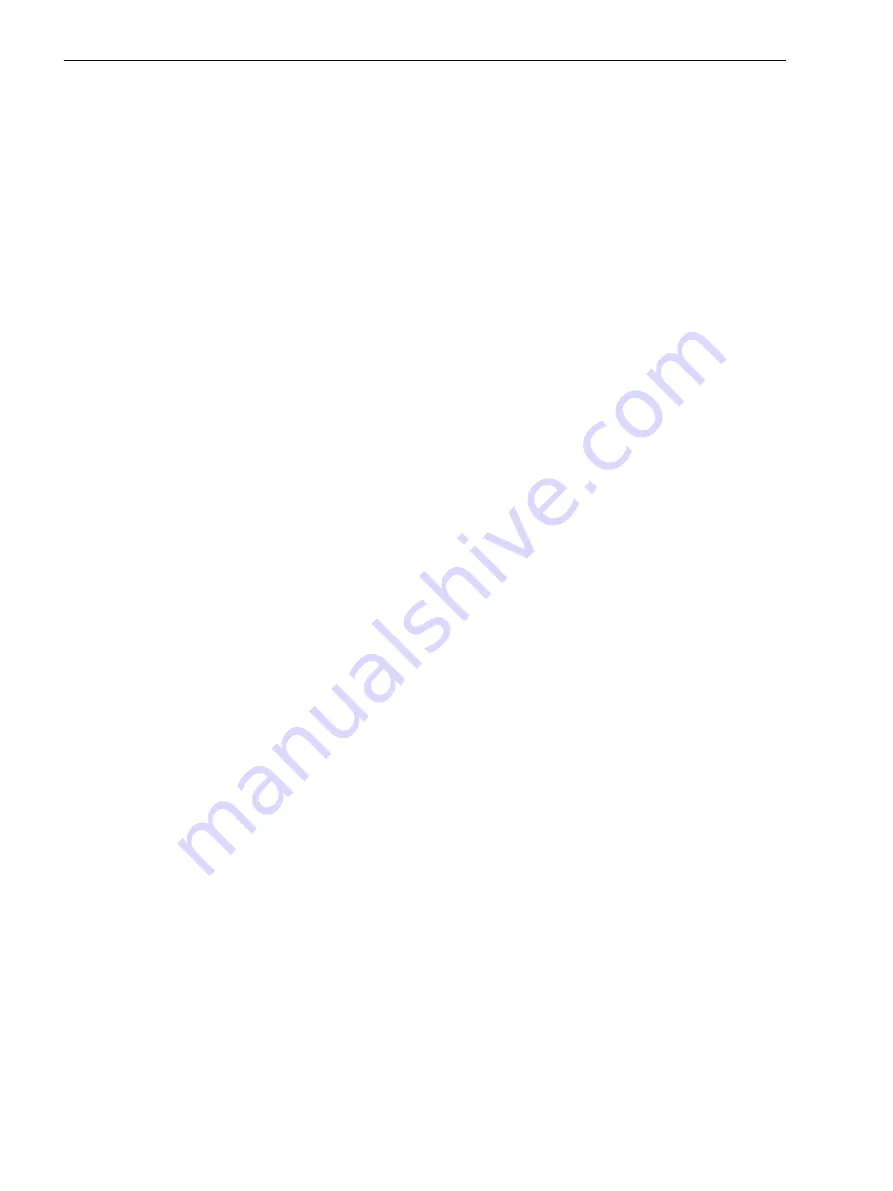
Directional Overcurrent Element 67N-1 (ground)
The pickup value of the 67N-1 overcurrent element(1604
67N-1 PICKUP
)should be set below the minimum
anticipated ground fault current.
If the relay is used to protect transformers or motors with large inrush currents, the inrush restraint feature of
7SJ62/64 may be used for the 67N-1 relay element (
67N-1 PICKUP
) (for more information see margin
heading "Inrush Restraint").
The delay is set at address 1605
67N-1 DELAY
and should be based on system coordination requirements for
directional tripping. For ground currents in a grounded system a separate coordination chart with short time
delay is often used.
