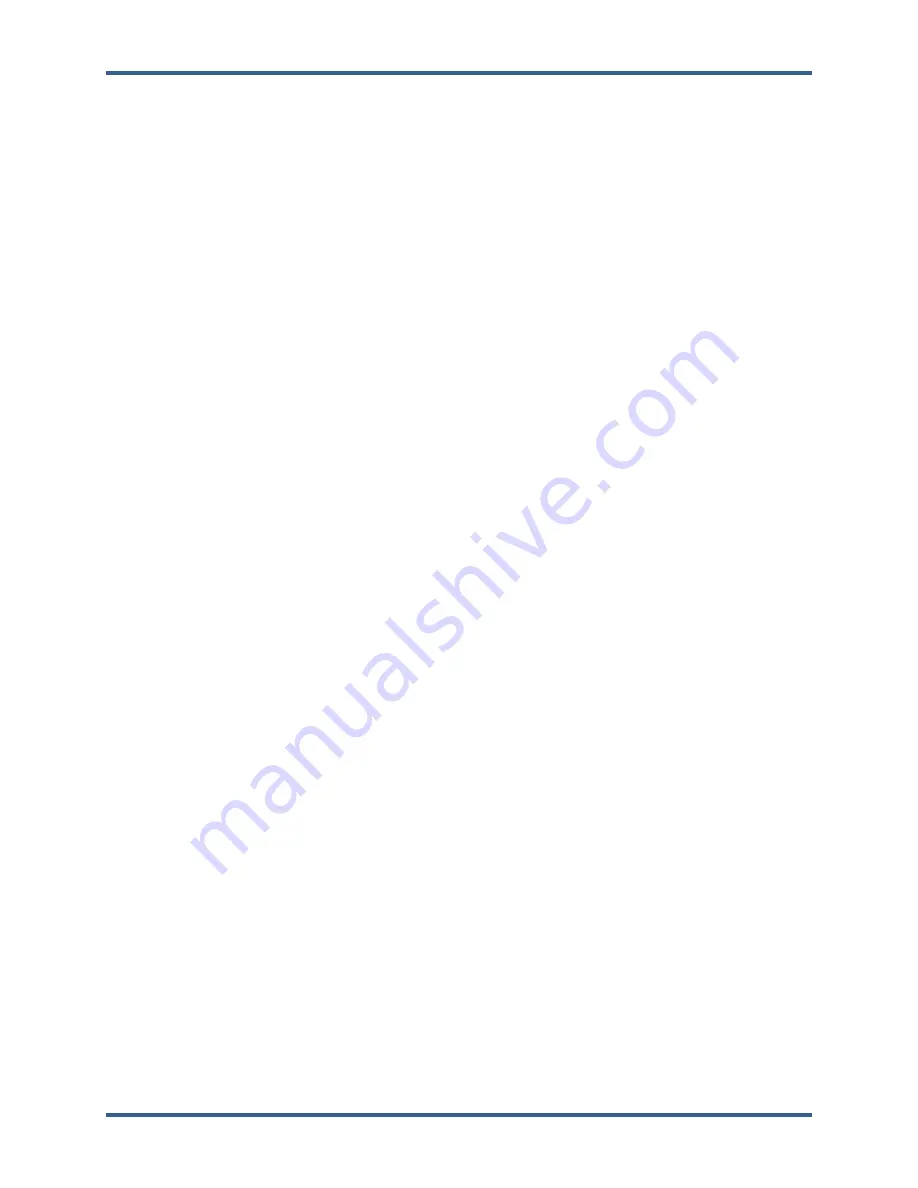
Manual 35018V1
505XT Digital Control System for Steam Turbines
Woodward
185
For Extraction/Admission type turbines, there is a third set of dynamics that can be set to optimize
operation within the steam performance map. These settings are identified as the ratio limiter dynamics
and are only used when the unit is On-Line and Extraction/Admission control is enabled. When first
tuning these settings (either manually or using OPTI Tune, they should be initialized to start with the
same settings as the On-Line dynamic settings.
Speed Droop
The Speed Loop controller can be programmed to use droop for control loop stability. For generator
applications, the ideal parameter to use is a Generator Load signal. If this is not available then the speed
loop will use actuator position droop. The actuator position droop feedback is convert to a load
percentage value
Cascade/Auxiliary Droop
The Cascade and Auxiliary controllers can be programmed to use droop for control loop stability. If the
parameter being controlled (Cascade or Auxiliary) is also being controlled by another device (letdown
station, boiler, or other turbine), droop is typically required for control loop stability. If required, no less
than 5% droop is recommend for stable operation.
Tuning Derivative
The value of the Derivative Ratio (DR) term can range from 0.01 to 100. If unsure of the correct value, set
the Speed control’s DR term to 5% and the Aux & Cascade controllers’ DR terms to 100%. In order to
simplify adjustment of the dynamics, adjusting the integral gain value sets both I and D terms of the PID
controller. The DR term establishes the degree of effect the integral gain value has on the "D" term, and
changes the configuration of a controller from input rate sensitive (input dominant) to feedback rate
sensitive (feedback dominant) and vice versa.
Another possible use of the DR adjustment is to reconfigure the controller from a PID to a PI controller.
This is done by adjusting the DR term to its upper or lower limits, depending on whether an input or
feedback dominant controller is desired.
A DR setting of 1 to 100 selects feedback dominant mode.
A DR setting of .01 to 1 selects input dominant mode.
A DR setting of .01 or 100 selects a PI only controller, input and feedback dominant respectively.
The change from one of these configurations to the other may have no effect during normal operation;
however, it can cause great differences in response when the governor is coming into control. (at start-up,
during a full load change, or during transfer of control from another channel).
An input dominant controller is more sensitive to the change-of-rate of its input (Speed, Cascade in or
Auxiliary in), and can therefore prevent overshoot of the set point better than a feedback dominant
controller. Although this response is desirable during a start-up or full load rejections, it can cause
excessive control motions in some systems where a smooth transition response is desired.
A controller configured as feedback dominant is more sensitive to the change-of- rate of its feedback
(LSS). A feedback dominant controller has the ability to limit the rate of change of the LSS bus when a
controller is near its set point but is not yet in control. This limiting of the LSS bus allows a feedback
dominant controller to make smoother control transitions than an input dominant controller.
Tuning Example
If the system is unstable, make sure the governor is the cause. This can be checked by closing the valve
limiter until it has control of the actuator output. If the governor is causing the oscillation, time the
oscillation cycle time. A rule-of- thumb is, if the system’s oscillation cycle time is less than 1 second
reduce the Proportional gain term. A rule-of-thumb is, if the system’s oscillation cycle time is greater the 1
second reduce the Integral gain term (proportional gain may need to be increased also).
On an initial start-up with the 505, all PID dynamic gain terms will require adjustment to match the
respective PID’s response to that of its control loop. There are multiple dynamic tuning methods available
that can be used with the 505’s PIDs to assist in determining the gain terms that provide optimum control
loop response times (Ziegler Nichols, etc.).