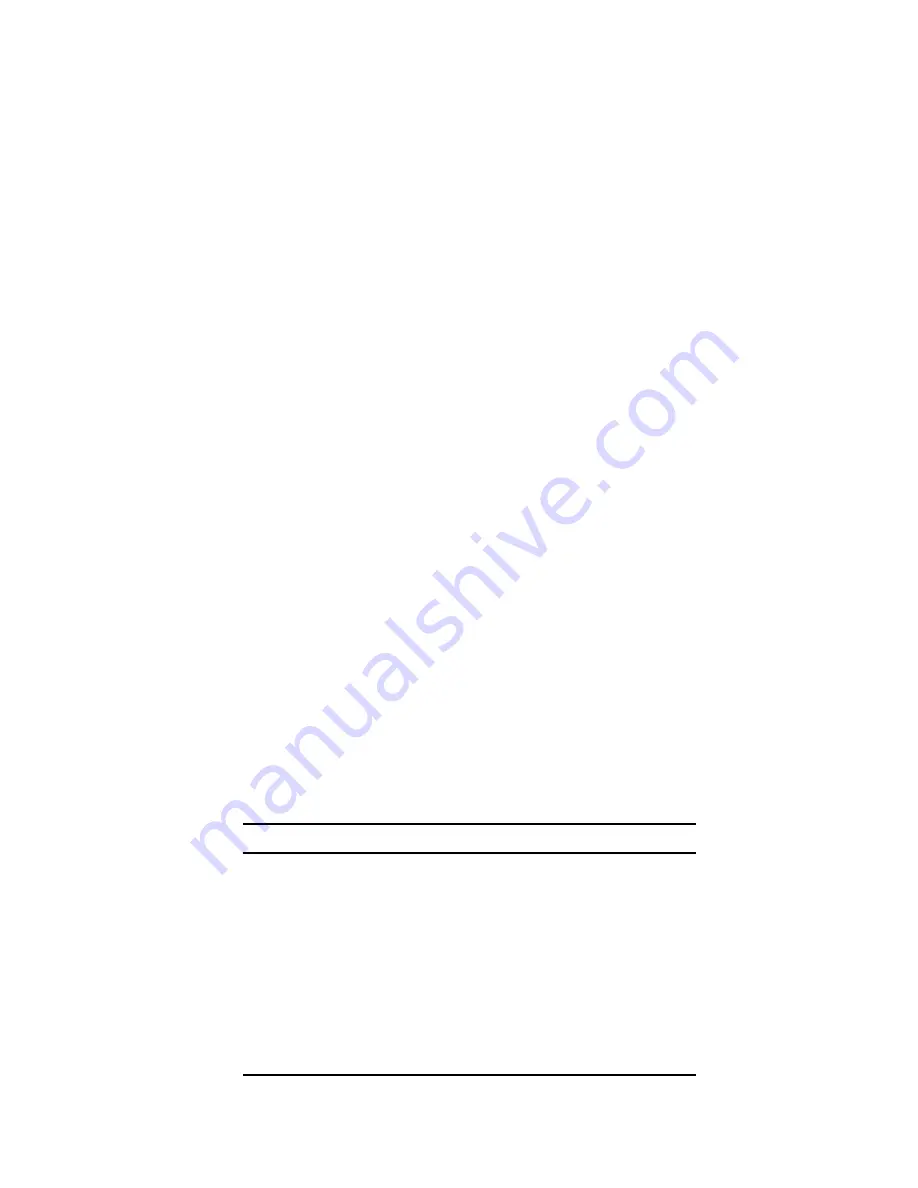
➅
Troubleshooting
105
6
Troubleshooting
IN THIS CHAPTER
•
Diagnostic LEDs
•
RS-232C Problems
•
Software Debugging Tips
•
Encoder Problems
•
Homing Diagrams
•
Non-Drive Related Problems
•
Protective Circuits
•
Product Return Procedure
C H A P T E R S I X
Artisan Technology Group - Quality Instrumentation ... Guaranteed | (888) 88-SOURCE | www.artisantg.com