The selected time is only an additional time delay and does not include the operating time (measuring time,
dropout time). The delay can be set to ∞. After pickup the element will then not trip. Pickup, however, will be
signaled. If the 67N-1 element is not required at all, the pickup value
67N-1 PICKUP
should be set to ∞. This
setting prevents from tripping and the generation of a pickup message.
Pickup Stabilization (67/67N Directional)
The pickups can also be stabilized via parameterizable dropout times under address 1518
67 T DROP-OUT
or
1618
67N T DROP-OUT
.
Directional Element 67-TOC with IEC or ANSI Curves (phases)
Having set address 115
67/67-TOC
=
TOC IEC
or
TOC ANSI
when configuring the protection functions
(Section
), the parameters for the inverse time characteristics will also be available.
If the relay is used to protect transformers or motors with large inrush currents, the inrush restraint function of
7SJ62/64 may be used for the 67-TOC element (
67-TOC PICKUP
) (for more information see margin heading
"Inrush Restraint").
If the inverse time trip characteristic is selected, it must be noted that a safety factor of about 1.1 has already
been included between the pickup value and the setting value. This means that a pickup will only occur if a
current of about 1.1 times the setting value is present. If Address 1510
67-TOC Drop-out
is set to
Disk
Emulation
, reset will occur in accordance with the reset curve as described in Section
.
The current value is set in address 1507
67-TOC PICKUP
. The setting is mainly determined by the maximum
operating current. Pickup due to overload should never occur, since the device in this operating mode oper-
ates as fault protection with correspondingly short tripping times and not as overload protection.
The corresponding element time multiplication factor for an IEC characteristic is set at address 1508
67 TIME
DIAL
and in address 1509
67 TIME DIAL
for an ANSI characteristic. It must be coordinated with the time
grading of the network.
The time multiplier can also be set to ∞. After pickup the element will then not trip. Pickup, however, will be
signaled. If the 67-TOC element is not required at all, address 115
67/67-TOC
should be set to
Definite
Time
during protective function configuration (see Section
).
If address 115
67/67-TOC
=
TOC IEC
, you can specify the desired IEC–characteristic (
Normal Inverse
,
Very Inverse
,
Extremely Inv.
or
Long Inverse
) in address 1511
67- IEC CURVE
. If address 115
67/67-TOC
=
TOC ANSI
you can specify the desired ANSI–characteristic (
Very Inverse
,
Inverse
,
Short
Inverse
,
Long Inverse
,
Moderately Inv.
,
Extremely Inv.
oder
Definite Inv.
) in address 1512
67- ANSI CURVE
.
Directional Element 67N-TOC with IEC or ANSI Curves (ground)
Having set address 116
67N/67N-TOC
=
TOC IEC
when configuring the protection functions (Section
), the parameters for the inverse time characteristics will also be available. Specify in
address 1611
67N-TOC IEC
the desired IEC characteristic (
Normal Inverse
,
Very Inverse
,
Extremely
Inv.
or
Long Inverse
). If address 116
67N/67N-TOC
was set to
TOC ANSI
, you can select the desired
ANSI characteristic (
Very Inverse
,
Inverse
,
Short Inverse
,
Long Inverse
,
Moderately Inv.
,
Extremely Inv.
or
Definite Inv.
) in address 1612
67N-TOC ANSI
.
Functions
2.3 Directional Overcurrent Protection 67, 67N
102
SIPROTEC 4, 7SJ62/64, Manual
C53000-G1140-C207-8, Edition 08.2016
Summary of Contents for SIPROTEC 4
Page 8: ...8 SIPROTEC 4 7SJ62 64 Manual C53000 G1140 C207 8 Edition 08 2016 ...
Page 18: ...18 SIPROTEC 4 7SJ62 64 Manual C53000 G1140 C207 8 Edition 08 2016 ...
Page 30: ...30 SIPROTEC 4 7SJ62 64 Manual C53000 G1140 C207 8 Edition 08 2016 ...
Page 540: ...540 SIPROTEC 4 7SJ62 64 Manual C53000 G1140 C207 8 Edition 08 2016 ...
Page 594: ...594 SIPROTEC 4 7SJ62 64 Manual C53000 G1140 C207 8 Edition 08 2016 ...
Page 720: ...720 SIPROTEC 4 7SJ62 64 Manual C53000 G1140 C207 8 Edition 08 2016 ...