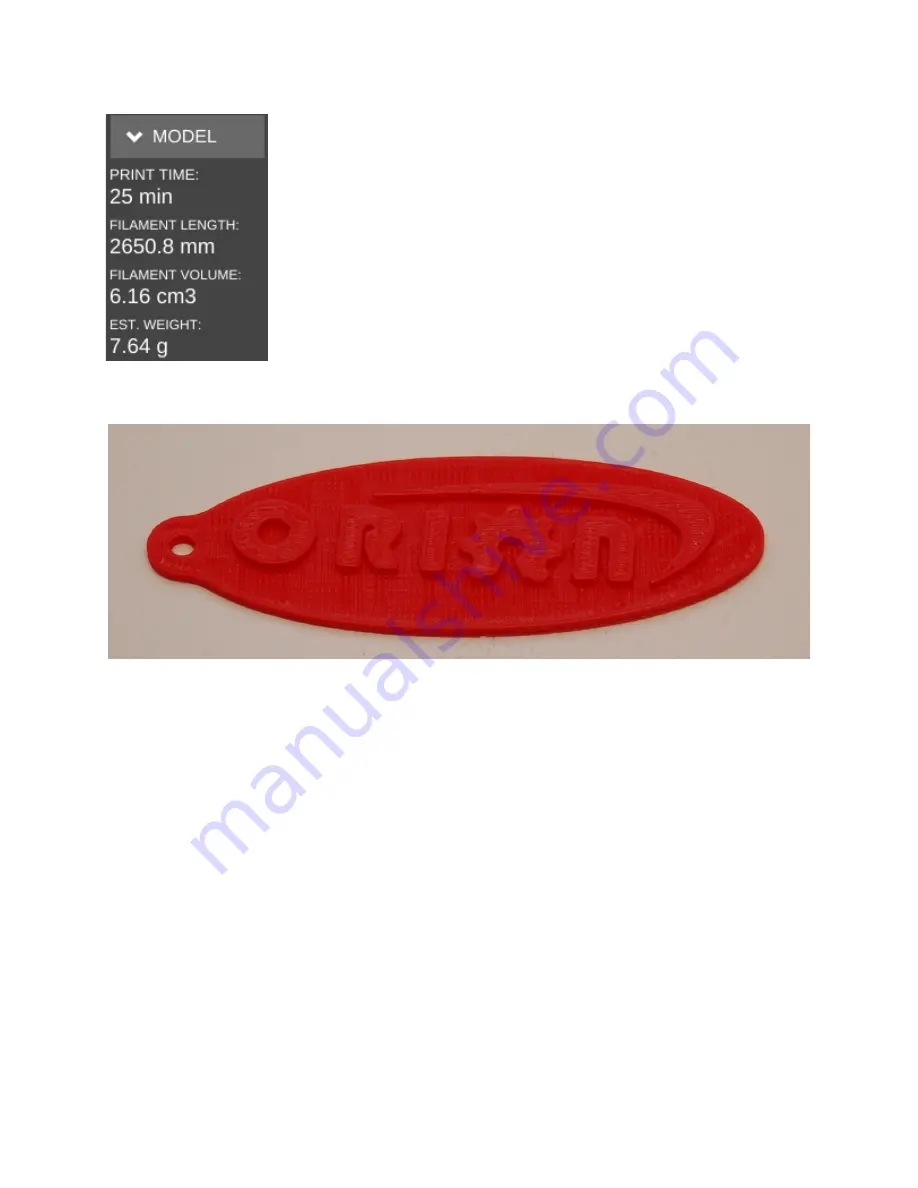
After slicing the object, MatterControl will display a few statistics
about the current print in the Layer View window. This can be handy
information if you're selling your services and need to know how much a
particular part is going to consume in both time and materials.
Go ahead and click the
button and get your object printing!
After the print finishes, you should have a little part that looks something like the photo
below (if that's what you printed).
66