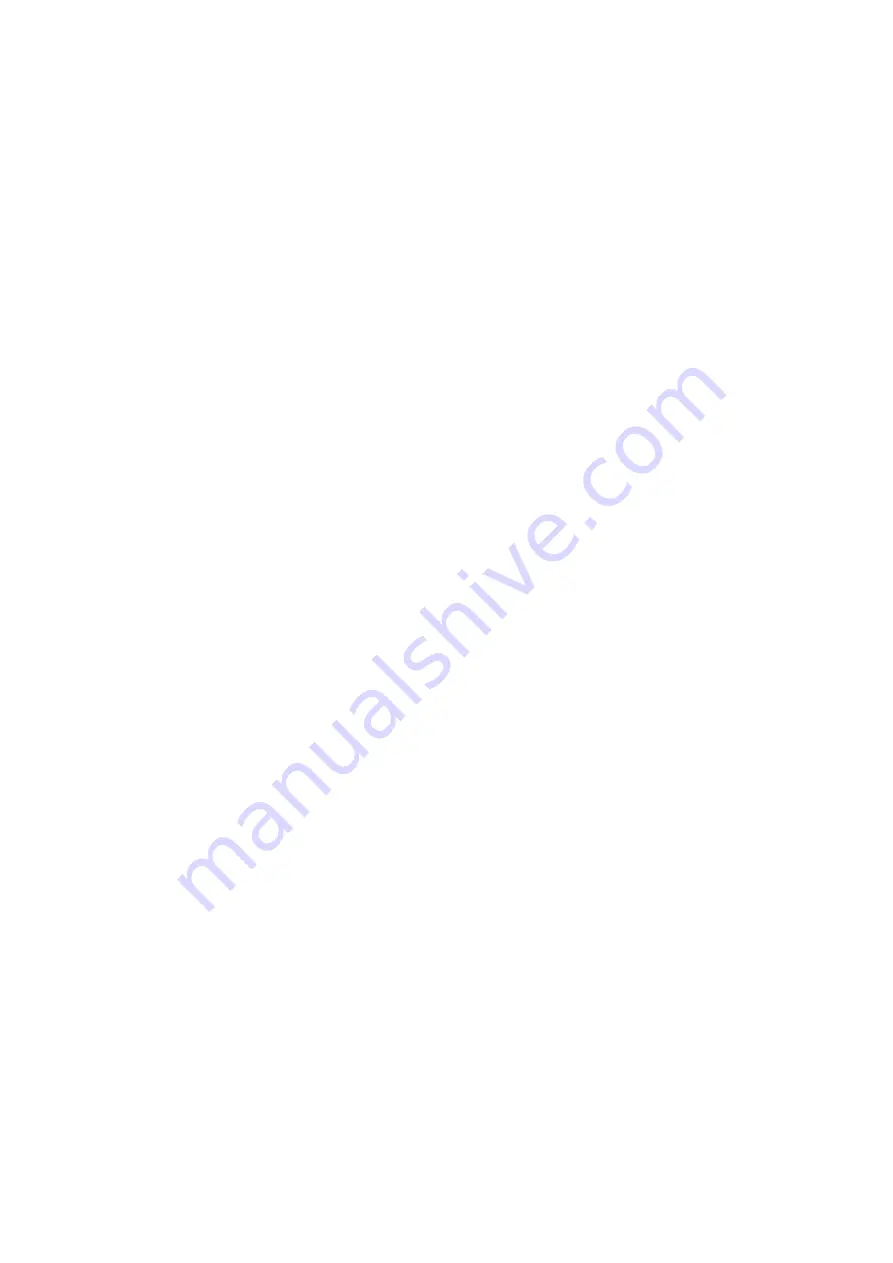
ZEAV-0416A
Measure S/N.(EI MODE and NCI MODE)
EI SAMPLE OFN 1pg/ul (isookutane solvent) 1ul m/z272 S/N
≧
60
NCI SAMPLE OFN 0.1pg/ul(100fg/ul)( isookutane solvent) 1ul
m/z272 S/N
≧
100
Measurement Conditions
INJ
250
M
C
SPLITLESS mode (sampling time 1.0 minute)
COL:
50
M
C (1min) - 40
M
C / min - 200
M
C (0min) - 15
M
C / min - 280
M
C
I/F:
250
M
C
IS:
200
M
C
He:
during injection 250kPa, 1 minute (HIGH-PRESSURE INJECTION mode)
during
analysis
120Kpa
Total flow:
50mL/minute
MS:
SCAN mode (mass range: m/z200 to 300)
interval
0.5s
detector voltage relative value: +0.4
(absolute value: 1.4 to 1.6kV)
measurement time: 3.0 to 10.0 minutes
(solvent elution time: 3 minutes)
Measure S/N.(CI MODE)
Benzophenone 100pg/ul (acetone solvent) 1ul m/z183 S/N
≧
150
Measurement Conditions
INJ
:
250
℃
SPLITLESS MODE (Sampling Time 2.0 min)
COL
:
80
℃(
2min
)−
30
℃/
min
−
260
℃(
5min
)
I
/
F
:
250
℃
IS
:
200
℃
He
:
during injection and analysis
100Kpa
Total flow
20ml/min
MS
:
SCAN
MODE
(
mass range
M/Z
100
〜
250
)
interval
0.5sec
detector voltage
relative value
+0.4
(
absolute
1.4
〜
1.6
kV
)
measurement time
6.0
〜
11.0
min
(
solvent elution time
5.5min
)
Reference pressure of the reagent gas in the installation at the time of corporate identity, NCI use
Methane gas CI 100Kpa
〜
300Kpa
NCI 200Kpa
〜
300Kpa
Isobutane gas CI 20Kpa
〜
80Kpa NCI 40Kpa
〜
80Kpa
Ammonia gas CI 100Kpa
〜
300Kpa NCI 200Kpa
〜
300Kpa
mass patern check Measurements
DI
MODE
Carry out temperature adjustment on the set-up temperature
cholestane 100ng/ul (acetone solvent) 1ul
