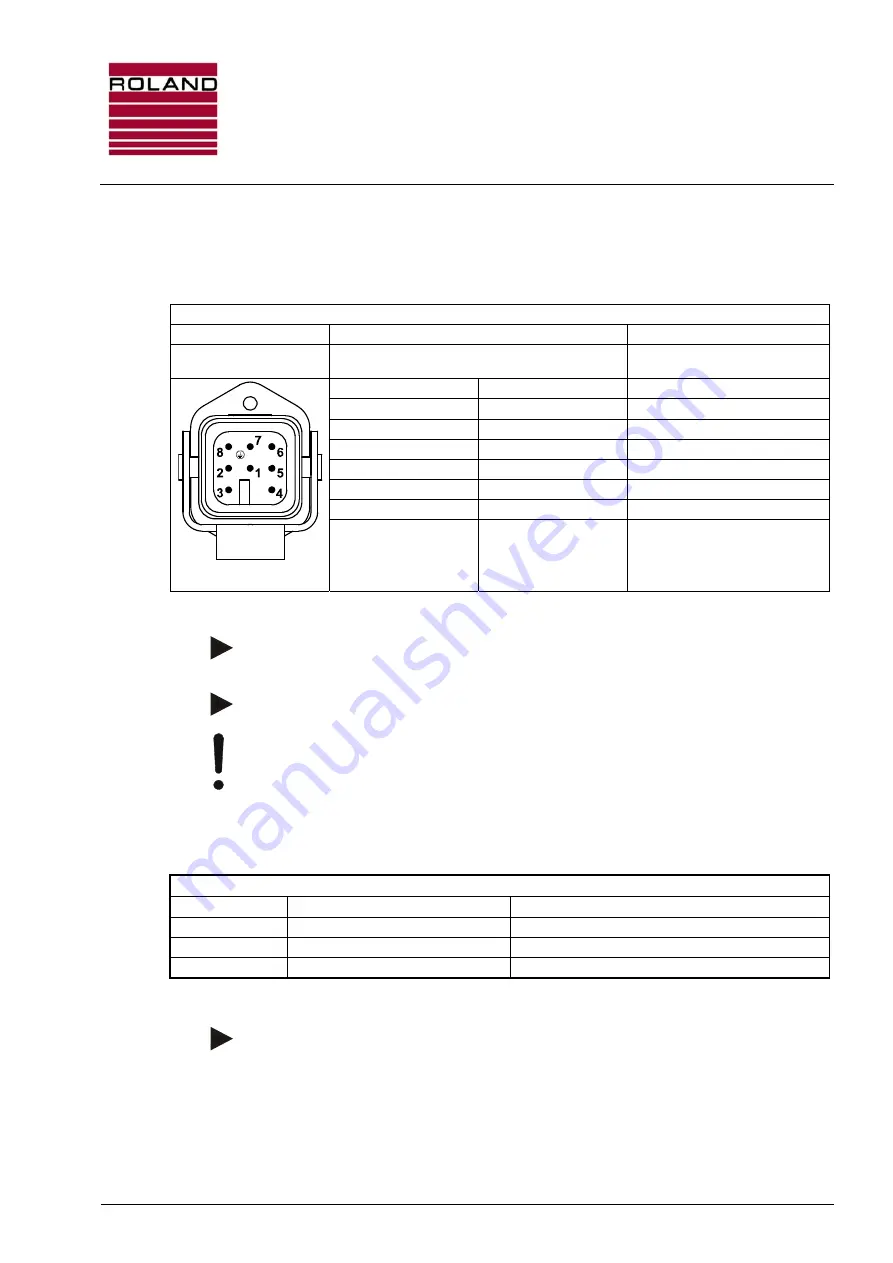
Manual
Double Sheet Control System R1000 series L20
with integrated fieldbus interface
B0063191 / 1.3
Electrical installation
ROLAND ELECTRONIC GmbH · Otto-Maurer-Str. 17 · DE 75210 Keltern · Phone +49 (0)7236-9392-0 · Fax +49 (0)7236-9392-33
27
5.2.3 Supply voltage connection and Optocoupler inputs (Connection X1)
Here, the supply voltage is connected, as well as the optocoupler inputs.
Allocation of power supply connection
Connector at control unit
Input
Suppliers / types / notes
Voltage supply
Enclosure HAN 3A, EMI-type, metrical
7-pin insert and PE, Pin contacts at control unit
Harting and others
view onto contacts
Pin1 +24VDC
Pin 2
GND
Pin 3
IN0 +
1st Opto coupler input +
Pin 4
IN1 +
2nd Opto coupler input +
Pin 5
IN2 +
3rd Opto coupler input +
Pin 6
PLC GND
Voltage supply PLC GND
Pin 7
PLC +24VDC
Voltage supply PLC +24VDC
Pin 8
Shield / ground
Internal at enclosure (ground)
A corresponding cable plug (/contacts) is part of the standard scope of supply.
Note
Pin 6 is connected with pin 7 of connection X2.
Pin 7 is connected with pin 1 of connection X2.
Note
The cable for the voltage supply should be kept as short as
possible.
Attention
Pin 1 (+24 VDC) must not be connected with operation earth.
Optocoupler inputs for fast measurements
For real-time measurements it is possible to start measurement with external optocoupler inputs.
The optocoupler function with a control voltage of 20 to 28 VDC. For connections see table on
page 40 "Pin configuration of voltage supply connection".
Allocation of optocoupler inputs
Signal Meaning
Note
IN0
External measurement start 1
1st optocoupler input
IN1
External measurement start 2
2nd optocoupler input
IN2
External measurement start 3
3rd optocoupler input
The combination of measurement start 1, 2 and 3 can be adjusted in the system configuration
menu.
Note
“Measurement start” signals can be issued either via the process channel
or via an opto coupler. Simultaneous measurement start” signals result in
fault messages.