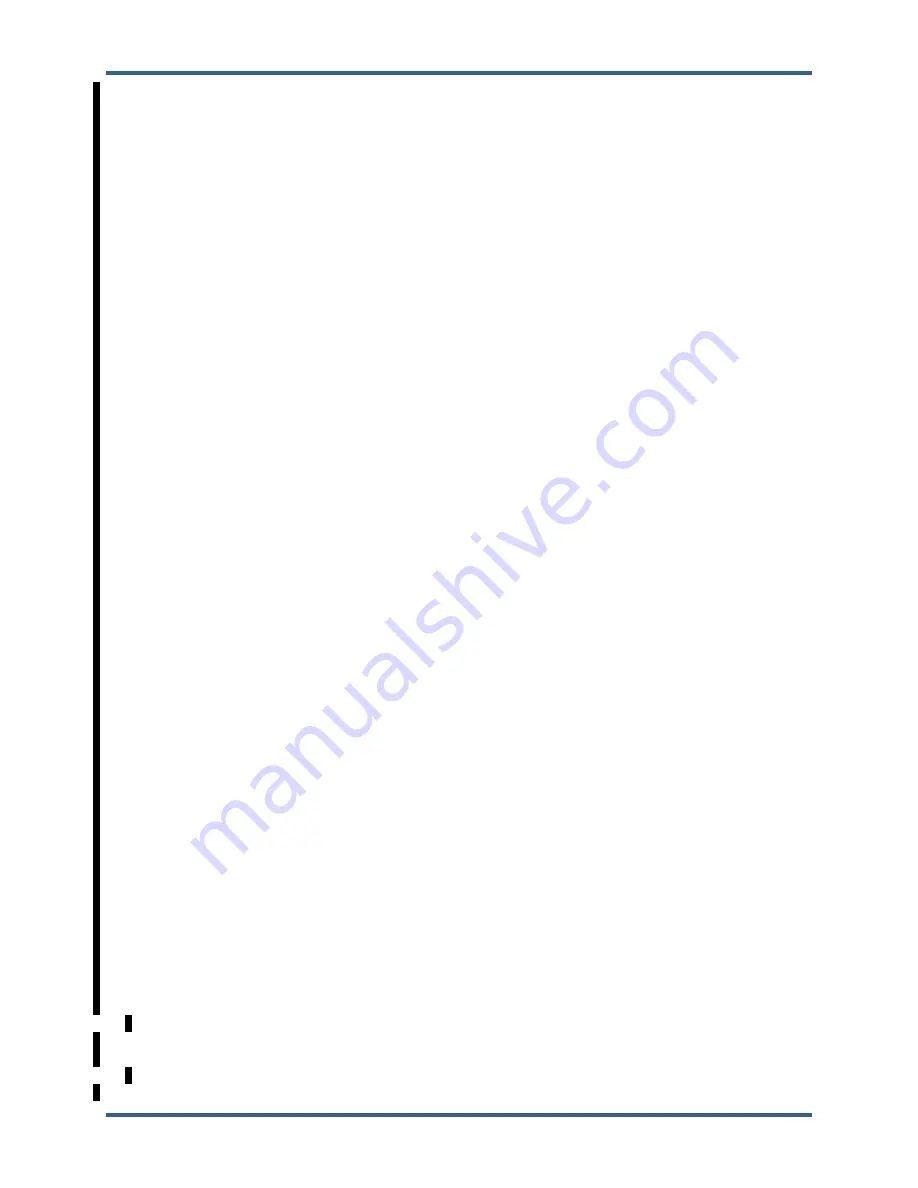
Manual 35018V1
505XT Digital Control System for Steam Turbines
Woodward
192
Alarm 8
- Actuator movement is limited
This alarm indicates that the actuator movement was limited during the Analysis Mode. This can result in
a response that is not optimum, depending on the system conditions.
Some causes of this alarm could be:
The
Act Limit
input is too low
The valve or actuator is close to its end of travel, limiting movement or effect.
If the response is not acceptable, some solutions would be:
If the response is not acceptable, the
Act Limit
could be increased
The system operating point could be moved away from the ends of the actuator and valve travel. This
would mean increasing or decreasing the SP input to the block.
Alarm 16
– High relative deadtime
This alarm indicates high deadtime in the system, relative to the system bandwidth. Deadtime is typically
measured on a step and is defined as the amount of time between when the SP starts to move, and when
the process starts to move.
Some causes of this alarm could be:
High friction on the valve or actuator
Lost motion on the valve or actuator or linkage
Hysteresis in the valve or actuator
Long lines, such as a pressure transducer or other transducer not located near the pressure of
interest.
A relatively slow recursion rate in the sensor, control, and/or driver
Asynchronous I/O in the sensor, control, and/or driver
Asynchronous communications between the sensor and control or control and driver (if digital)
Some solutions for this alarm could be:
With an oscilloscope, datalog, or logic analyzer, measure the system deadtimes.
The optimum solution to this problem would be to fix the system and remove the deadtime. If that is
not possible, the control should be de-tuned, to ensure adequate stability.
Alarm 32
– Process movement greater than Droop movement during Droop parameter tuning
This alarm indicates that the movement of the process parameter exceeded the movement of the Droop
parameter during droop tuning.
Some causes of this alarm could be:
Improper connections in the GAP. The process (speed) should be connected to the process input,
and the droop parameter (load, scaled in RPM) should be connected to the Droop input
The amount of initial actuator movement is set by the system noise. If this is too high the machine
might move more than the system can support.
The utility or plant frequency could be moving around.
Some solutions for this alarm could be:
Ensure that the block is connected correctly.
Reduce system noise.
Ensure that the
Act Limit
field is set correctly.
Alarm 64
–
Response Timeout
too short
This alarm indicates that the movement of the system did not respond enough during the
Response
Timeout
.
Some causes of this alarm could be:
The
Response Timeout
is too short for the turbine system response time
Some solutions for this alarm could be:
Increase
Response Timeout
.