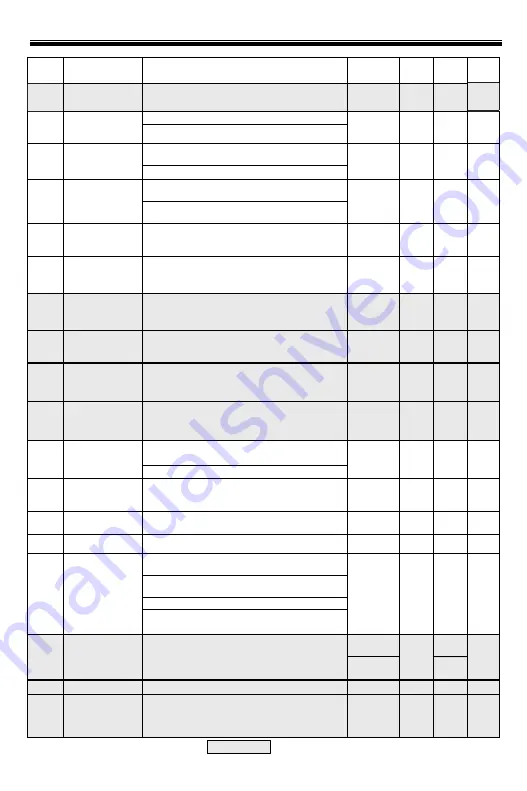
~
LIST OF FUNCTION CODE SETTING~
- 29 -
Function
Name
Descriptions
Range of
setting
Resolu-
tion
Factory
setting
No. page
reference
for detail
F_064
Gain of the
automatic
torque boost
According to the load condition, adjust the
output voltage of the certain V/F pattern
0.0~25.5 0.1
1.0
59
0:There is no output for overload detection
F_065
Selection of
overload
detection(OLO)
1:There is output for overload detection (Re.6)
0,1
—
0
60
0:There is output for the condition of constant
frequency only
F_066
Status of
overload
detection(OLO)
1:There is output for any frequency
0,1
—
0
60
0:Inverter is still running after overload has
been detected
F_067
Output setting
for
overload(OLO)
1:Output of inverter is inhibited after overload
has been detected
0,1
—
0
60
F_068
Level of
overload
setting(OLO)
The setting of level of current for overload
detection
30%~200%
by the inverter
rated current
1%
160 60
F_069
Time interval
for overload
detection
The time interval, in which the output current
is larger than the setting of F_068, required for
overload detection
0.1~10.0 0.1S
0.1
60
F_070
Level of stall
prevention
during
acceleration
If stall is occurred during acceleration, motor is
kept at constant speed
30%~200%
rated current
1%
170 61
F_071
Level of stall
prevention at the
constant speed
If stall is occurred at the constant-speed
running, the motor speed is decreased
30%~200%
rated current
1% 160 61
F_072
Acceleration time
of recovery after
stall prevention at
the constant speed
Setting of acceleration time of recovery after
stall prevention at the constant speed
0.1~3200.0
0.1S
61
F_073
Deceleration time
of recovery after
stall prevention at
the constant speed
Setting of deceleration time of recovery after
stall prevention at the constant speed
0.1S 15.0 61
0:There is no stall prevention during
deceleration
F_074
Select function of
stall prevention
during dec.
1:There is stall prevention during deceleration
0,1
—
1
61
F_075
Current of DC
braking
Setting of level of current for DC braking
setting
0~150%
by the inverter
rated current
1%
50
62
F_076
Time interval of DC
braking in stop
In stop the required time interval for DC
braking setting
0.0~20.0 0.1S 0.5
62
F_077
Time interval of DC
braking in start
In start the required time interval for DC
braking setting
0.0~20.0 0.1S 0.0
62
0:Inverter can not be restarted after
instantaneous power interruption
1:Inverter will be restarted after instantaneous
power interruption
2:Shutdown
F_078 Selection of
resumption
3:Enable controlled deceleration stop
(F_103,F_104,F_105,F_106)
0~3
—
0
63
150.0~192.0
175.0
(Re.3)
F_079
Level of power
source for
shutdown
Level of power source for shutdown
300.0~384.0
0.1V
320.0
(Re.4)
63
F_080
Number of restart Number of restart for fault conditions
0~16
1
0
67
F_081
Carry
frequency
setting
The setting value is higher then the noise is
lower.
The carry frequency is inversely proportional
to the distance between inverter and motor
1~6
—
4
(Re.10)
67
The color as means which can be set during operation
.
0.1~3200.0
(Re.5)
15.0
(Re.5)
by the inverter
by the inverter