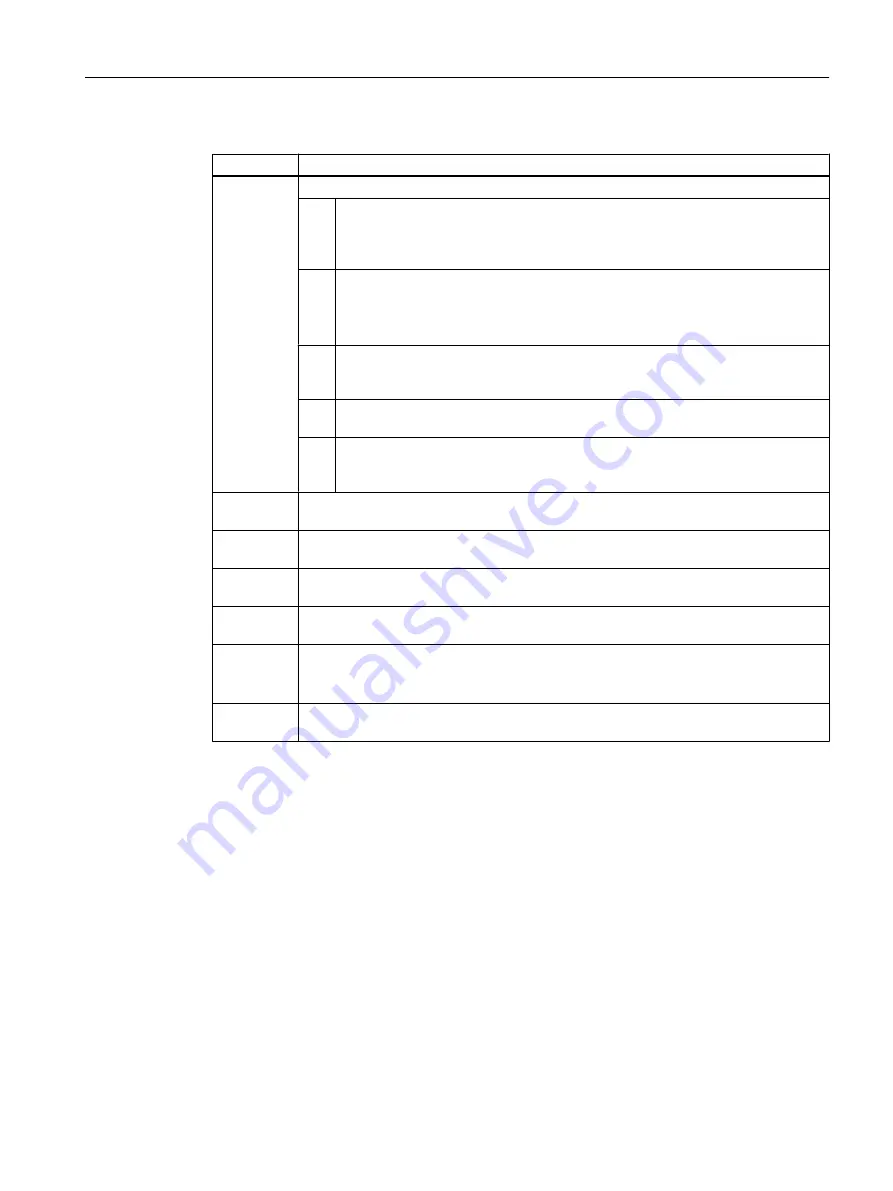
Table 6-36
Extended setup of motorized potentiometer
Parameter
Description
p1030
MOP configuration (factory setting: 00110 bin)
.00
Storage active
= 0: After the motor has been switched on, the setpoint = p1040
= 1: After the motor has switched off, the inverter saves the setpoint. After the
motor has switched on, the setpoint = the stored value
.01
Automatic mode, ramp-function generator active (1-signal via BI: p1041)
= 0: Ramp-up/ramp-down time = 0
= 1: With ramp-function generator
In manual mode (p1041 = 0), the ramp-function generator is always active.
.02
Initial rounding active
1: With initial rounding. Using the initial rounding function it is possible to enter
very small setpoint changes
.03
Storage in NVRAM active
1: If bit 00 = 1, the setpoint is retained during a power failure
.04
Ramp-function generator always active
1: The inverter also calculates the ramp-function generator when the motor is
switched off
p1037
MOP maximum speed (factory setting: 0 rpm)
Automatically pre-assigned when commissioning
p1038
MOP minimum speed (factory setting: 0 rpm)
Automatically pre-assigned when commissioning
p1039
Motorized potentiometer, inversion (factory setting: 0)
Signal source for inverting the minimum speed / velocity or maximum speed / velocity
p1041
Motorized potentiometer, manual/automatic (factory setting: 0)
Signal source for switchover from manual to automatic
p1043
Motorized potentiometer, accept setting value (factory setting: 0)
Signal source for accepting the setting value. The motorized potentiometer accepts the
setting value p1044 on signal change p1043 = 0 → 1.
p1044
MOP setting value (factory setting: 0)
Signal source for the setting value.
For more information about the motorized potentiometer, refer to function diagram 3020 in the
List Manual.
Advanced commissioning
6.16 Setpoints
SINAMICS G120C converter
Operating Instructions, 09/2017, FW V4.7 SP9, A5E34263257B AF
239