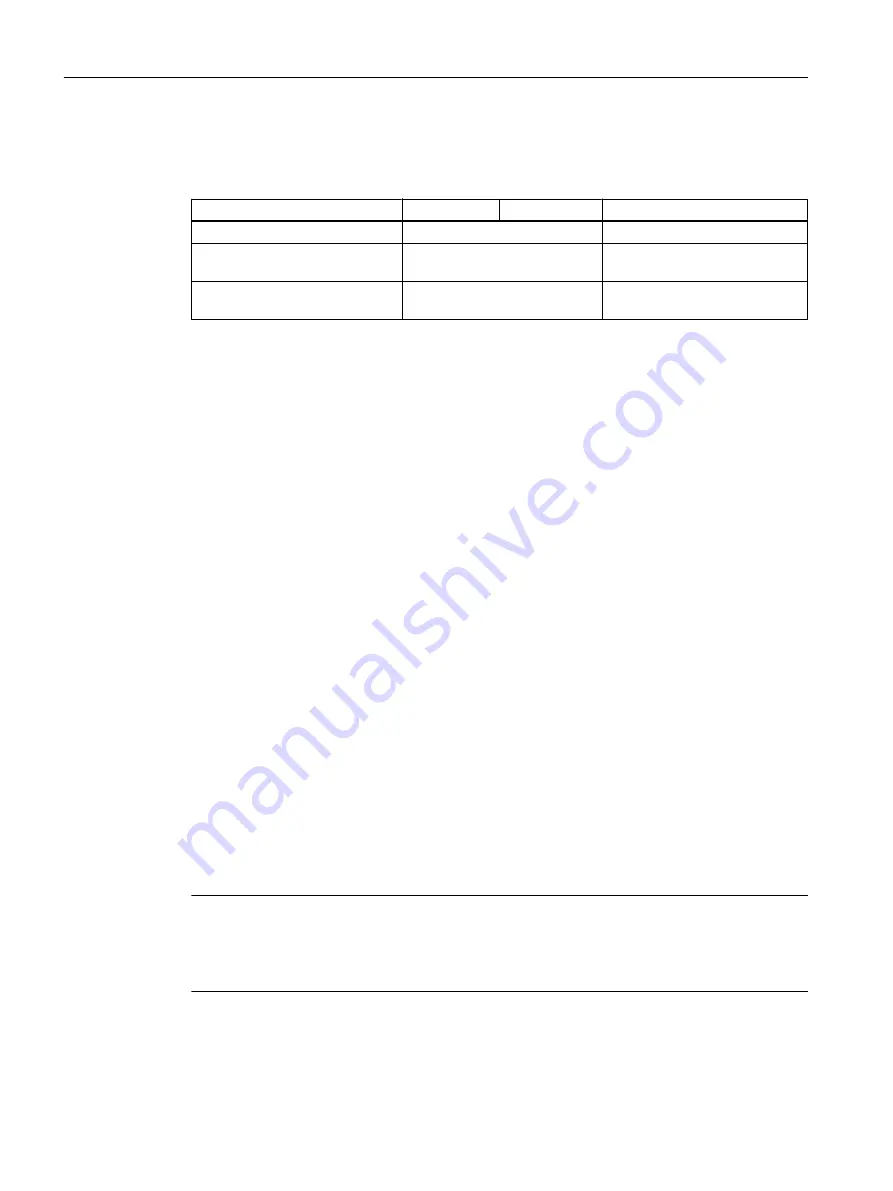
Properties of the Controller, Supervisor and drive units
Table A-2
Properties of the Controller, Supervisor and drive units
Properties
Controller
Supervisor
Drive unit
As bus node
Active
Passive
Send messages
Permitted without external re‐
quest
Only possible on request by the
Controller
Receive messages
Possible without any restrictions Only receive and acknowledge
permitted
Communication types
4 communication types are defined in the PROFIdrive profile:
● Cyclic data exchange via a cyclic data channel
Motion control systems require cyclically updated data in operation for open-loop and
closed-loop control tasks. This data must be sent to the drive units in the form of setpoints
or transmitted from the drive units in the form of actual values, via the communications
system. Transmission of this data is usually time-critical.
● Acyclic data exchange via an acyclic data channel
An acyclic parameter channel for exchanging parameters between the control/supervisor
and drive units is additionally available. Access to this data is not time-critical.
● Alarm channel
Alarms are output on an event-driven basis, and show the occurrence and expiry of error
states.
● Isochronous mode
– Cyclic data exchange in a fixed time grid
– The controller and device are synchronized
Interface IF1 and IF2
The CU320-2 Control Unit can communicate via two different interfaces (IF1 and IF2).
Both interfaces can be allocated the following physical interfaces:
● (1) On-board X126 PROFIBUS/X150 PROFINET
● (2) Communication Board X1400
Note
Ethernet interface X127 is intended for commissioning and diagnostics.
Do not use this interface for other purposes (e.g. field bus communication) and ensure that
X127 (e.g. for service) is always accessible.
Communication
A.1 Communication
Industrial Security
84
Configuration Manual, 08/2017, A5E36912609A