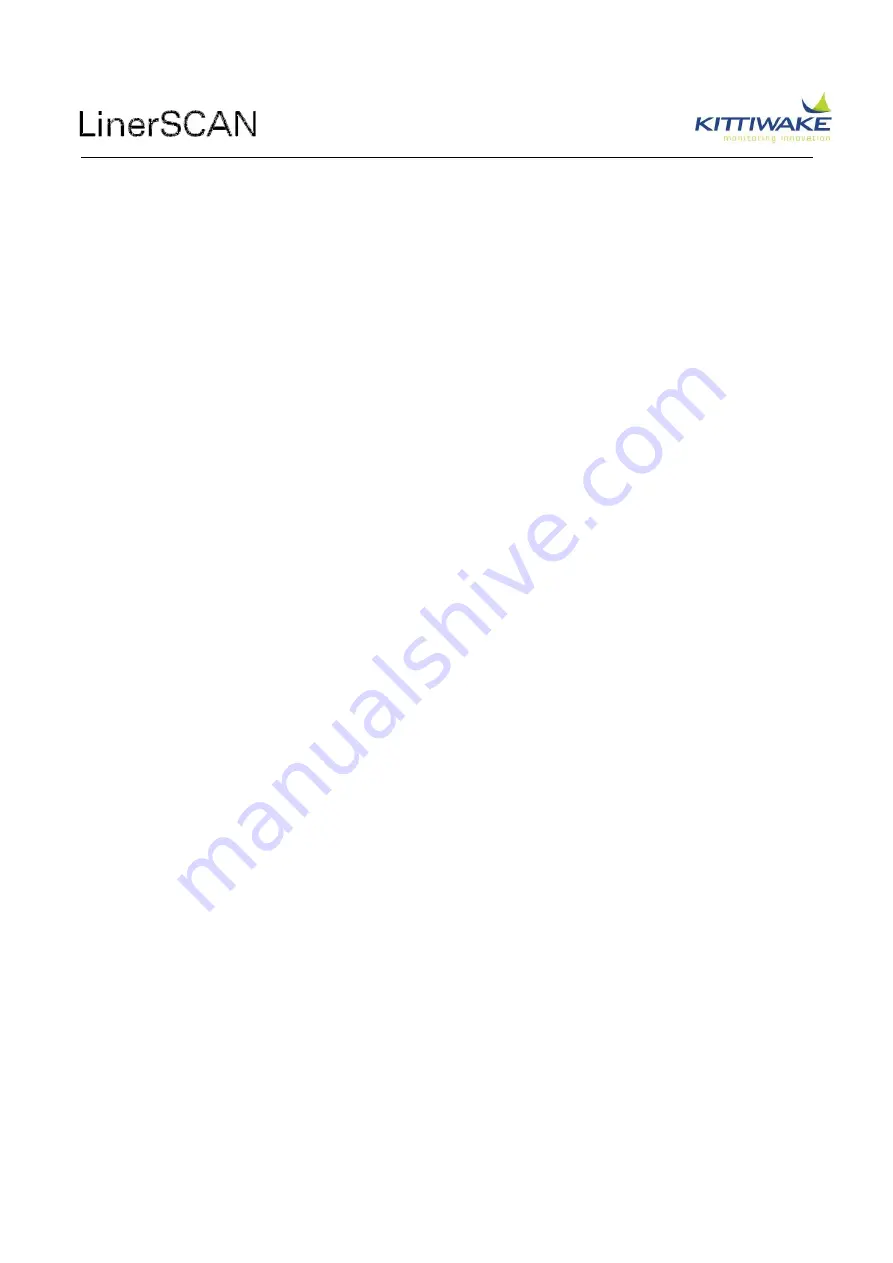
MA-K17510-KW LinerSCAN manual ISSUE P.doc
Page 57 of 93
6.1 Introduction
Improvements to the design, operation and maintenance of slow speed diesel engines from the
manufacturers have recently seen impressive claims in reductions of liner wear, cylinder lubricant
feedrate and maintenance.[2,3] This progress has come about from years of research into
understanding the complex parameters which affect the life of the cylinder. But it is common
knowledge that no two pieces of equipment will ever behave exactly the same. For this reason Chief
Engineers will not always follow the newest guidelines or recommendations. Engines are regularly
over lubricated to try to avoid problems like scuffing. This practice can sometimes have the opposite
effect and lead to problems such as bore polishing and also high lubrication costs.
An average container ship can spend US $10,000,000 on cylinder lubrication in its life. If the current
practice on an engine works then it is very hard to move away from it without proof that the changes
are not causing problems. This feedback can currently be made available in the field using on-board
oil analysis equipment or sample based oil analysis from a laboratory. This has proved time and time
again to be a successful way to monitor the engines condition. The main disadvantage is the time
required to take samples and collate the data.
The LinerSCAN system automatically reports the amount of ferrous wear debris in the waste cylinder
lubricant and fulfils this genuine requirement, and crucially fills in the data points between normal
laboratory information.
Wear is very much related to engine parameters, such as speed, load, cylinder lubricant feedrate,
temperature, fuel and lubricant quality etc… The following data shows how quickly issues can arise
and be avoided or at least monitored. It also shows that even with the best laboratory sampling
practices unrepresentative samples could cause false alarms.
It is worth also considering the financial side of the project when the average insurance claim for an
unexpected liner loss is over $250,000.[1]
The following case study data is taken from real slow speed engines all of which are used as main
engines on container or bulk carrier ships. The engines used were either Man B&W or Wartsila/Sulzer.
Summary of Contents for FG-K17401-KW
Page 9: ...MA K17510 KW LinerSCAN manual ISSUE P doc Page 8 of 93 3 Installation Installation ...
Page 34: ...MA K17510 KW LinerSCAN manual ISSUE P doc Page 33 of 93 4 Commissioning Commissioning ...
Page 40: ...MA K17510 KW LinerSCAN manual ISSUE P doc Page 39 of 93 5 Operation Operation Manual ...
Page 89: ...MA K17510 KW LinerSCAN manual ISSUE P doc Page 88 of 93 ...