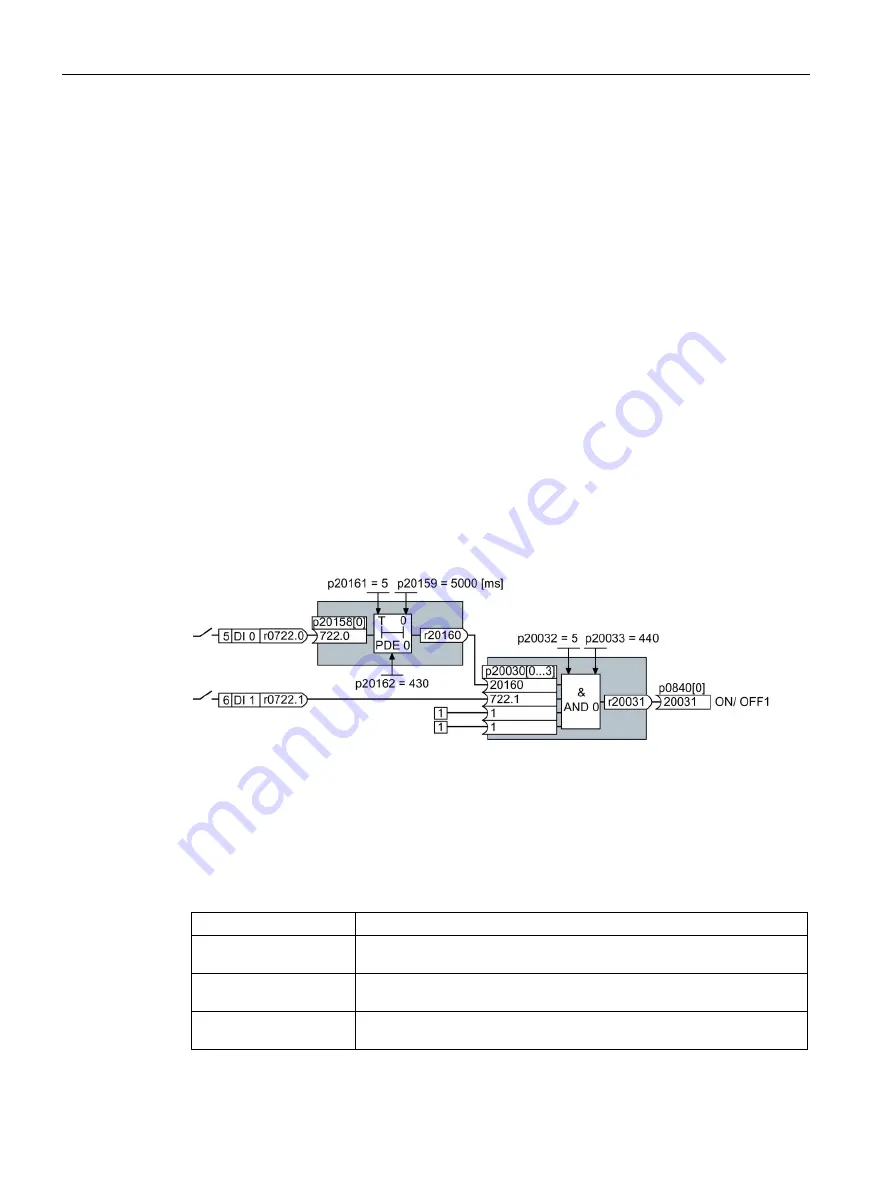
Appendix
A.2 Interconnecting signals in the inverter
Converter with the control units CU240D-2
334
Operating Instructions, 04/2018, FW V4.9 SP10, A5E34262100B AF
Where can you find additional information?
●
This manual suffices for assigning a different meaning to the digital inputs.
●
The parameter list in the List Manual is sufficient for more complex signal
interconnections.
●
The function diagrams in the List Manual provide a complete overview of the factory
setting for the signal interconnections and the setting options.
A.2.2
Application example
Shift the control logic into the inverter
It is only permissible that a conveyor system starts when two signals are present
simultaneously. These could be the following signals, for example:
●
The oil pump is running (the required pressure level is not reached, however, until after 5
seconds)
●
The protective door is closed
To implement this task, you must insert free function blocks between digital input 0 and the
command to switch on the motor (ON/OFF1).
Figure A-4 Signal interconnection for control logic
The signal of digital input 0 (DI 0) is fed through a time block (PDE 0) and is interconnected
with the input of a logic block (AND 0). The signal of digital input 1 (DI 1) is interconnected to
the second input of the logic block. The logic block output issues the ON/OFF1 command to
switch-on the motor.
Setting the control logic
Parameter
Description
p20161 = 5
The time block is enabled by assigning to runtime group 5 (time slice of
128 ms)
p20162 = 430
Run sequence of the time block within runtime group 5 (processing before
the AND logic block)
p20032 = 5
The AND logic block is enabled by assigning to runtime group 5 (time
slice of 128 ms)