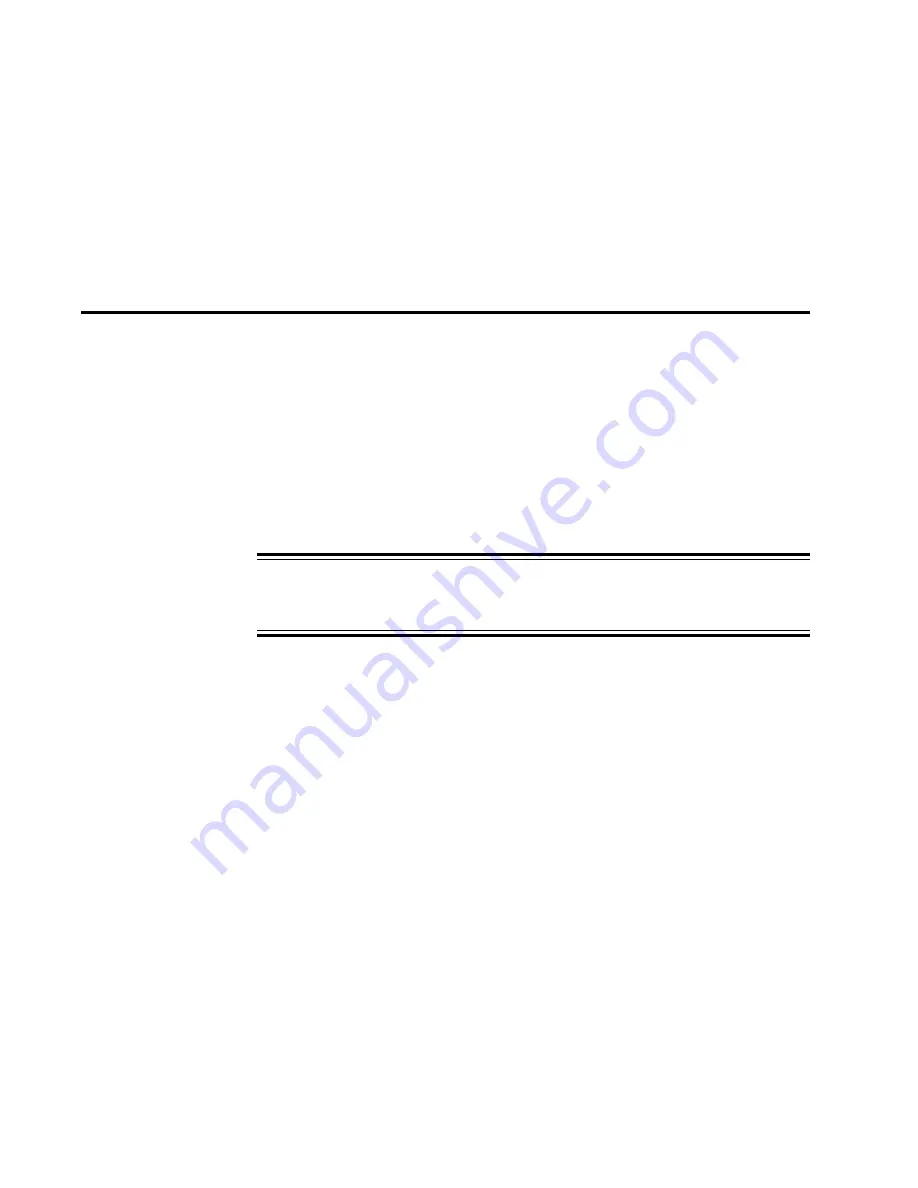
50
TQ10X User Guide
Integral gain can remove steady state errors that are due to gravity or a constant
static torque. Integral gain can also correct velocity lag that can occur in a constant
velocity system.
If error persists during a move, the sum of the error values may be quite high at the
end of the move. In this case, the torque commanded by the integral gain can also
be very high, and cause overshoot. This effect is called integral windup. Integral
windup can sometimes cause very aggressive motion, you may want to limit this
effect. CIL sets an upper limit on the integral, which in turn limits the integral term
(Integral * CIG).
Tuning the System
In the procedure given below, you will systematically vary the tuning parameters
until you achieve a move that meets your requirements for accuracy and response
time.
Special Considerations when Tuning with SM or NeoMetric Motors
If you use a high performance motor (peak current rating greater than three times
the continuous current rating), be careful not to overheat the motor while tuning
your system. If you accidentally choose tuning gains that cause motor instability,
excess motor current can quickly overheat and damage the motor—even before the
thermostat can trigger the motor overtemperatu re circuit.
CAUTION
For initial tuning with an SM or NeoMetric motor, set peak current DIP switches at twice the
motor’s continuous rated current, or less. Otherwise, high peak currents during instability
may cause motor overheating and damage.
To avoid damage, we recommend a tuning procedure that may differ from methods
you have used before. Instability sometimes does occur during tuning; to avoid the
damaging currents that instability can cause, reduce the peak current before you
begin the tuning process. Then, as you refine your tuning values, you can gradually
increase peak current. These steps are included in the tuning procedure described
below.
Preparing the System for Tuning
Before applying power and tuning the drive, complete the following steps.
Setup Procedure:
➀
Heatsink your motor: This is especially important in temporary “bench top”
procedures. SM and NeoMetric Motors dissipate excess heat through their faceplate;
to ensure proper motor cooling, the faceplate must be mounted to a heatsink.
➁
Reduce peak current: Using the drive's DIP switches, set the peak current at a level
that is less than twice the motor’s continuous current rating.
•
4.4 amps for SM motors with
-A
windings
•
7.4 amps for SM motors with
-B
windings
•
6.0 amps for N0701D and N0702E motors
•
8.9 amps for N0702F motor
This helps protect SM and NeoMetric motors from overheating when you begin
tuning the drive.
Artisan Technology Group - Quality Instrumentation ... Guaranteed | (888) 88-SOURCE | www.artisantg.com