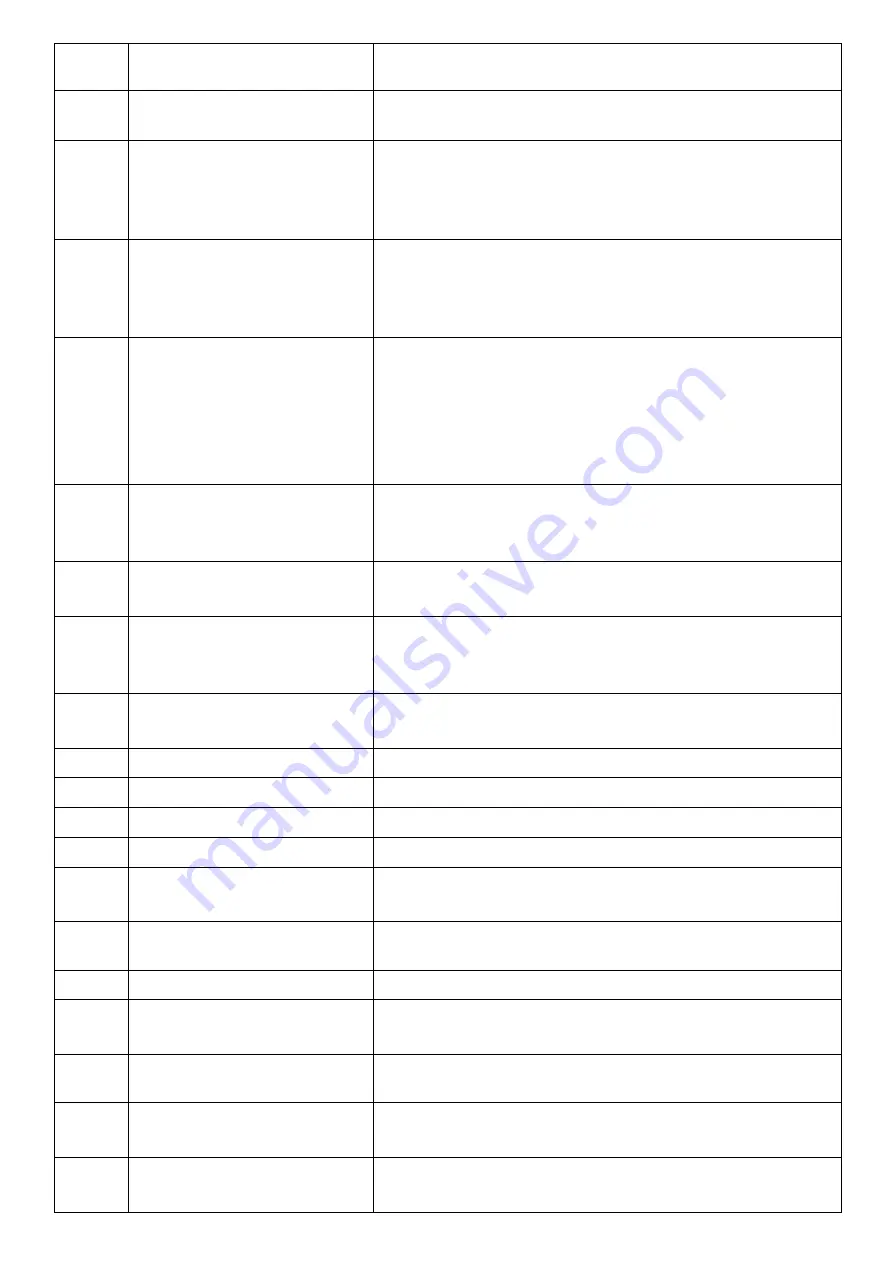
78
Setting
value
Function
Description
17
Acceleration / deceleration time
selection terminal 2
acceleration and deceleration time are selected. See Table 2 for
details.
18
Frequency source switching
According to the setting of the frequency source selection
parameter (00-17), when switching between two frequency
sources is set as the frequency source, the terminal is used to
switch between the two frequency sources.
19
UP/DOWN set to clear (terminal,
keyboard)
When the frequency is given as digital timing, this terminal can
clear the frequency value changed by terminal UP/DOWN or
keyboard UP/DOWN, so that the given frequency is restored to
the value set by 00-06.
20
Run command switching
terminal
When the command source is terminal control (00-00=1), this
terminal can switch between terminal control and keyboard
control.
When the command source is communication control (00-00=2),
this terminal can switch between communication control and
keyboard control.
21
Acceleration / deceleration
prohibited
Ensure that the inverter is not affected by external signals
(except the stop command) and maintain the current output
frequency.
22
PID Pause
The PID is temporarily disabled, and the inverter maintains the
current output frequency.
23
PLC status reset
The PLC pauses during execution, and when running again, you
can use this terminal to restore the inverter to the initial state of
the simple PLC.
24
Wobble frequency pause
The inverter outputs at the center frequency. The wobble
frequency function is suspended.
25
Counter Input
Count pulse input terminal.
26
Counter reset
Clear the counter status.
27
Length counter input
Input terminal for length counting.
28
Length reset
Length clear
29
Torque control prohibited
The inverter is prohibited from torque control, the inverter enters
the speed control mode
30
PULSE (pulse) frequency input
(only valid for MI5)
MI5 functions as a pulse input terminal.
31
Reserved
Reserved
32
Immediate DC braking
When this terminal is valid, the inverter directly switches to the
DC braking state
33
Normally closed input for
external fault
When this signal is valid, the inverter reports fault EF and stops.
34
Frequency modification enable
When this function is valid, the inverter does not respond to
changes in frequency commands.
35
PID action direction is reversed
When this terminal is valid, the direction of PID action is reversed
to the direction set in 10-03.
Summary of Contents for S3100E Series
Page 1: ...S3100Eseries inverter General vector control PM User manual User manual ...
Page 24: ...20 Size 5 Unit mm S3100E 4T45G 55P 4T110G Size 6 Unit mm S3100E 4T110G 132P 4T160G 185P ...
Page 25: ...21 Size 7 Unit mm S3100E 4T185G 200P 4T220G Size 8 Unit mm S3100E 4T220G 250P 4T315G ...
Page 26: ...22 Size 9 Unit mm S3100E 4T315G 355P 4T400G 450P Size 10 Unit mm S3100E 4T450G 500P 4T500G ...