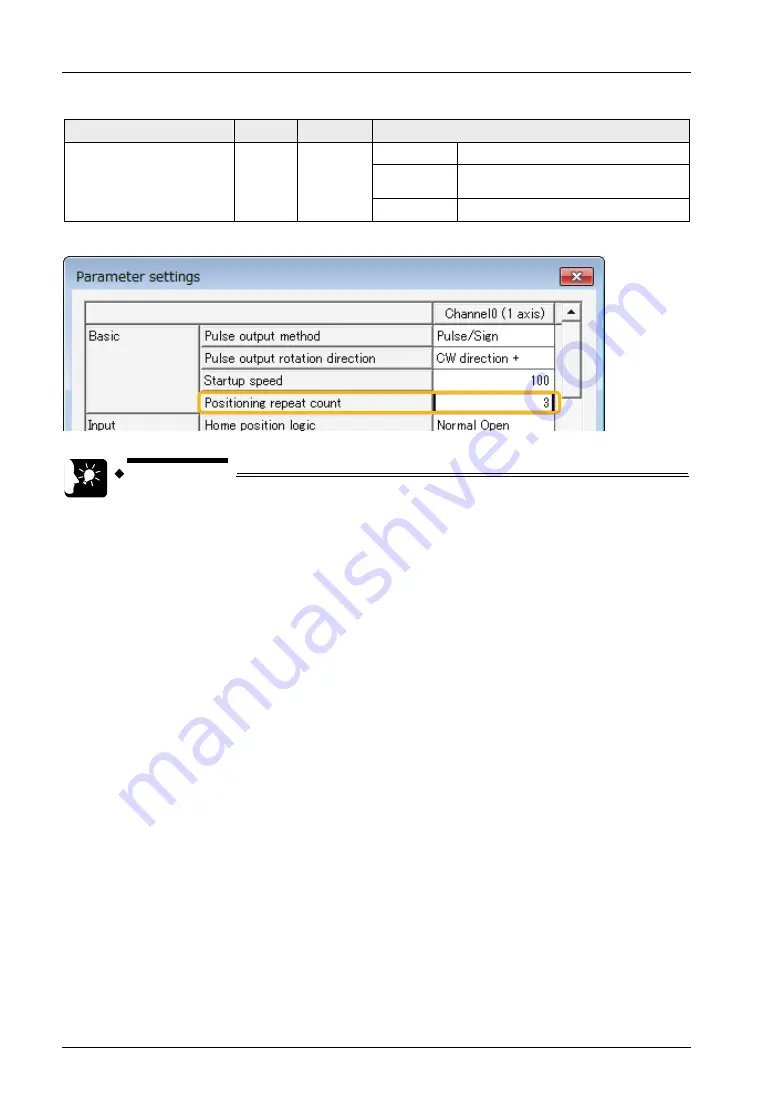
Operation
Patterns
5-30
Configurator PMX setting items
Parameter name
Unit
Default
Settings
Positioning repeat count
times
0
0 or 1
Not repeat an operation.
2 to 254
Repeat an operation for a specified
number of times.
255
Repeat an operation infinitely.
Configurator PMX settings
KEY POINTS
•
When selecting “255: Repeat infinitely” in the parameter of positioning
repeat count, create a program to stop the operation using the deceleration
stop function.
Summary of Contents for FP0H Series
Page 1: ......
Page 11: ...1 Functions of Unit and Restrictions on Combination ...
Page 19: ...2 Wiring ...
Page 23: ...3 Power ON and OFF and Items to Check ...
Page 30: ...Power ON and OFF and Items to Check 3 8 ...
Page 31: ...4 Settings of Control Unit ...
Page 52: ...Settings of Control Unit 4 22 ...
Page 53: ...5 Operation Patterns ...
Page 89: ...6 Operating Characteristics ...
Page 93: ...7 Instruction References ...
Page 124: ...Instruction References 7 32 ...
Page 125: ...8 Troubleshooting ...
Page 133: ...9 PWM Output Function ...
Page 140: ...PWM Output Function 9 8 ...
Page 141: ...10 High speed Counter Function ...
Page 151: ...10 3 High speed Counter Instruction 10 11 MEMO ...
Page 170: ......
Page 171: ...11 FPΣ Mode ...
Page 180: ...FP Mode 11 10 ...
Page 181: ...12 Specifications ...
Page 196: ...Specifications 12 16 ...
Page 198: ......
Page 199: ......
Page 200: ......