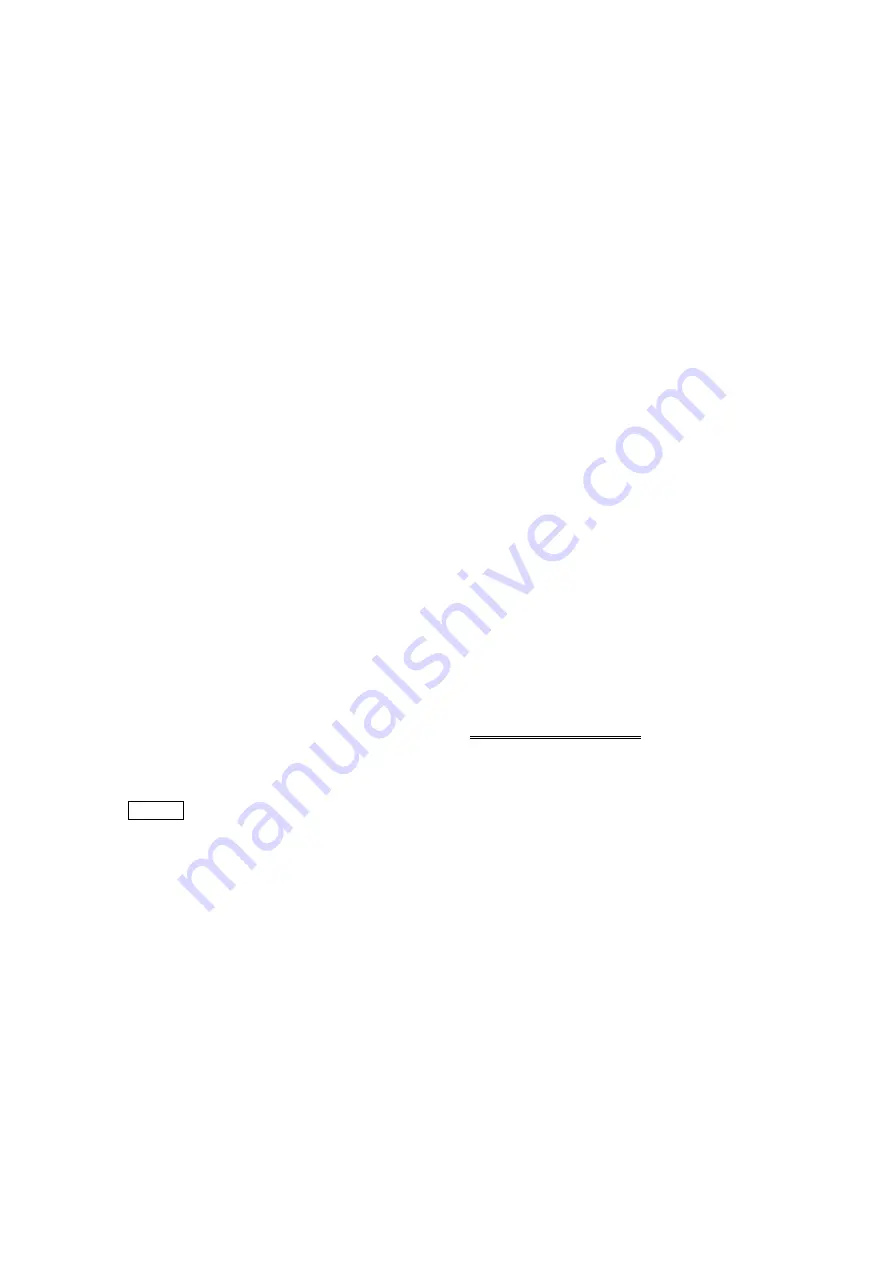
10
Check the following points about the carrier gas connections.
Carrier gas pressure
The operational gas supply pressure to the GC is in the range 300 to 980kPa. But some
supply pressures have a limiting effect on the pressures that can be set at the GC. The
normal supply pressure is 700 to 800kPa.
Carrier gas purity
Leaks from the pipes and organic matter can hinder high-accuracy measurements
(particularly for integrated piping).
Residual air in pipes and air in the analyzer also have an adverse influence on analysis.
Be sure to conduct the following checks when connecting the pipes:
c
Purge the pipes. (Place a piece of paper over the end of pipes and check that no color is
visible.)
d
Sniff the gas to check it has no bad smell.
e
Purge the GC connector for several minutes.
f
Set the GC total flowrate to maximum and leave for 10 to 20 minutes.
Mounting the column
Mount the column, as described in section
3.2 Preparation for Analysis
of the Operation
Guide.
Caution
Minute traces of interfering components appear easily in the analysis results due to the high
sensitivity of the instrument.
Never touch the septum or glass insert at the inlet with bare hands.
When mounting the column, wipe all parts with acetone before inserting them.
Installation
All required software is preinstalled in the PC set but, unless the latest software versions are
installed, the software must be upgraded to the latest version.
Refer to applicable Technical Information for details about how to obtain the latest software
and the method of installation.
Summary of Contents for GCMS-QP2010 Series
Page 1: ...1 225 00612A Gas Chromatograph Mass Spectrometer GCMS QP2010 Service Manual...
Page 27: ...27...
Page 71: ...71 Wiring Diagrams 1 Wiring diagram Overall Wiring Diagrams...
Page 72: ...72 Wiring Diagrams 2 Wiring diagram MAIN POWER ASSY...
Page 73: ...73 Unit Operation Checks 3 Wiring diagram Details...
Page 76: ...76 MAIN POWER ASSY Block Diagram Parts inside the broken box are in the MAIN POWER ASSY...
Page 79: ...79 DC POWER A Block Diagram...
Page 84: ...84 MAIN CTRL A Block Diagram...
Page 85: ...85...
Page 90: ...90 IS CTRL A Block Diagram...
Page 94: ...94 HV PCB ASSY block diagram 1 UNNCI case of model EI CI 2 NCI case of model NCI...
Page 98: ...98 IG CTRL A PCB Block Diagram...
Page 109: ...109 DI CTRL A block diagram...
Page 150: ...126 Do not remove the 2 screws on the right side Remove the 2 screws on the left side...
Page 151: ...127 Remove cardboard Move the TW300 left by holding in both hands...
Page 155: ...131 Remove the cap of outlet Loosen the 3 fixing screws and remove the plate Remove the o ring...
Page 160: ...136 Remove the cardboard Completion of TMP mounting...
Page 161: ...137 12 Fix the flange to outlet Place the flange on the outlet Do not forget to place o ring...
Page 163: ...139 Slide fast the IS CTRL A board down and fix it 4 screws Connect the two connectors...
Page 164: ...140 14 Place the covers Place the front cover Place the front door...