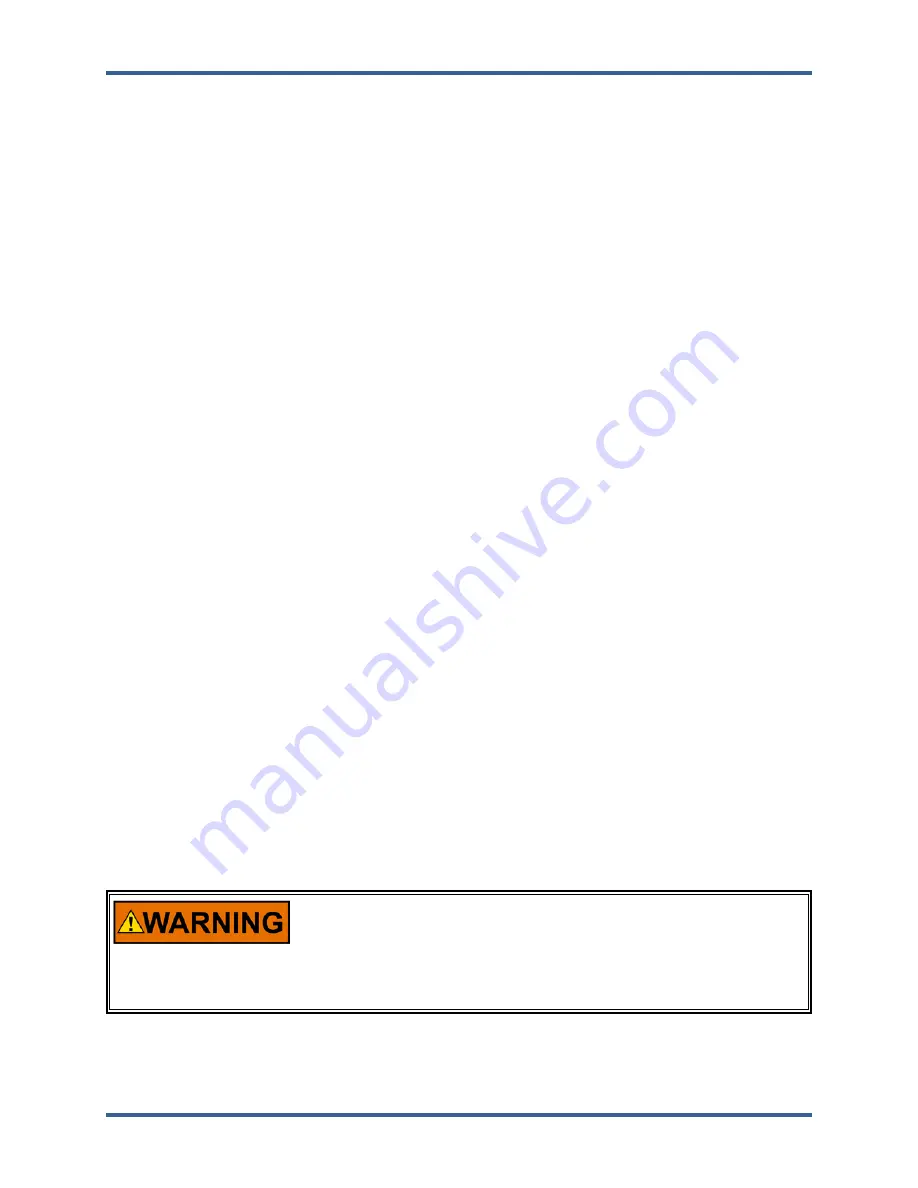
Manual 35018V1
505XT Digital Control System for Steam Turbines
Woodward
157
Valve/Actuator Calibration & Test
Before initial operation or after a turbine overhaul where any actuator or valve travel may have been
affected, the below Valve Calibration procedure should be followed to insure that the 505 is correctly
calibrated to the turbine control valve(s). When calibration is complete, 0 to 100% actuator position as
displayed by the 505 must equal 0 to 100% actual valve travel.
After a valid configuration has been entered, the actuator and valve minimum and maximum positions can
be adjusted and tested, if needed. Actuator and valve positions are determined by the drive current to the
actuator. The maximum actuator current can not be adjusted lower than the minimum actuator current
(see Table 4-2 below). The minimum actuator current can not be adjusted higher than the maximum
actuator current. The driver current ranges are determined by the setting in the Configuration Mode under
the Driver configuration menu.
When adjusting or testing actuator and valve travel, verify that sufficient valve overtravel at the minimum
stop is achieved (1%). This assures that each valve can fully close to completely shut off the steam flow
to the turbine.
Table 4-4. Actuator Driver Limits
Driver Limits
20–200 mA Range
4–20 mA Range
Overcurrent
210 mA
24 mA
Undercurrent
5 mA
0.6 mA
Max Output Current Range
10–200 mA
2–24 mA
Max Output Impedance
65
600
Min Stop Adjust Range
10–80 mA
2–20 mA
Max Stop Adjust Range
100–200 mA
10–24 mA
To ensure proper control to actuator resolution do not calibrate the span of the actuator output to less
than a range of 100 mA (20–160 mA output) or 12 mA
(4–20 mA output). If necessary, the actuator to valve linkage may need to be adjusted to ensure proper
505 to valve resolution.
Calibration Mode, required to force/stroke the actuator(s), is only available when the 505 control is in a
shutdown state. After enabling Calibration Mode, there are options available to adjust the minimum and
maximum stops and to manually stroke the output(s). The manual adjustment mode can be used to
stroke the actuator and valves from 0 to 100% after the minimum and maximum positions have been
adjusted. This allows both the actuator and valve to be tested for binding, play, resolution, linearity, and
repeatability.
As a safety precaution, if turbine speed ever exceeds either of the speed probe failed speed settings the
Calibration mode will be automatically disabled, which disables forcing of the actuator and takes actuator
currents to zero.
Calibration/Stroking Procedure
Before calibrating or testing, the unit must be tripped and the steam
supply removed. This is to ensure that opening the control valve(s)
will not allow steam into the turbine. Overspeeding the turbine may
cause damage to turbine and can cause severe injury or death to
personnel. STEAM TO THE TURBINE MUST BE SHUT OFF BY OTHER
MEANS DURING THIS PROCESS.