Measurement Conditions
MS I/F 100
℃
IS 250
℃
DI temperature
room temperature to 300
℃
40
M
C / min
GC temperature constant
Colum flow moderate flow
Summary of Contents for GCMS-QP2010 Series
Page 1: ...1 225 00612A Gas Chromatograph Mass Spectrometer GCMS QP2010 Service Manual...
Page 27: ...27...
Page 71: ...71 Wiring Diagrams 1 Wiring diagram Overall Wiring Diagrams...
Page 72: ...72 Wiring Diagrams 2 Wiring diagram MAIN POWER ASSY...
Page 73: ...73 Unit Operation Checks 3 Wiring diagram Details...
Page 76: ...76 MAIN POWER ASSY Block Diagram Parts inside the broken box are in the MAIN POWER ASSY...
Page 79: ...79 DC POWER A Block Diagram...
Page 84: ...84 MAIN CTRL A Block Diagram...
Page 85: ...85...
Page 90: ...90 IS CTRL A Block Diagram...
Page 94: ...94 HV PCB ASSY block diagram 1 UNNCI case of model EI CI 2 NCI case of model NCI...
Page 98: ...98 IG CTRL A PCB Block Diagram...
Page 109: ...109 DI CTRL A block diagram...
Page 150: ...126 Do not remove the 2 screws on the right side Remove the 2 screws on the left side...
Page 151: ...127 Remove cardboard Move the TW300 left by holding in both hands...
Page 155: ...131 Remove the cap of outlet Loosen the 3 fixing screws and remove the plate Remove the o ring...
Page 160: ...136 Remove the cardboard Completion of TMP mounting...
Page 161: ...137 12 Fix the flange to outlet Place the flange on the outlet Do not forget to place o ring...
Page 163: ...139 Slide fast the IS CTRL A board down and fix it 4 screws Connect the two connectors...
Page 164: ...140 14 Place the covers Place the front cover Place the front door...