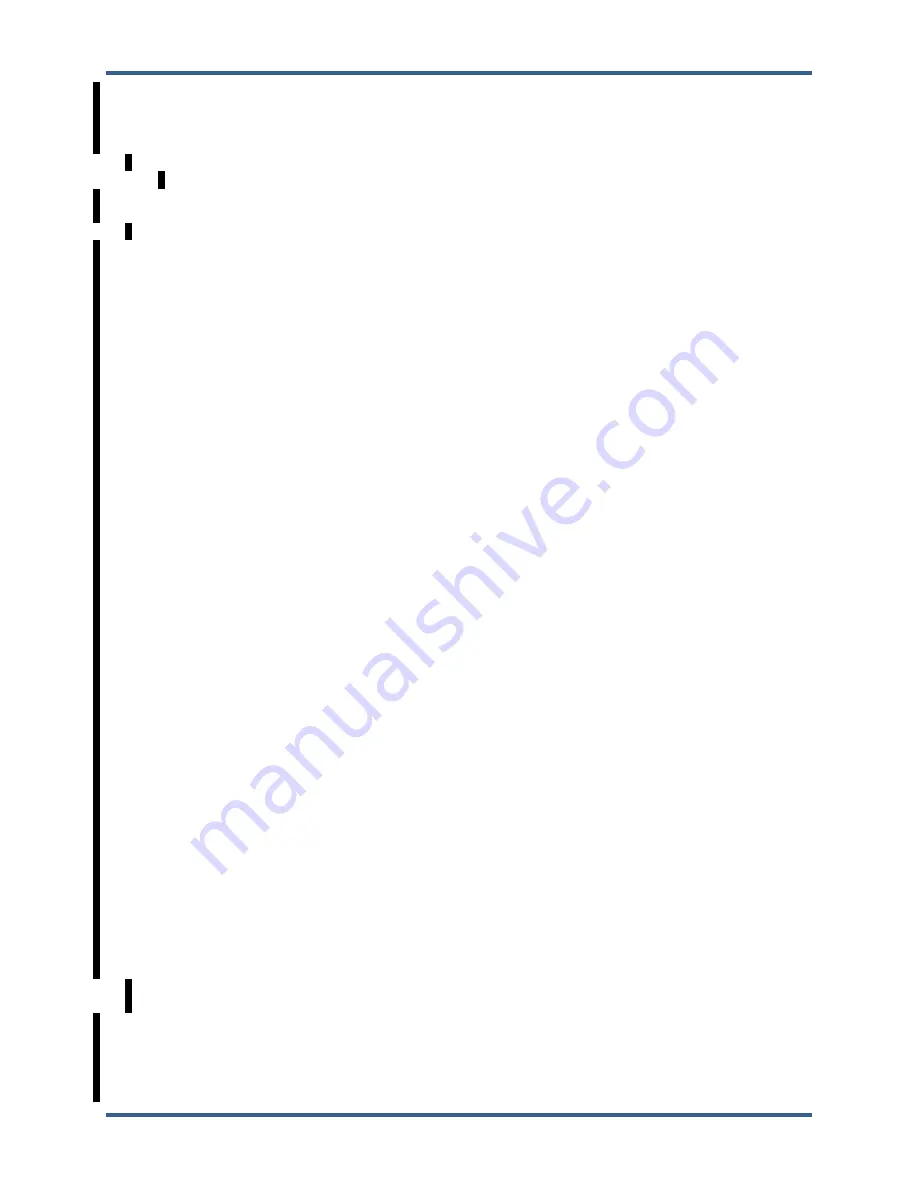
Manual 35018V1
505XT Digital Control System for Steam Turbines
Woodward
193
Faults
Fault 1
– CLR_STATE was toggled TRUE
This fault will only occur if the CLR_STATE input is toggled TRUE
Some causes of this fault could be:
The CLR_STATE input was toggled TRUE
This can occur when system dynamics are changed from Offline to Online
Some solutions for this fault would include:
Ensure that the CLR_STATE logic is correct, CLR_STATE has priority over automatic tuning.
Fault 2
– Process or droop movement limit low with respect to noise
This fault indicates that the process/droop movement (or noise on the process/droop input) is greater than
10% of the
Process Limit
or
Droop Limit
during the first seconds after the Automated PID Optimizer
routine is enabled. This is usually due to noise or drift on the process or droop input.
Some causes of this fault could be:
The
Response Timeout
is too long, the PID cannot increase the output movement fast enough to
counteract system drift.
The noise or system swing on the process/droop input is greater than 10% of the
Process Limit
and/or
Droop Limit
.
The system is not at steady state. As an example, if the Integral Gain input is low, there could be a
large error between process and setpoint.
Some solutions would include:
Decrease
Response Timeout
if the system is much faster than the time-out time.
Proportional Gain could be adjusted to make the system stable, if applicable.
Integral Gain could be adjusted to allow system to minimize error and/or slow hunt, if applicable.
The
Process Limit
or
Droop Limit
could be increased, if the system allows.
Check for excessive noise on process or droop signal, check shielding and grounding on the
applicable sensors and actuator(s).
Fault 3
– High response time variation
This fault indicates that the response variation exceeded the allowable limit. This fault will occur if the
response time variation is greater than a factor or 4, tuning would be unrepeatable.
Some causes of this fault could be:
The system has high friction, resulting in initial movements which are lower than later movement,
after the actuator or valve has broken free
The system has loose linkage or coupling, sometimes the system moves a lot, and sometimes it does
not.
The hydraulic pressure is moving during the tuning process.
The steam supply pressure is moving during the tuning process.
Some solutions for this fault would include:
Monitor the performance of the system, including the valve, steam pressure, hydraulic pressure, etc.
Use a datalog to verify proper I/O to the PID
Fault 4
– Process movement didn’t correlate to actuator movement
This fault indicates that the response did not correlate to the actuator movement.
Some causes of this fault could be:
The hydraulic pressure or steam supply is moving during the tuning process, if the actuator demand
is increasing but the supply is dropping, the actuator could close, or vice versa.
Some solutions for this fault would include:
Monitor the performance of the system, including the valve, steam pressure, hydraulic pressure, etc.
Use a datalog to verify proper I/O to the PID