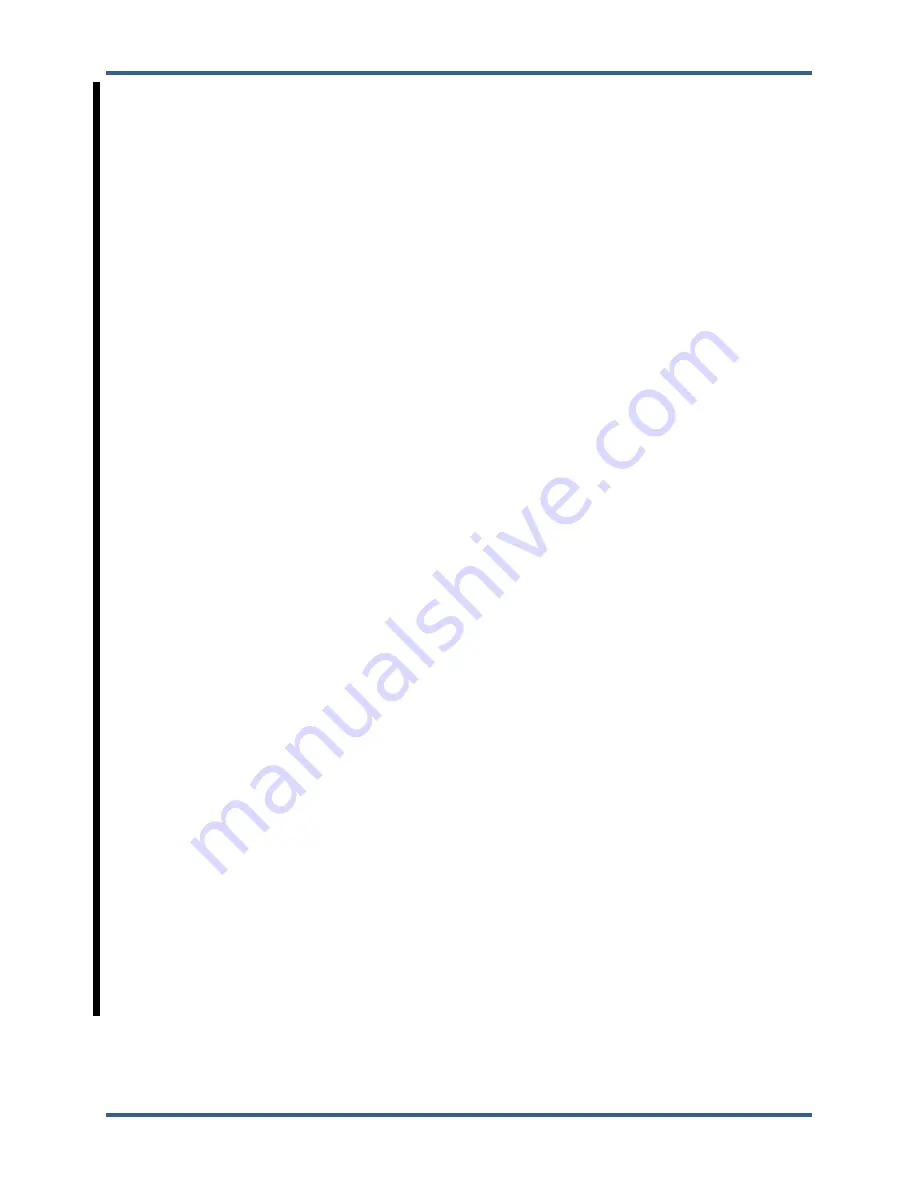
Manual 35018V1
505XT Digital Control System for Steam Turbines
Woodward
191
Most of the time, an alarm or fault indicates a problem with the steam turbine system that is outside of
PID tuning. The descriptions below help identify what in the system may be causing the less than ideal
control conditions. In some cases, suggestions to the Automated PID Optimizer configuration are
included, in order to try and achieve successful automatic tuning.
Alarms
Alarm 1
- Rate group not fast enough
This alarm indicates that the rate group of the block is not fast enough to provide optimum control for the
control loop, as measured. The rate group should be at least 20 times as fast as the system response.
Some causes of this alarm could be:
The process loop (like speed) controlled by the PID is too fast for the rate group (RG) of PID
If the control loop is position droop, the problem may be that there is no lag or other filter on the
between the PID output and the process input.
Some solutions for this alarm could be:
If it is not possible to change the rate group, the second solution would be to accept the suggested
dynamics if adequate, or detune the PID
If there is no lag or other filter on the between the PID output and the process input for position droop,
the solution would be to add a lag.
Alarm 2
– High overshoot on test step
This alarm indicates that the overshoot on the test step was greater than 50% of the step size. The
performance might be acceptable, depending on the system.
Some causes of this alarm could be:
The valve or turbine response is non-linear. This could occur due to:
Poppet valve staging, resulting in higher flow with the larger movement of the step, and lower flow
with the earlier smaller movements.
The actuator or valve response is slew rate limited
If the amount of overshoot were unacceptable, some solutions would be:
Verify that the poppet valve staging is correct.
If the poppet valve staging cannot be fixed, the turbine operating point could be adjusted (i.e. the
speed (process) and speed setpoint (SP) could be increased) to tune at the higher/lower flow point.
The FAST/SLOW input may need to be reduced, to achieve the desired response.
Alarm 4
– Response to test step sluggish
The test step response did not reach 50% of the setpoint during the test step, the response was sluggish.
The performance might be acceptable, depending on the system demands.
Some causes of this alarm could be:
The valve or turbine response is non-linear. This could occur due to:
Poppet valve staging, resulting in higher flow with the lower movement of the step, and higher flow
with the earlier smaller movements.
The actuator or valve response is slew rate limited
The process or sensor has a long deadtime
If the speed or the response is unacceptable, some solutions would be:
Verify that the poppet valve staging is correct.
If the poppet valve staging can’t be fixed, the turbine operating point could be adjusted (i.e. the speed
(process) and speed setpoint (SP) could be increased) to tune at the higher or lower flow point.
The FAST/SLOW input could be increased, to achieve the desired response.