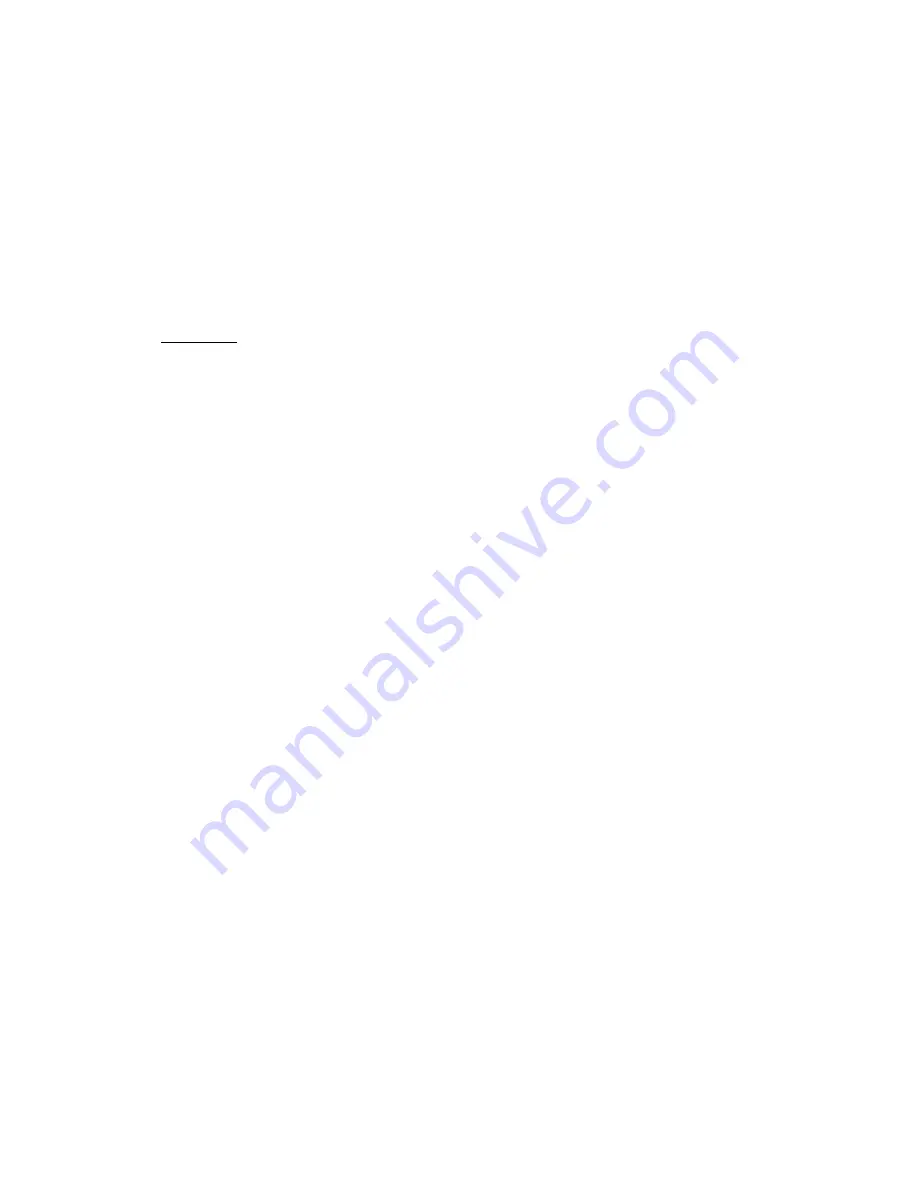
There are many other variations on this (changing slicers for example).
Learn how to diagnose problems. This requires careful observation (#6). Once you've
identified where the problem occurs (let's say getting the first layer to stick) then PRACTICE that
piece (see #3) until you sort it out. No need to run through the entire process over and over.
Isolate the problem, formulate a hypothesis on what you think might be happening and design a
test to prove or disprove your hypothesis. If you see a problem and can't formulate a hypothesis
THEN seek help! Or, pre-test your hypothesis here to get some experienced feedback. But,
whatever you do, try to work through the diagnostic process yourself first, that's how you learn.
Footnote:
Many years ago (20) my company had an annual laboratory safety week (I
worked in a corporate R&D lab with lots of nasty stuff). One of the annual favorites was a
gentleman from OSHA who talked about electrical safety. He started his presentation with a
black and white video from the 1940s (I think) of a speaker walking up to a microphone on
stage. The presentation was being filmed. The speaker reached up and grabbed the mic and
was immediately thrown back and fell to the stage unconscious. Members of the audience
rushed up to help him. This was all on video. As 4 or 5 people worked to help the victim, you
see a gentleman casually walk up to the mic, reach out his hand and touch the mic. He was
immediately thrown back and collapsed on the stage next to victim #1. Literally 30 seconds later
a THIRD audience member walked up to the mic (now there are 2 victims on the stage and a
hoard of people working to revive them) and
carefully
reached out his finger (looked like the
scene from ET) and very, very gently touched the mic with just the tip of his finger. He was
immediately thrown to the stage as the third victim. All of this was caught on video. No one died
(we were told). Neither of the second two victims stopped to think about the problem,
consequences or solutions.
#12 Be a Fanboy.
I am probably going to lose some fans for this post about cooling fans!
Don't think of a part cooling fan as an object. Instead, think about "air flow". If you need
cooling on a PLA (or other material) part, then you need to understand air flow. Not all cooling
fans are created equally. Consider this, some folks use a 40mm, some a 25mm, some (like me)
a 25mm squirrel cage fan. Some are mounted to blow the full fan width stream at the nozzle
area, some have a duct or some (like mine) have a very focused soda straw duct). So
comments like "run your fan at 1/2 speed" are not specific enough to be useful information.
Instead, you need to understand how your particular fan, it's arrangement, your material, etc, all
relate to the air flow.
Firstly, using the previous strategies, try to minimize or eliminate the need for any sort of
air cooling. Slowing a print down (#5) is one great way to do this. It also gives you a chance to
see (#6) where any problem areas on a print might be. You can use this information to focus the
right amount
of air flow on the problematic areas. The tendency for many is to use as much air
as possible. It is much better, more consistent, and more reliable to use as little air flow as
necessary. This puts less thermal stress on the printed part.
101