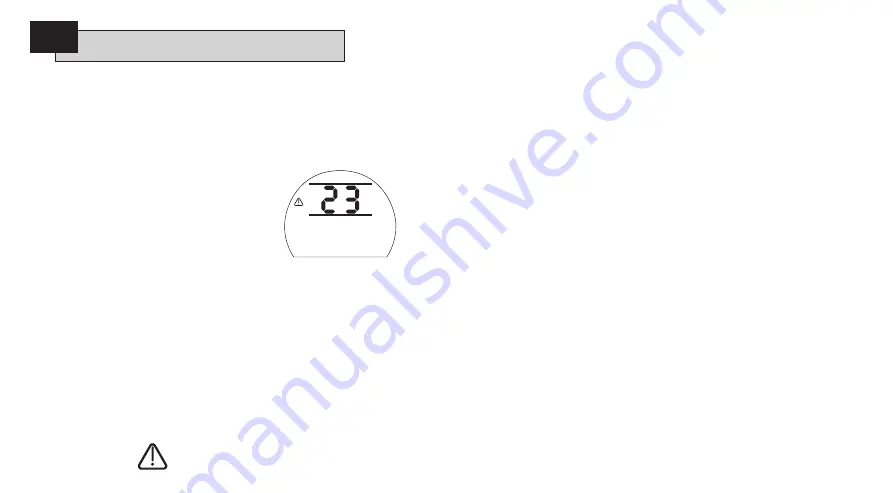
6
•
Local Close
Local close signal applied.
•
Local Open
Local open signal applied.
•
Remote Close
Remote close (hardwired
or analogue) signal applied.
•
Remote Open
Remote open (hardwired
or analogue) signal applied.
•
Remote ESD
Remote hardwired
emergency shut down signal applied.
•
Remote Bus Open
Remote Bus * open
signal applied.
•
Remote Bus Close
Remote Bus* close
signal applied.
•
Remote Bus ESD
Remote Bus*
emergency shut down signal applied.
•
BT Connected
The actuator is connected
via
Bluetooth
to either a setting tool
or PC.
*
Bus Control option fitted may be Pakscan,
Profibus, Modbus, DeviceNet or Foundation
Fieldbus. Refer to actuator wiring diagram.
3.5 Display Alarm Indication
The EH display provides alarm indication
in the form of text and alarm icons.
General Alarm:
The general alarm icon will be
supported with text in the bottom line
indicating the particular alarm, or if
more than one is present, each alarm
will be displayed in sequence.
Fig 3.8 shows the status example
MID
TRAVEL OP
(Mid Travel Over Pressure).
Fig. 3.8
Available alarm conditions displayed:
Valve Alarms
•
OP IN MID POS
- Tripped off on pressure
while moving in either direction between
electrical limits after a signal to move.
•
OP AT LIMIT
- Tripped off on pressure
while moving in either direction between
the electrical limit and the mechanical
end stop after a signal to move.
•
STALL IN MID POS
- No movement
detected between electrical limits after a
signal to move.
•
STALL AT LIMIT
- No movement detected
between the electrical limit and the
mechanical end stop after a signal to
move.
Control Alarms
•
DEMAND FAULT
- This fault indicates
that the analogue demand signal has
dropped below half the minimum set
demand signal. In a 4-20 mA system the
demand signal has dropped below 2
mA, or it goes above 22mA.
•
PS UNABLE TO RUN
- The actuator may
not be at the correct limit to start the
test or a new command was issued
before the test was complete.
•
MANUAL RESET ON
- The actuator needs
to be manually reset after either a ESD
command or mains failure.
Refer to 9.5
ESD Manual Reset.
•
ESD ACTIVE
- When present the ESD
signal overrides all local and remote
control signals. Once the ESD action is
carried out operation is inhibited while
the ESD signal is maintained.
Refer to
9.5 ESD Action.
Actuator Alarms
•
CONFIG ERROR
- There may be an error
in the configuration (set up) of the
actuator. Check and reset basic setting
and check configuration settings.
•
ELECTRONIC FAULT
- A hardware fault is
caused by an internal fault on the Main
PCBA which prevents it from reading
its inputs. This is critical and inhibits
operation. This fault may be cleared by
removing the mains power from the
actuator and waiting for 20 seconds.
•
LOCAL CONTROL FAIL
- This indicates a
fault caused by a either a Main Board
failure, local control switch failure or
conflicting signals from the switches.
For example, both Local and Remote or
Open and Close selected simultaneously.
•
SOL DRIVE FAULT
- Contact Rotork.
•
POS SENSOR FAULT
- Detected failure in
the position sensing system – contact
Rotork.
•
PRES SENSE FAULT
- Detected failure in
the pressure sensing system – contact
Rotork.
•
WRONG DIRECTION
- This indicates
that the actuator has started to move
in the opposite direction to the given
command. When this occurs the
actuator is stopped.
•
PS ERROR
- This indicates that a fault
occurred while the actuator was
attempting a partial stroke.
•
OPTION CH 1 FAULT
- Contact Rotork.
•
OPTION CH 2 FAULT
- Contact Rotork.
•
EEPROM MISSING
- Contact Rotork.
Operating your EH Actuator
continued
Stopped
MID TRAVEL OP
3