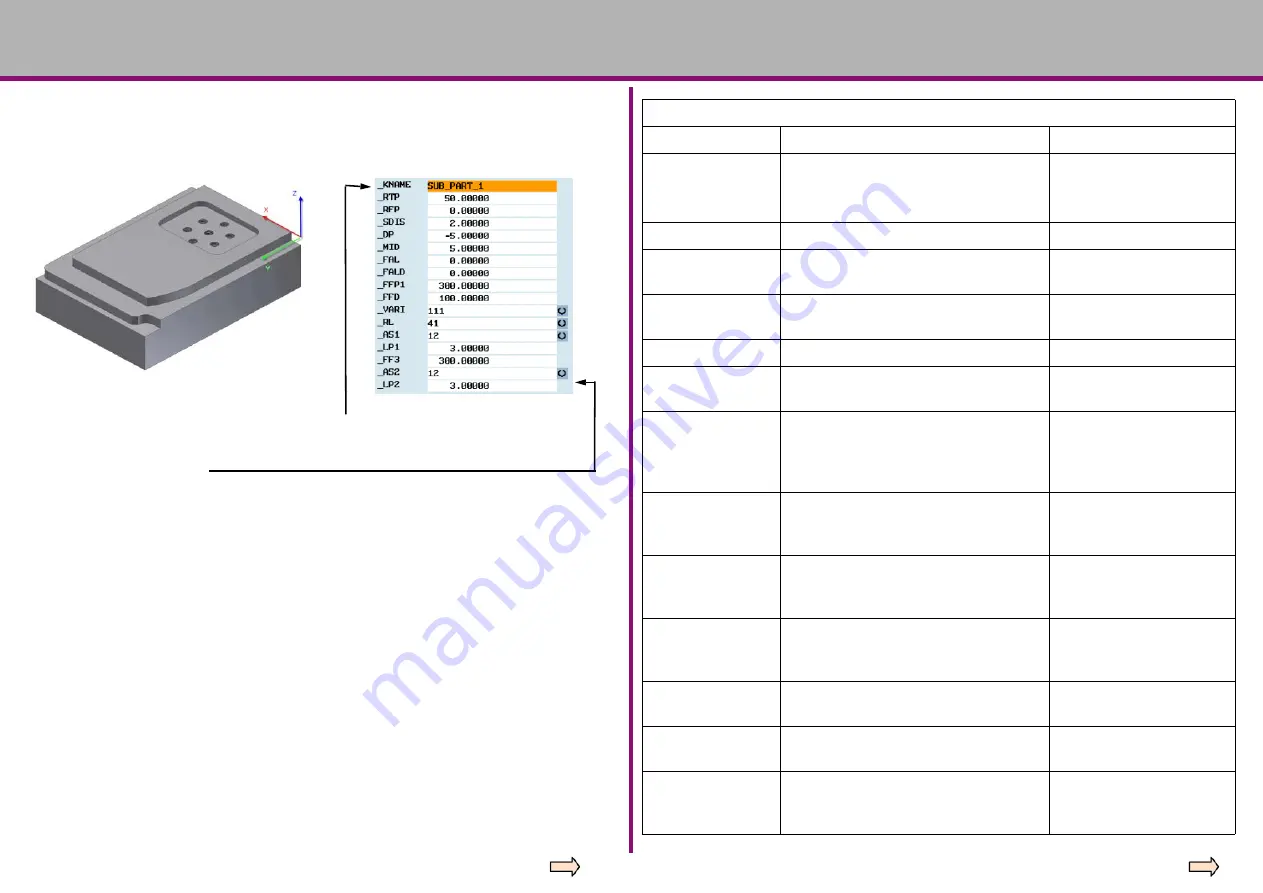
OPTIMUM
M A S C H I N E N - G E R M A N Y
808D
Page 340
Operating and Programming — Milling
Create Part Program Part 2
Brief instruction 808D Milling
Basic Theory
With the “OK” SK, the values and the cycle call are transferred to the part program as
shown below.
actual effect
N245 CYCLE72( "SUB_PART_1", 50.00000, 0.00000, 2.00000, -5.00000,
5.00000, 0.00000, 0.00000, 300.00000, 100.00000, 111, 41, 12, 3.00000,
300.00000, 12, 3.00000)
For descriptions of RTP, RFP, SDIS and DP, please see
Parameters Meanings
Remarks
KNAME=
CONT1:CONT1_E
Set the name of the contour
subprogram as “CONT1”
(“:CONT1_E” is automatically created)
The first two positions of
the program name must
be letters
MID=5
The maximal feed depth is 5 mm
FAL=0
Finishing allowance at the contour
side is 0 mm
FALD=0
Finishing allowance at the bottom
plane is 0 mm
FFP1=300
Tool feed rate on plane is 300 mm/min
FFD=100
Feed rate after inserting the tool in the
material is 100 mm/min
VARI=111
Use G1 to perform rough machining,
and back to the depth defined by the
RTP+SDIS at the completion of the
contour
For other parameters,
please refer to the
standard manual
RL=41(absolute
value)
PL=41
→
use G41 to make tool
compensation on the left side of the
contour
PL=40
→
G40,
PL=42
→
G42
AS1=12
Approach the contour along the 1/4
circle on the path in space
For other parameters,
please refer to the
standard manual
LP1=3
The radius of the approaching circle is
20 mm
The length of the
approaching path is along
the line to approach
FF3=300
The feed rate during retraction of the
path is 300 mm/min
AS2=12
Return along the 1/4 circle on the path
in space
Parameter explanations
are the same as for AS1
LP2=3
The radius of the return circle is 20
mm
The length of the
returning path is along the
line to approach