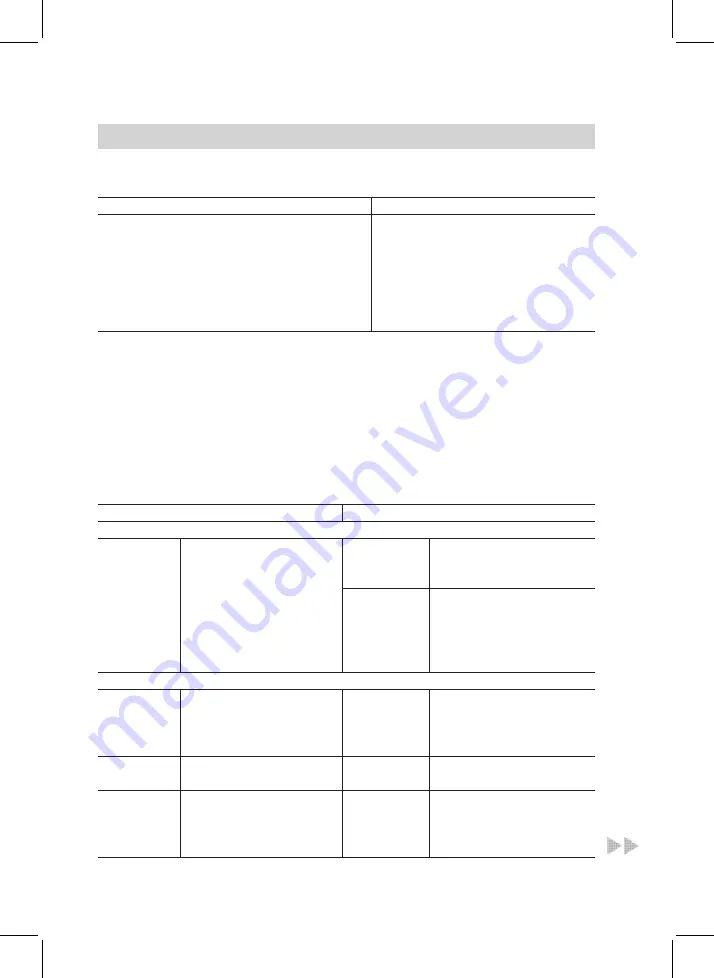
The areas are scanned in the following sequence with
a
/
b
:
Function area
Coding addresses
System design
00
Boiler/burner
06 to 54
DHW
56 to 73
General
76 to 9F
Heating circuit A1 (heating circuit without
mixer)
A0 to Fb
Heating circuit with mixer M2
A0 to Fb
Note
Heating systems with one heating circuit without mixer and one heating circuit
with mixer:
Initially, the possible coding addresses "A0" to "Fb" for the heating circuit with-
out mixer A1 are scanned; then the coding addresses for the heating circuit with
mixer M2 are scanned.
Coding
Coding in the delivered condition
Possible change
System design
00:2
System version 1, 3:
1 heating circuit without
mixer A1, with DHW
heating
00:4
1 heating circuit with
mixer M2, with DHW
heating
00:6
System version 2, 4:
1 heating circuit without
mixer A1 and 1 heating
circuit with mixer M2, with
DHW heating
Boiler/burner
06:...
Maximum limit of the
boiler water tempera-
ture, defaulted in °C by
the boiler coding card
06:20
to
06:127
Maximum limit of the boil-
er water temperature
within the ranges de-
faulted by the boiler
1E:0
Operation with natural
gas
1E:1
Operation with LPG
21:0
No hours run interval for
burner service
21:1
to
21:9999
The number of hours run
before the burner should
be serviced is adjustable
from 1 to 9999 h
Code 2
(cont.)
56
Coding
5592
817
GB
Summary of Contents for VITOPEND 200
Page 12: ...Opening the control unit casing 12 Installation sequence 5592 817 GB...
Page 16: ...Fitting the programming unit into the control unit 16 Installation sequence 5592 817 GB...
Page 17: ...Fitting the front panel 17 Installation sequence 5592 817 GB Installation...
Page 113: ...Connection and wiring diagram internal connections 113 Designs 5592 817 GB Service...
Page 119: ...Parts lists cont 119 Parts lists 5592 817 GB Service...
Page 120: ...Parts lists cont 120 Parts lists 5592 817 GB...
Page 121: ...Parts lists cont 121 Parts lists 5592 817 GB Service...
Page 122: ...Parts lists cont 122 Parts lists 5592 817 GB...
Page 130: ...130 5592 817 GB...
Page 131: ...131 5592 817 GB...