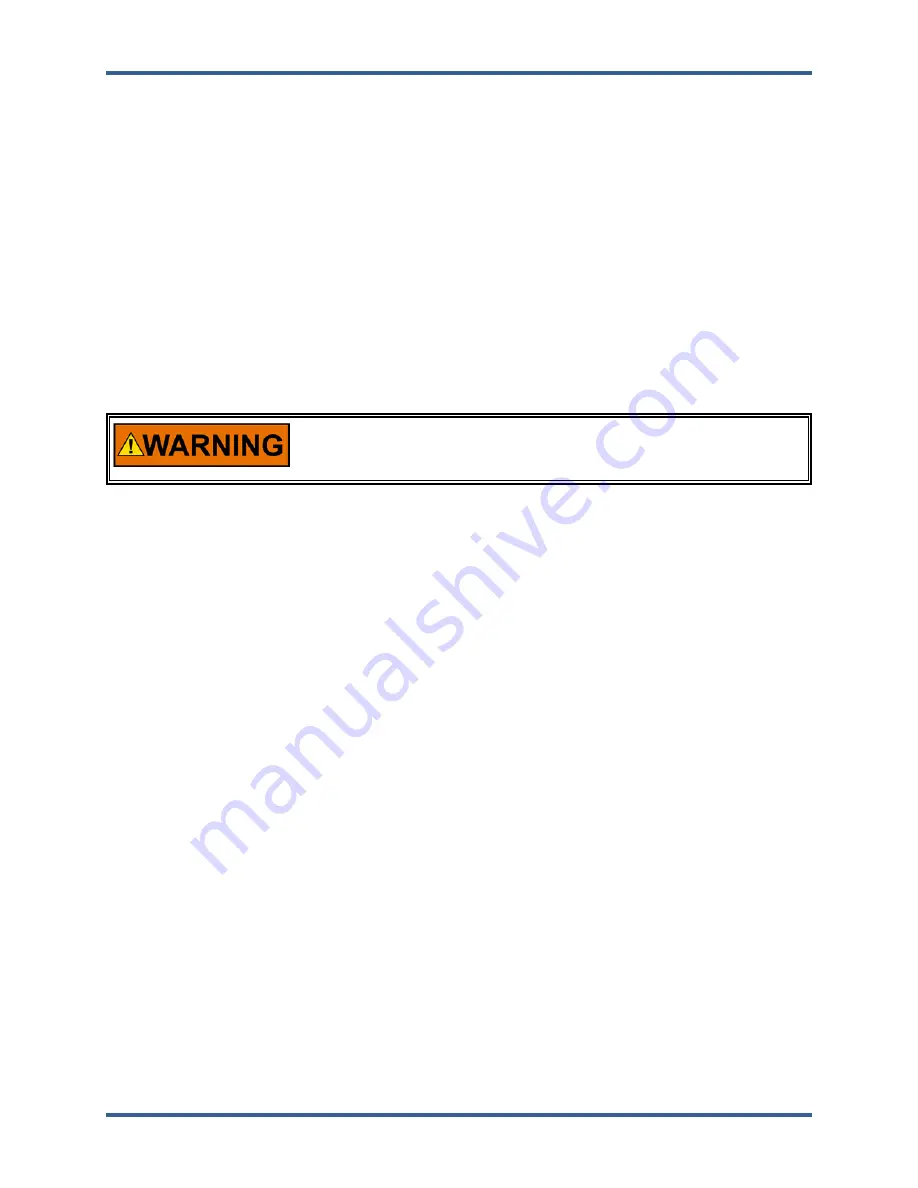
Manual 35018V1
505XT Digital Control System for Steam Turbines
Woodward
17
•
Load Droop and Isochronous Load sharing between units (with an DSLC-2 control)
•
Feed-forward loop for compressor units
•
High speed (10ms) datalog and Slow speed (1 sec) trendlog capture files
•
SNTP time synchronization via an Ethernet IP
•
Ability to expand system I/O with Woodward Linknet Distributed I/O nodes
•
Multiple digital communication links to other Woodward products (Woodward Links)
Using the 505XT
The 505XT control has three normal operating modes, Configuration Mode, Service Mode and the Run
Mode. See chapter 4 for more information about the User Levels required to enter each of these modes.
Configuration Mode –
This mode is used to select the options needed to configure the control to your specific turbine
application. While in this mode, the control will force the hardware into IO LOCK, meaning that no outputs
will be active, all Relays will be de energized, and all Analog output signals will be at 0 current. Once the
control has been configured, the Configuration mode is typically not needed again, unless turbine options
or operation changes. It is available to be viewed at any time.
A password is required to log into this mode.
Anytime the control is in IOLOCK all Relays will be de-energized and
all Analog outputs will be at 0 current. Ensure that the devices
receiving these commands are fail-safe at these states.
Calibration Mode –
This mode is used to calibrate, tune and adjust certain parameters either while the unit is shutdown, or
during turbine run time. A password is required to log into this mode.
Operation Mode -
This mode is the typical state for normal operations of the control and the turbine. The Run Mode is used
to operate the turbine from start-up through shutdown.
Functional Block Diagrams
An overview of the 505XT valve demands is shown in Figure 1-4. Most of the PIDs are optional
controllers, and are shown in the following diagrams for PID relationship purposes only. Later in this
manual, more detailed functional block descriptions will be given in relation to each control loop PID. The
Speed PID is always used and on Extraction/Admission type turbines the Extraction PID is required.